Digitalisation Of A Production Environment
Name of demonstration
Digitalisation Of A Production Environment
Main objective
This demonstrator illustrates how to create a digital copy of a production environment. It will also show how robots and other machines can be connected and controlled from the same industrial information server.
Short description
Factories of the future will face increasing demands for non-stop production, accompanied with high flexibility and safety requirements. This implies an important future market, for instant services dealing with support, error diagnostics and reconfiguration of industrial robot systems. These advances can be achieved by utilizing IoT in every stage of the production process in a factory. Based on the collected data, decisions can be made even from distant locations.
Owner of the demonstrator
The Arctic University of Norway
Responsible person
Scientific fellow. M.Sc
Halldor Arnarson
Department of Industrial Engineering
UiT the Arctic University of Norway
NACE
C33.2.0 - Installation of industrial machinery and equipment
Keywords
Simulation software, IoT, Digital twin, Remote control , VR robotic programming.
Potential users
Production systems, Factories
Benefits for the users
– The main benefits of the demonstrator revolve around increased flexibility by digitalising a production environment and connecting robots and other machines together.
– A digital twin can be used for testing, validating, and refining assumptions, which leads to …
– Data from a production system can give an enhanced insight into the performance of the system for improved visualisation.
– It creates a unified method for robot programming which simplifies and standardises the procedure of robot programming. Which again creates a friendly and simple environment for training of employees.
– The system is made to be flexible and scalable, where robot arms, mobile robots and other machines can be added or removed to the IoT system without compromising the current system.
– The use case creates an agile method for connecting robots and other machines together through a standardized industrial information server (OPC UA standard).
Innovation
This demonstrator allows for machine-to-machine communication which allows for collaboration between robots and other machines from different brands. Instead of going to each robot controller and programming the robots separately. This demonstrator creates a unified method of robot programming, as well as using new methods for programming.
A digital model of a production environment can be used for optimisation and modification of the environment.
Risks and limitations
- Some robots have closed system and don’t allow for control from an external computer. This demonstrator requires an open robot controller.
- Since robots are connected through the internet, extra work and consideration on cybersecurity should be done.
- The mobile robot used to scan the production environment does not have the highest accuracy and therefore the digital twin module does not produce the highest accuracy.
Technology readiness level
6 - Safety approved sensors and systems are commercially available
Sectors of application
Aerospace, Automotive, Manufacturing, Supply chain and logistics.
Potential sectors of application
Production and Healthcare
Patents / Licenses / Copyrights
The module is made for the purpose of providing a proof-of-concept. The designed structure, upsetting, and its associated files are free of charge for internal and external use during the project period. The software and other related files are under the standard MIT license: Copyright 2021 The Arctic University of Norway (UiT) Permission is hereby granted, free of charge, to any person obtaining a copy of this software and associated documentation files (the "Software"), to deal in the Software without restriction, including without limitation the rights to use, copy, modify, merge, publish, distribute, sublicense, and/or sell copies of the Software, and to permit persons to whom the Software is furnished to do so, subject to the following conditions: The above copyright notice and this permission notice shall be included in all copies or substantial portions of the Software. THE SOFTWARE IS PROVIDED "AS IS", WITHOUT WARRANTY OF ANY KIND, EXPRESS OR IMPLIED, INCLUDING BUT NOT LIMITED TO THE WARRANTIES OF MERCHANTABILITY, FITNESS FOR A PARTICULAR PURPOSE AND NONINFRINGEMENT. IN NO EVENT SHALL THE AUTHORS OR COPYRIGHT HOLDERS BE LIABLE FOR ANY CLAIM, DAMAGES OR OTHER LIABILITY, WHETHER IN AN ACTION OF CONTRACT, TORT OR OTHERWISE, ARISING FROM, OUT OF OR IN CONNECTION WITH THE SOFTWARE OR THE USE OR OTHER DEALINGS IN THE SOFTWARE.
