WAAM Clamp: Hybrid Wire Arc Additive Manufacturing to reduce production lead time for the oil and gas industry
Name of demonstration
WAAM Clamp: Hybrid Wire Arc Additive Manufacturing to reduce production lead time for the oil and gas industry
Main objective
The demonstrator shows a new alternative approach for the manufacturing of pipeline clamps or parts, by combining traditional manufacturing technologies with 3D metal printing.
Short description
During the scope of the WAAM Clamp project, a typical repair part for pipelines has been researched and manufactured with Hybrid Wire Arc Additive Manufacturing (WAAM). This technique provides a smart production solution, by combining the advantages of traditional manufacturing (such as precision machining) with the advantages of wire arc additive manufacturing (such as form freedom, high deposition rates and minimal material waste)
This demonstration has received funding from the European Union’s Horizon 2020 research and innovation programme under grant agreement No 825196.
Owner of the demonstrator
MX3D
Responsible person
Thomas Van Glabeke – R&D Manager
thomas@mx3d.com
NACE
C28 - Manufacture of machinery and equipment n.e.c.
Keywords
industrial robotics, Industry 4.0, robotic cell, Process Control, Welding, Additive manufacturing, robotics and automation, Smart Manufacturing, WAAM, Hybrid Manufacturing.
Benefits for the users
Potential benefits:
- reduction of lead time due to faster production
- reduction of material waste by additive manufacturing
- reduction of human errors or highly speciality (welding) skills
- manufacturing automation (vs. human labour)
- on-demand production
- on-site fabrication
Final demonstrator: 60 x 60 x 30 cm
Alloy: E70C 6M H4 (Metal Cored)
Weight: 30 kg printed, 87kg total weight
Savings: at least 80% material savings compared to CNC-manufacturing
Innovation
Current repair processes by clamps typically rely on CNC milling, specialized manual labour, or a combination of both. Each of these processes has its downsides, as CNC milling has high material waste (on average >80% of the original material) and specialized labourers are becoming more scarce.
Hybrid manufacturing provides a smart production solution, by combining the advantages of traditional manufacturing (such as precision machining) with the advantages of wire arc additive manufacturing (such as form freedom, high deposition rates and minimal material waste). This level of hybrid WAAM has not been shown yet at this size, flexibility and inspection requirements before.
The project team managed to reach a high level of assurance for the WAAM clamp demonstrator. BWI (Belgian Welding Institute) tested the materials and confirmed the printed material complied with key TEAM Industries requirements for this material. The MX3D M1 Metal AM System, facility and procedures were qualified by Lloyds Register. TiaT Europe performed non-destructive testing, such as Ultrasonic Testing (UT), Penetrant Testing (PT), Radiographic Testing (RT), showing no relevant defects. TEAM Industries has performed a pressure test, which ran until the maximum pressure of the test installation (i.e. > 60 Bar) without any failure.
Risks and limitations
Further testing and extensive inspection is required to achieve the full certification of this hybrid WAAM pipeline clamp application. As the material (wire), process (with the M1 Metal AM System) and DPS (deposition procedure specification) has been certified already, it is likely that the certification of the full application can be achieved. Furthermore, although the hybrid WAAM has been shown on various size and diverse shapes (including straight pipe and curved pipe), it is to be determined whether is achievable for more size, shapes and materials.
Technology readiness level
7 - System model in operational environment
Sectors of application
Oil & Gas Industry, Chemicals Industry.
Potential sectors of application
Hybrid WAAM can be extended to other industries where a combination of traditional manufacturing and 3D metal printing can be put to good use. Any industry that is using casting, CNC-milling, sheet metal fabrication, or robotic welding could be interested in this application.
