Digital Twin ⇌ Plan Visualise Control
Main functionalities
Our team has created intuitive software tools that seamlessly merge teaching, simulation and control of industrial robots. The result is an intuitive and versatile automation platform. The platform is agnostic to robot vendor and modular by design. Users can now manage, monitor and configure their robot cell from one software platform. No more jumping between expensive proprietary software applications, no more custom post-processors and no more commissioning online with a pendant. All this can be performed remotely from one software platform.
Technical specifications
- Industrial PC
- Ubuntu 20.04
- ROS Noetic running in a docker container
- Local ethernet network connected to:
- Industrial Robot Controller
- Industrial Raspberry Pi
- Force Sensor (optional)
- 3D Camera (optional)
- HQ Raspberry Pi Camera
Inputs and outputs
Communication runs over the ROS (Robotic Operating System) bus using the TCP/IP protocol. An external axis servo operates over CANopen via a PLC also on the ROS bus. The two schematics attached show the technology stack overview and inputs/outputs. The key is as follows:
Red : ROS software
Green : Configuration files
Yellow : Human machine interface
Orange : Robot hardware
Blue : Hardware peripherals (e.g. IOT devices)
Formats and standards
Formats: ROS, ROS-I, TCP/IP, CANopen
Standards: IEC 61508 (Functional Safety of Electrical / Electronic / Programmable Electronic Safety-related Systems)
Training material
undefined
Owner (organization)
Rivelin Robotics
Documents
Tech stack schematic
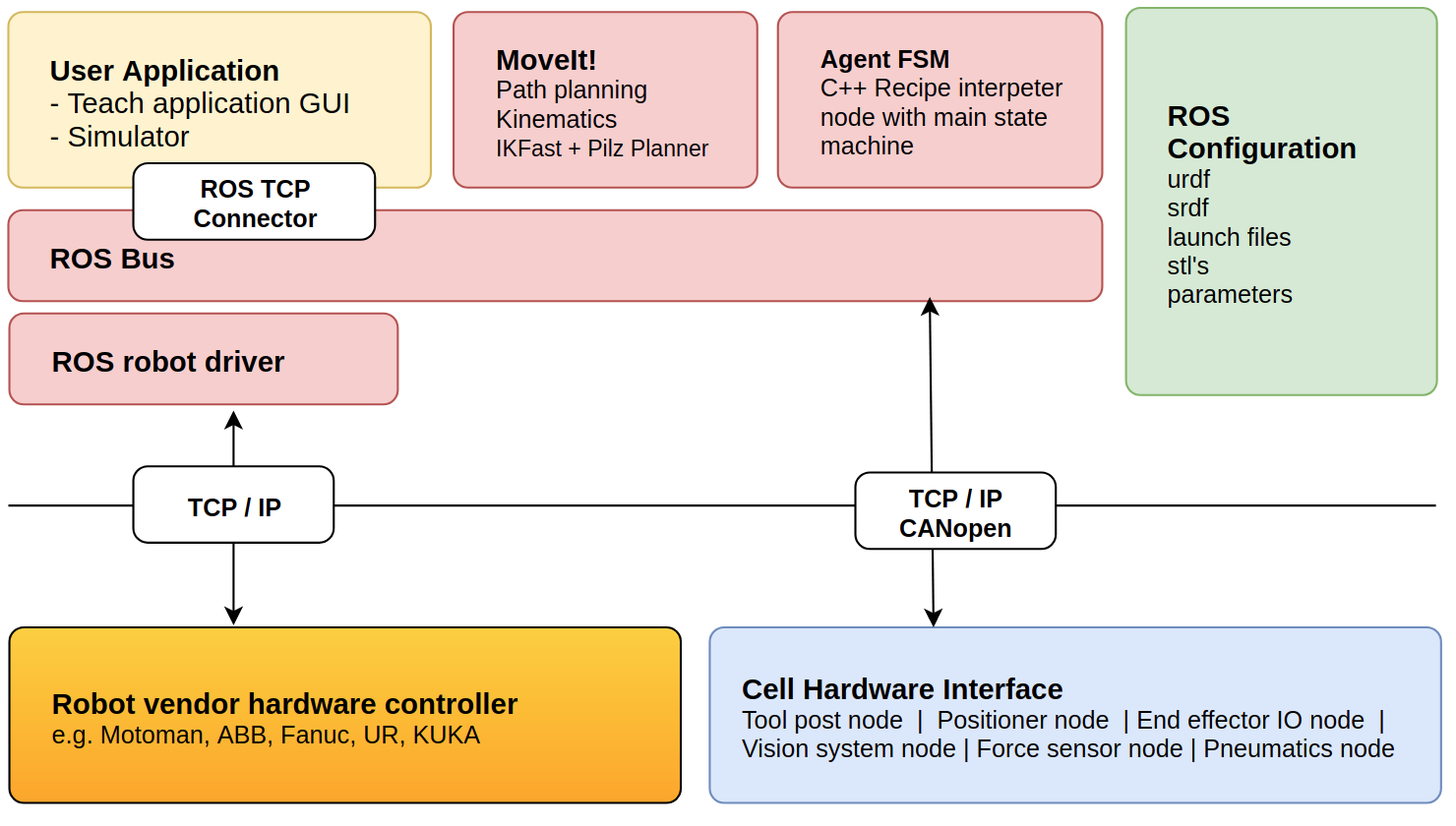
Architecture schematic
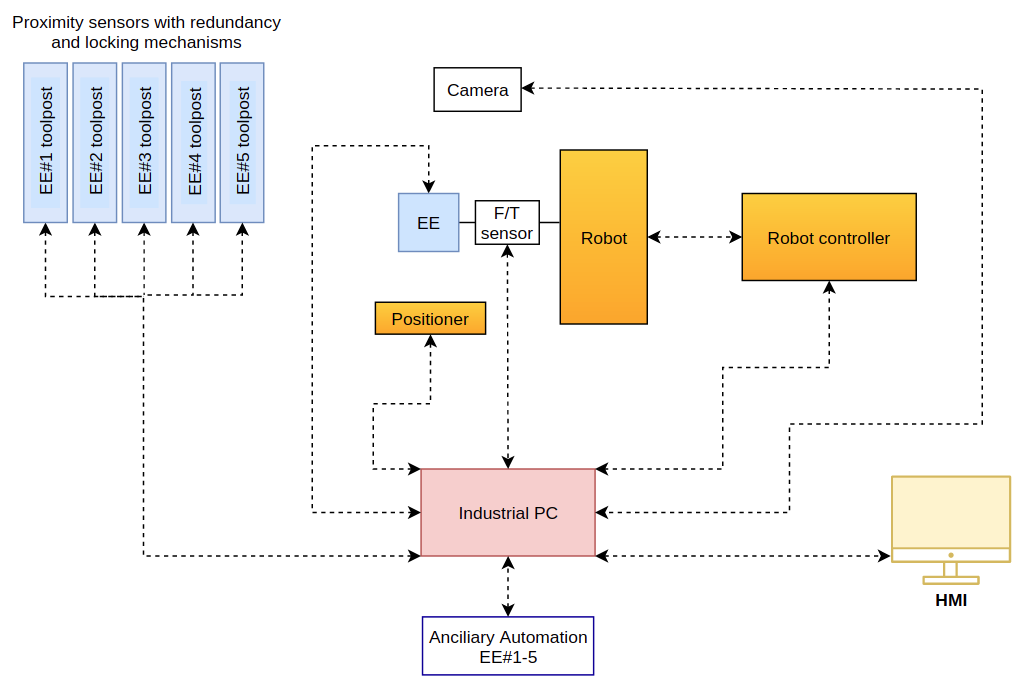
Digital Twin
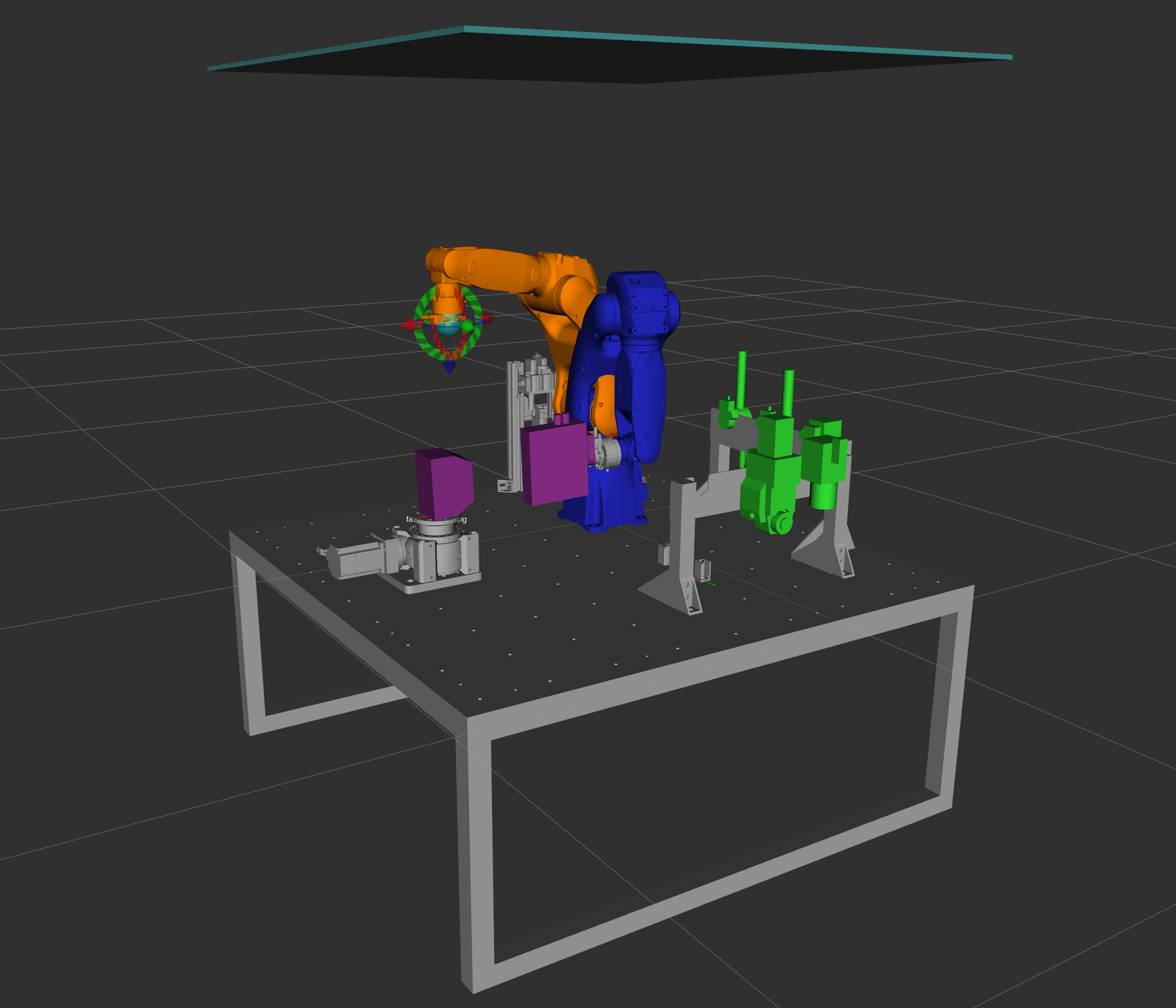