Hardware / Software
Hardware:
Industrial robot
Robot arm
External computer
Software:
Visual Components premium 4.2
OPC UA
Visual Components Experience
Steam VR
Trainings
The training material is under development: http://heinlein.mech.upatras.gr/trinity/use-case-6/
Photos

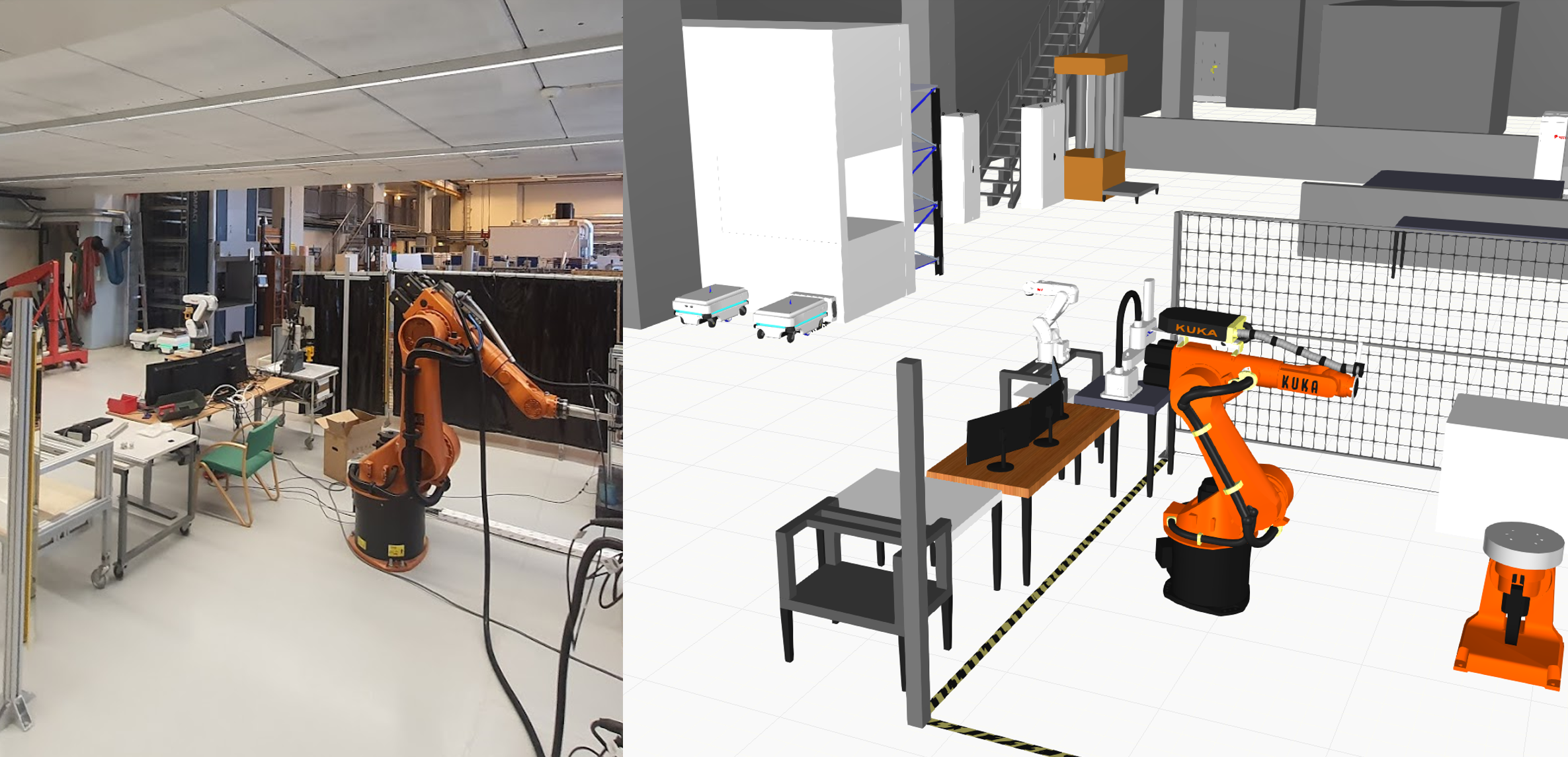
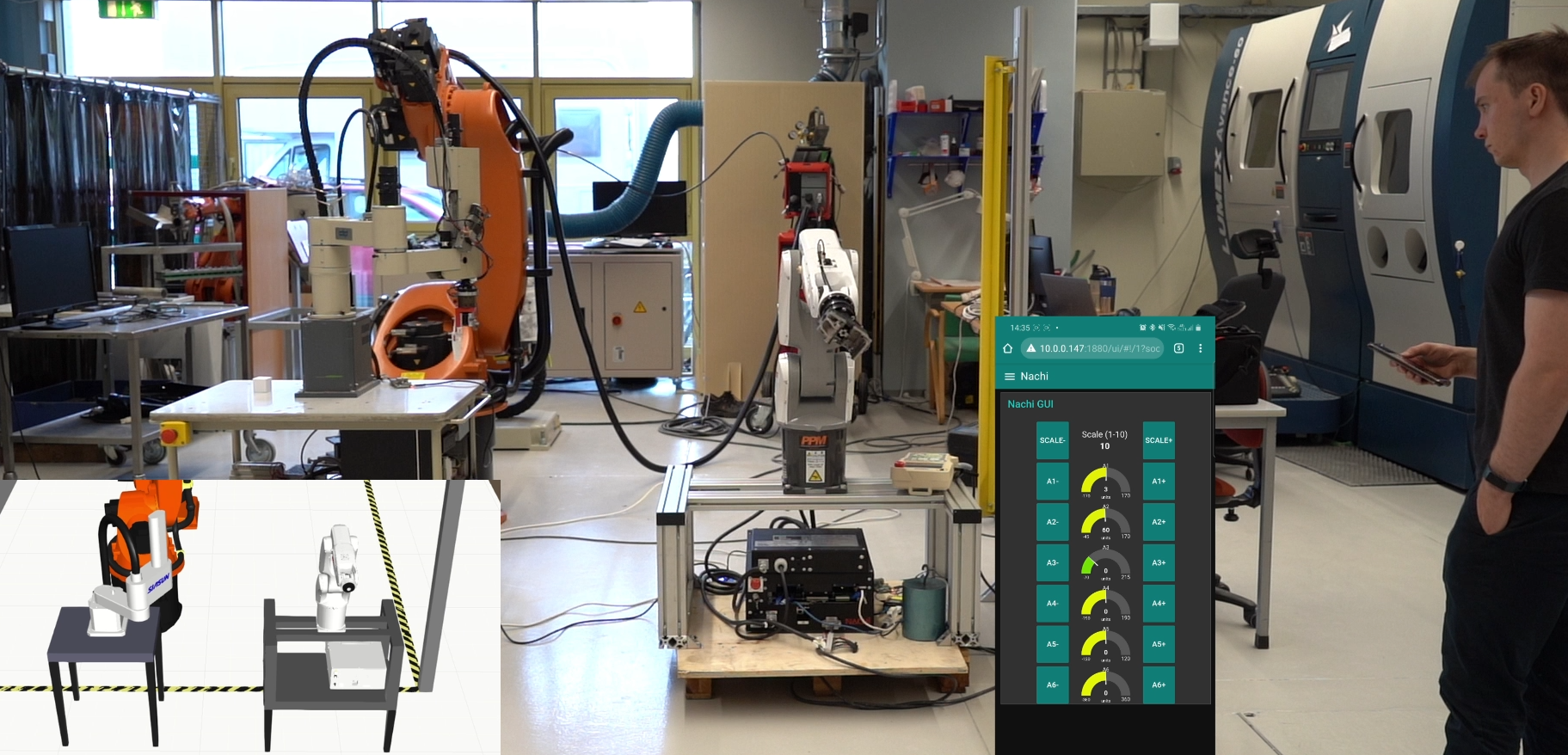
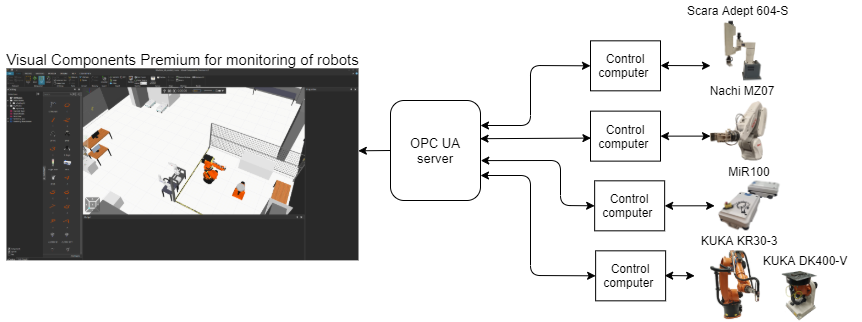
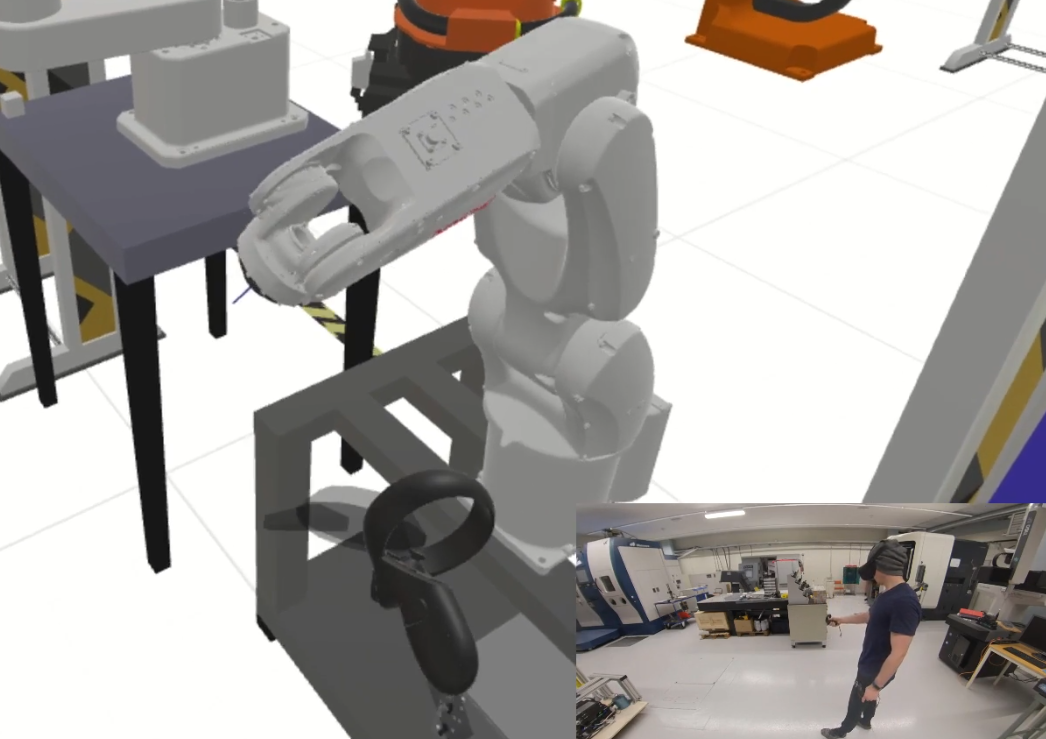
Connecting Virtual Model With The Physical Model
The module describes how robots and other machines can be connected together, through an information server...
LEARN MORE
Rapid Mapping Of A Production System In A Virtual Environment
The module presents a method for rapid mapping of a production system in a virtual environment. The virtual...
LEARN MORE
Remote Control Of Industrial Robots
The module offers a method to control a general industrial robot remotely. This module offers a robot contr...
LEARN MORE
Virtual reality programming of a manufacturing cell
The main functionality of the module is to utilize VR for both robot programming and system programming. Th...
LEARN MORE
Trainings
To learn more about the solution, click on the link below to access the training on the Moodle platform
Production flow simulation/supervision