TRAining of an INdustrial MANipulator Using the MAGOS Platform – TRAINMAN-MAGOS (Classification: Robotics, haptic-technology, robotic development time saving)
Name of demonstration
TRAining of an INdustrial MANipulator Using the MAGOS Platform – TRAINMAN-MAGOS (Classification: Robotics, haptic-technology, robotic development time saving)
Main objective
TRAINMAN-MAGOS is a haptic-based solution which transforms the gathered hand movements into a tangible set of instructions to a set of robot and gripper, which can decrease the development time of robotic implementations in high dexterity process operations. Moreover, this tool can register and exploit this skilled knowledge.
Short description
TRAINMAN-MAGOS is a system composed by a haptic-glove, a robot and a gripper. It is function is to translate hand movements performed with the haptic glove into a set of instructions. These instructions are then processed by the robot and the gripper, which could reproduce these movements, having thus the possibility to automate high dexterity process operations in which nowadays human intervention is still needed.
This demonstration has received funding from the European Union’s Horizon 2020 research and innovation programme under grant agreement No 825196.
Owner of the demonstrator
MAGOS
Responsible person
Mr. Greg Agriopoulos gagriopoulos@themagos.com
Mr. Vasilapostolos vasilapostolos@themagos.com
Ms. Gema Antequera gema.antequera@ctag.com
Keywords
Robotics, human-robot collaboration, safety, wearables, Collaborative Robotics, Industry 4.0, Augmented Reality.
Benefits for the users
Programming time is reduced: Taking into account that movements are translated into instructions, programmers don’t have to spend hours programming point per point complicated paths to reproduce high dexterity movements, being able to save up to 70% of the time used in the usual programming procedure.
Commissioning time of the robotic application is decreased: Time spent by the robotic technician making fine adjustments is reduced up to 20% due to the high quality of the draft path provided by the glove.
Commissioning expenses are decreased: It is common to damage involved products during adjustments of robotic paths. However, expenses done by these damages are decreased because using TRAINMAN-MAGOS there are less possibilities of making damages than programming the path from scratch. The probability of damaging parts is reduced up to 20% using TRAINMAN-MAGOS.
Skilled knowledge is kept in the company: Expert knowledge normally confined in the hands of a skill operator is in this way kept in company’s know-how, being an important asset of the organization that should be managed and controlled.
Operators’ wellbeing is improved: Automating high-dexterity operations usually means improving operators’ wellbeing by reducing repetitive high-demanding tasks, so they can use their time in more added value activities.
Innovation
In contrast to the usual programming procedures, in which a robotic technician has to specify point per point the path to be followed by a robot, TRAINMAN-MAGOS solution decreases dramatically robotic development time, since movements captured by the glove are translated into a set of instructions which are processed by a set of a robot and a gripper, which are able to reproduce them without the necessity of spending hours defining points position.
In addition, skilled knowledge in hands of skill operators is therefore kept in company’s know-how, which is an important asset to manage in order to train apprenticeship operators or to improve a specific process.
Moreover, with this system is possible to save commissioning time and expenses due to the high quality of the draft path provided by the glove, (which would not be possible if programming would be done from scratch as in the usual programming procedure).
Risks and limitations
Using data only from the first phalange and not from all phalanges (gripper limitation): All data provided by the MAGOS glove was from the first phalange, (the base of the finger), since this is the only degree of freedom that can be controlled by the 3-finger Robotiq gripper. Using data from the third phalange would be very complicated to adapt to gripper’s movements. Using data from only three fingers and not all fingers (gripper limitation): As the gripper used in this project was the 3-finger Robotiq gripper, data came only from 3 fingers (the thumb, the index and the middle finger). Gripper weight limitation: As the gripper has a fingertip payload limitation of 2,5 Kg, a support had to be created in the window glass model in order to get stability. In addition, gripper's pressure had to be at maximum to pick the window model, not having thus the possibility of using glove's pressure sensors to study in a more accurate way which pressure would be suitable to perform assembly movements. Units and axes adapted in an external software: Units and axes had to be adapted in an external simulator, not being able to integrate it in robot’s software.
Technology readiness level
7 - System model in operational environment
Sectors of application
AUTOMOTIVE INDUSTRY: Car manufacturers can have much profit using TRAINMAN-MAGOS solution because this system saves robotic development time, which is very important nowadays since both automation and time are being more and more crucial in the automotive sector. Therefore, time saved using TRAINMAN-MAGOS could be used to automate other operations. In addition, car manufacturers can preserve skilled knowledge to train inexperienced operators or to improve their processes. , Welding industry: cases that robotic programming is inevitable or too difficult, Oil & Gas: cases that robotic programming is inevitable or too difficult, Industry 4.0: cases that robotic programming is inevitable or too difficult.
Potential sectors of application
TEXTILE INDUSTRY: Nowadays, some textile brands prefer to manufacture their garments by hand because the quality of stitching is much better than automated stitches done by a robot. However, with TRAINMAN-MAGOS solution, stitching could be automated having the same quality as the by-hand stitches since robots could perform the same paths performed by tailors' hands. They would have much more precision when stitching. HEALTH SECTOR: TRAINMAN-MAGOS would be very useful to automate very accurate movements in complicated operations which highly qualified professionals with high dexterity are required. In addition, the TRAINMAN-MAGOS solution would be also very helpful to train new surgeons who have just been graduated.
Patents / Licenses / Copyrights
Hardware / Software
Hardware:
MAGOS glove: Sensorized haptic glove providing finger tracking, hand orientation tracking and indoor localization, to be used to monitor the hands of a skilled operator performing, in this case, the assembly of a side car window glass in a car door.