Hardware / Software
Hardware:
MX3D M1 Metal AM System: Turn-key solution for the hybrid WAAM process
MX3D MetalXL Control System: to monitor and control the hybrid WAAM process
CNC-machine: to pre-manufacture the sidebars and flange
Software:
CAD program: To design a new clamp shape or edit an existing design
MX3D MetalXL software: To prepare, control and log the hybrid WAAM process
Photos
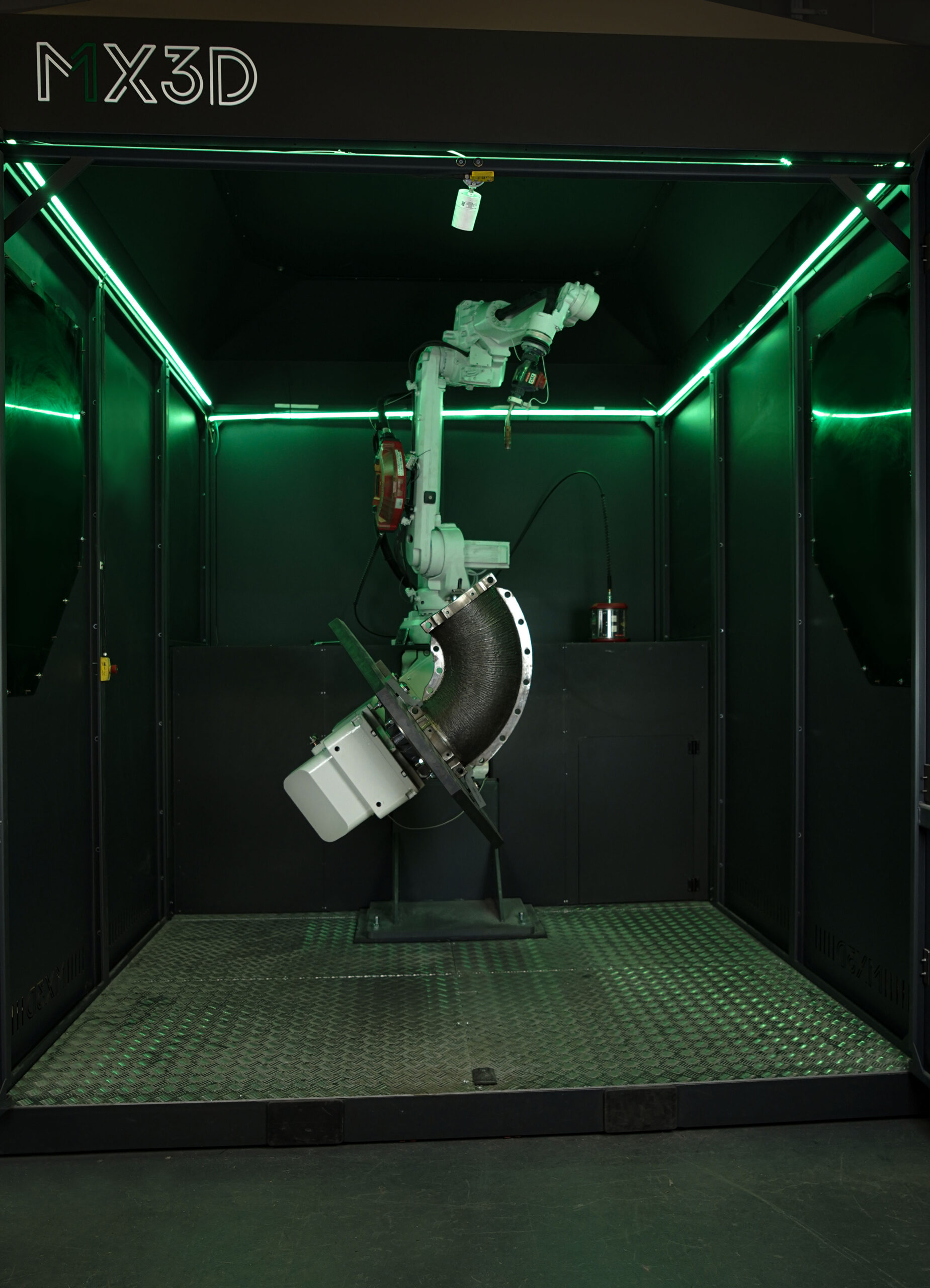