3-Finger Robotiq gripper: This was the gripper chosen to automate the assembly of the side car window glass. Therefore, the gripper is the physical interface between the robot arm and the window model reproducing worker’s fingers movements during the assembly.
KUKA LBR IIWA 14 R820: This was the collaborative robot used to perform the assembly, reproducing worker’s arm during the conduction of the task.
Software:
Magos core software: for the collection and recording of the users motion data
Robot controller: The collaborative KUKA LBR IIWA 14 R820 is managed by its controller, which provides the programming environment to import and develop robotic solutions, including the development of trajectories, the usage of the gripper, and communication procedures.
Tecnomatix Process Simulate v. 15. This offline simulation software adapts orientation and scales the read values into valid gripper instructions. The path and gripper steps are manually refined in this virtual model by the robotic technician, so that it can be finally implemented in real world afterwards.
Photos
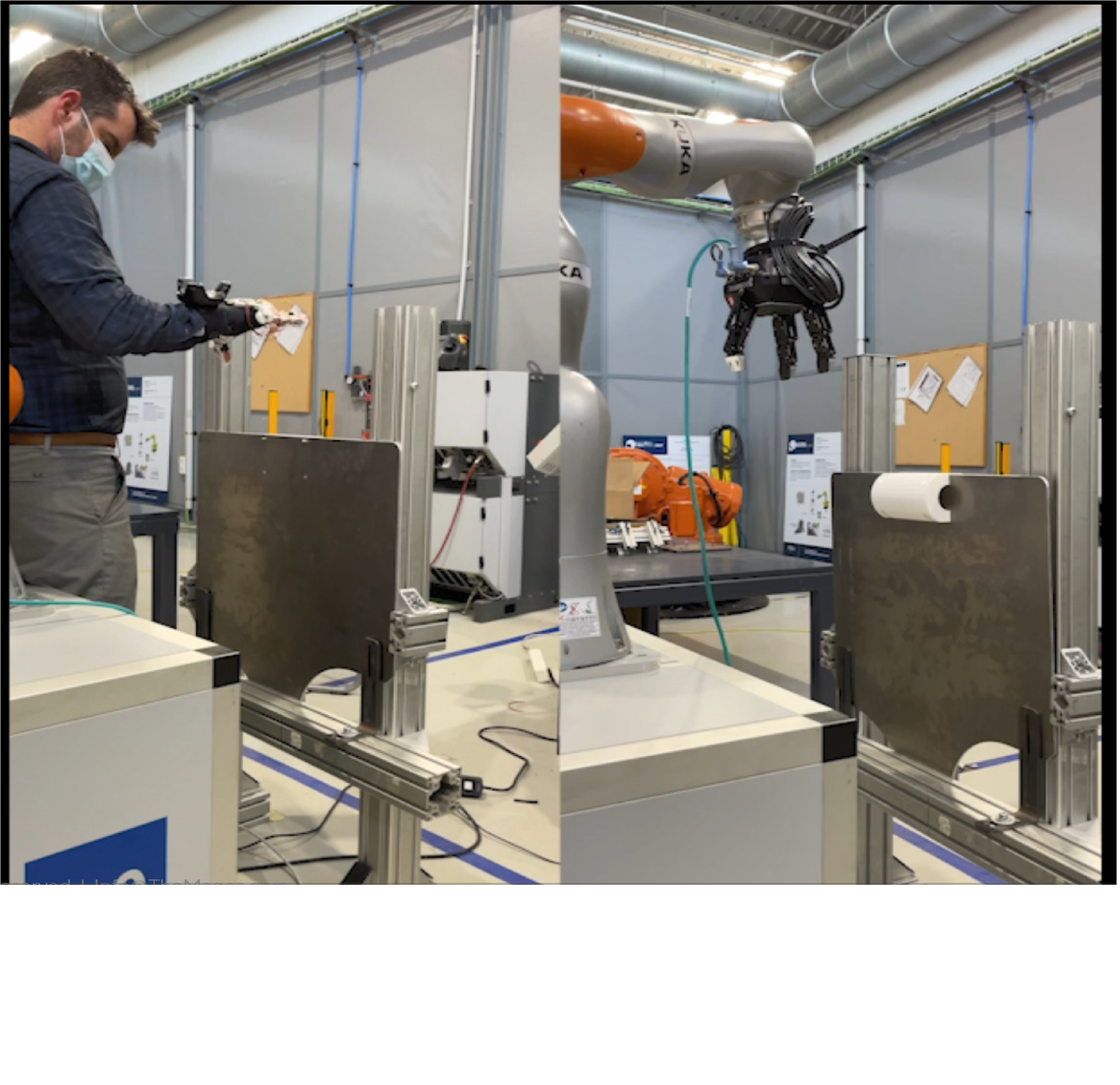
Video
The user (worker) performs high dexterity tasks (grab car door glass replica); Magos records the data. The data are utilized to make the robotic hand perform the same action.
https://www.youtube.com/watch?v=aQ-Yc1_LrQU&ab_channel=infothemagosDemonstration executive summary
https://vimeo.com/615797210/0b304d2e97Connecting Virtual Model With The Physical Model
The module describes how robots and other machines can be connected together, through an information server...
LEARN MORE
Hardware & software interface for robot programming by manual guidance
The module for robot programming by manual guidance enables fast and intuitive programming of new robot mot...
LEARN MORE
Remote Control Of Industrial Robots
The module offers a method to control a general industrial robot remotely. This module offers a robot contr...
LEARN MORE
Wearable AR-based Interaction Interface for HRC
Generation of AR-based interface for human-robot collaboration: Increase the human operator awarene...
LEARN MORE
Trainings
To learn more about the solution, click on the link below to access the training on the Moodle platform
Training of an industrial manipulator using the magos platform