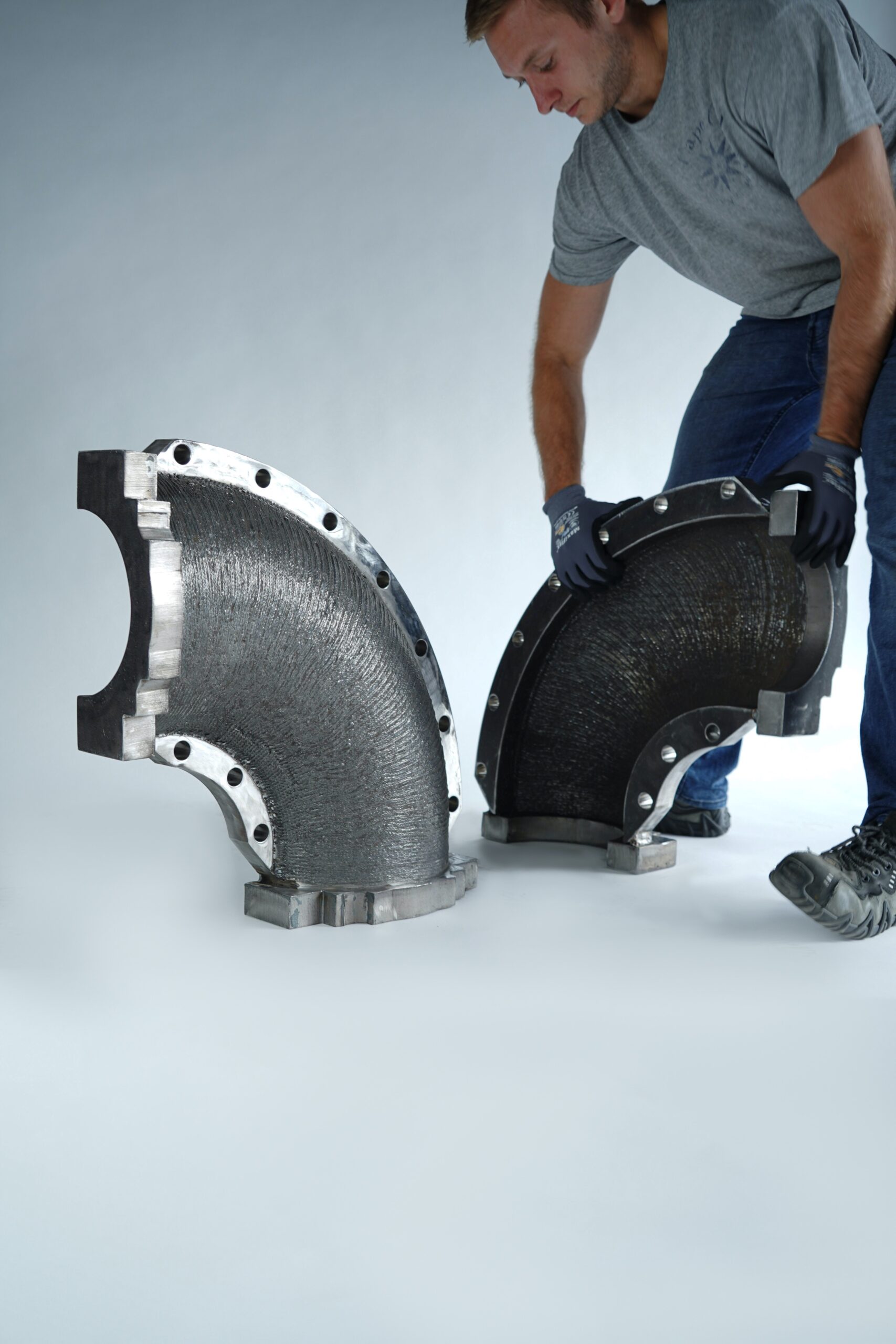
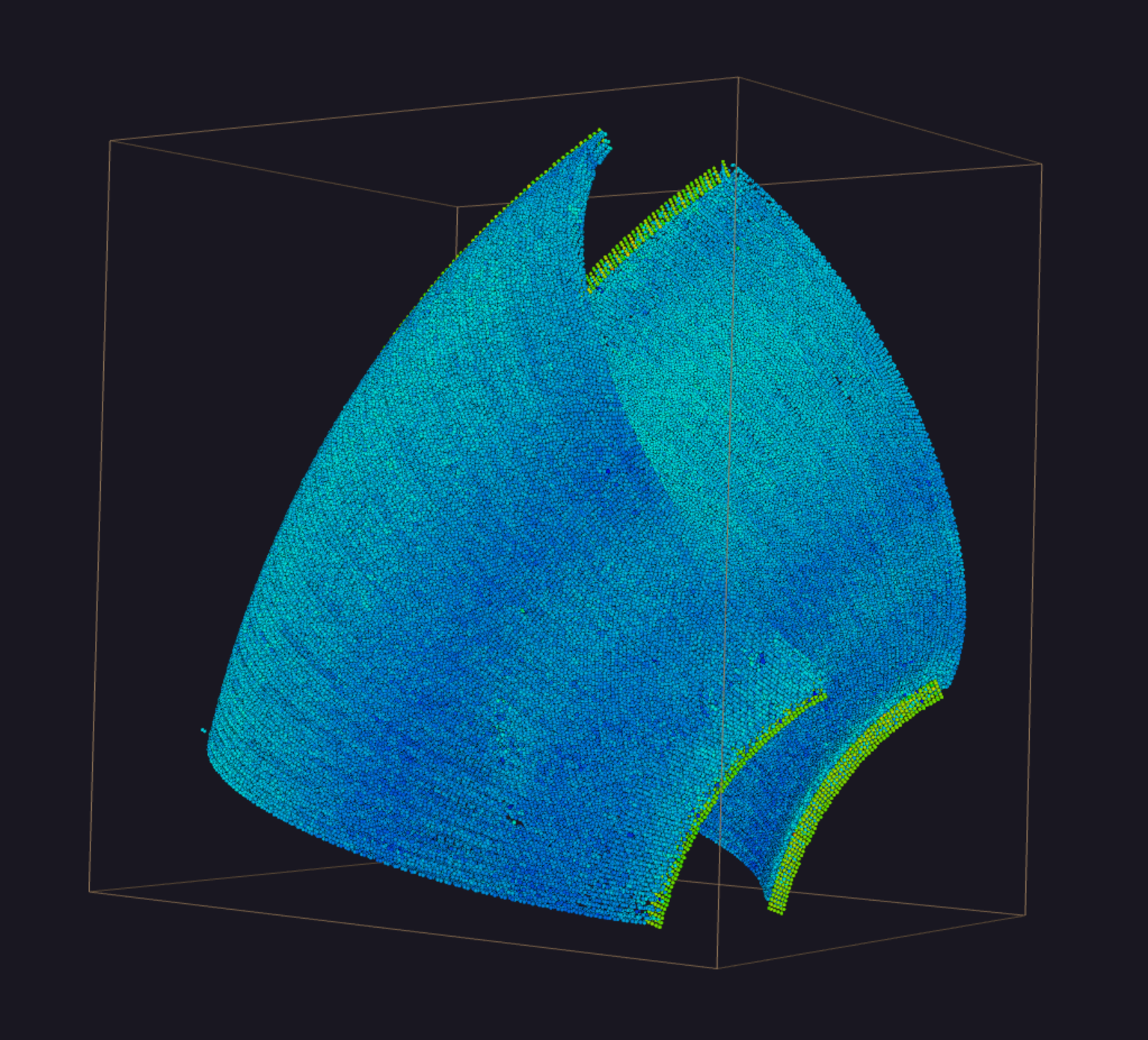
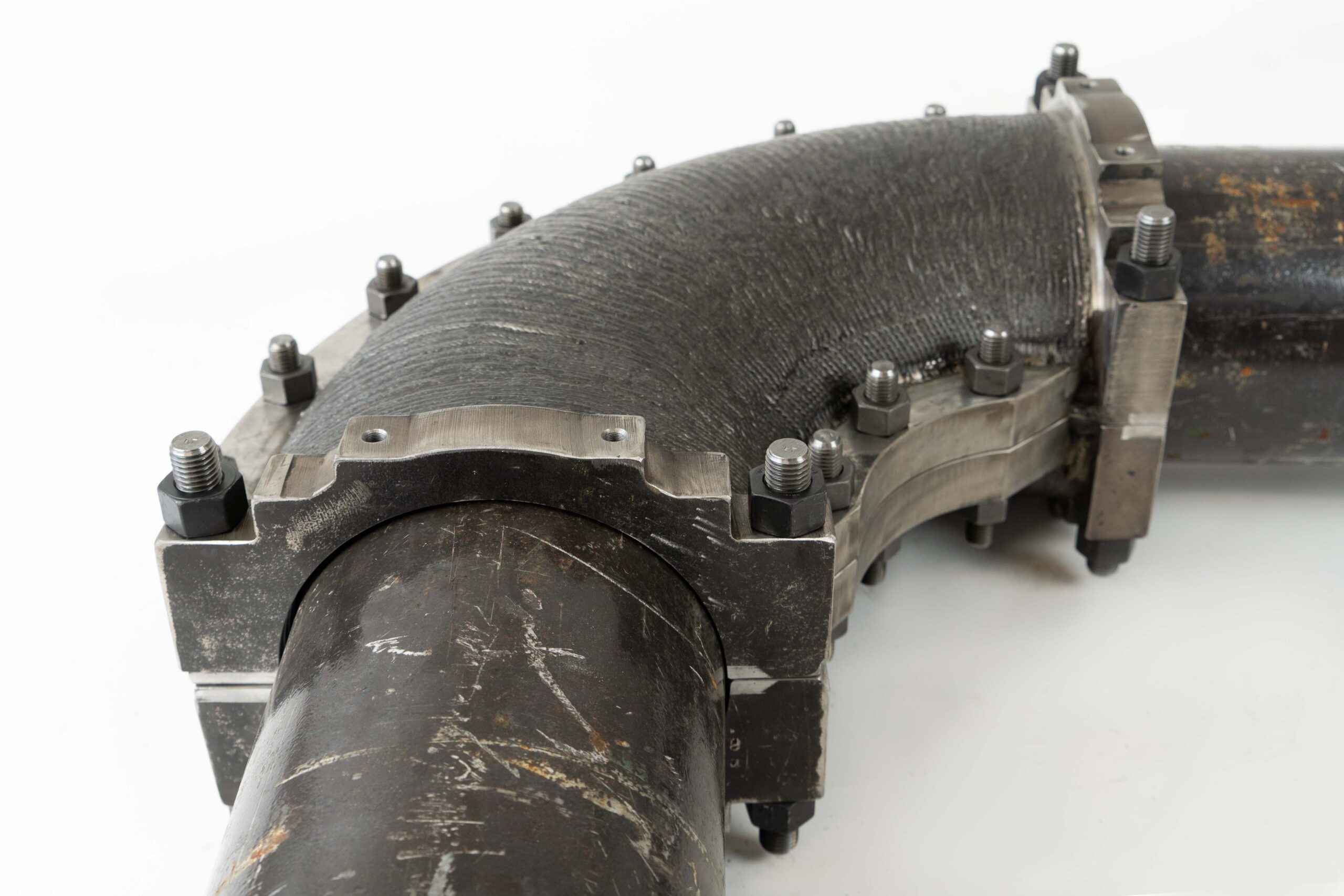
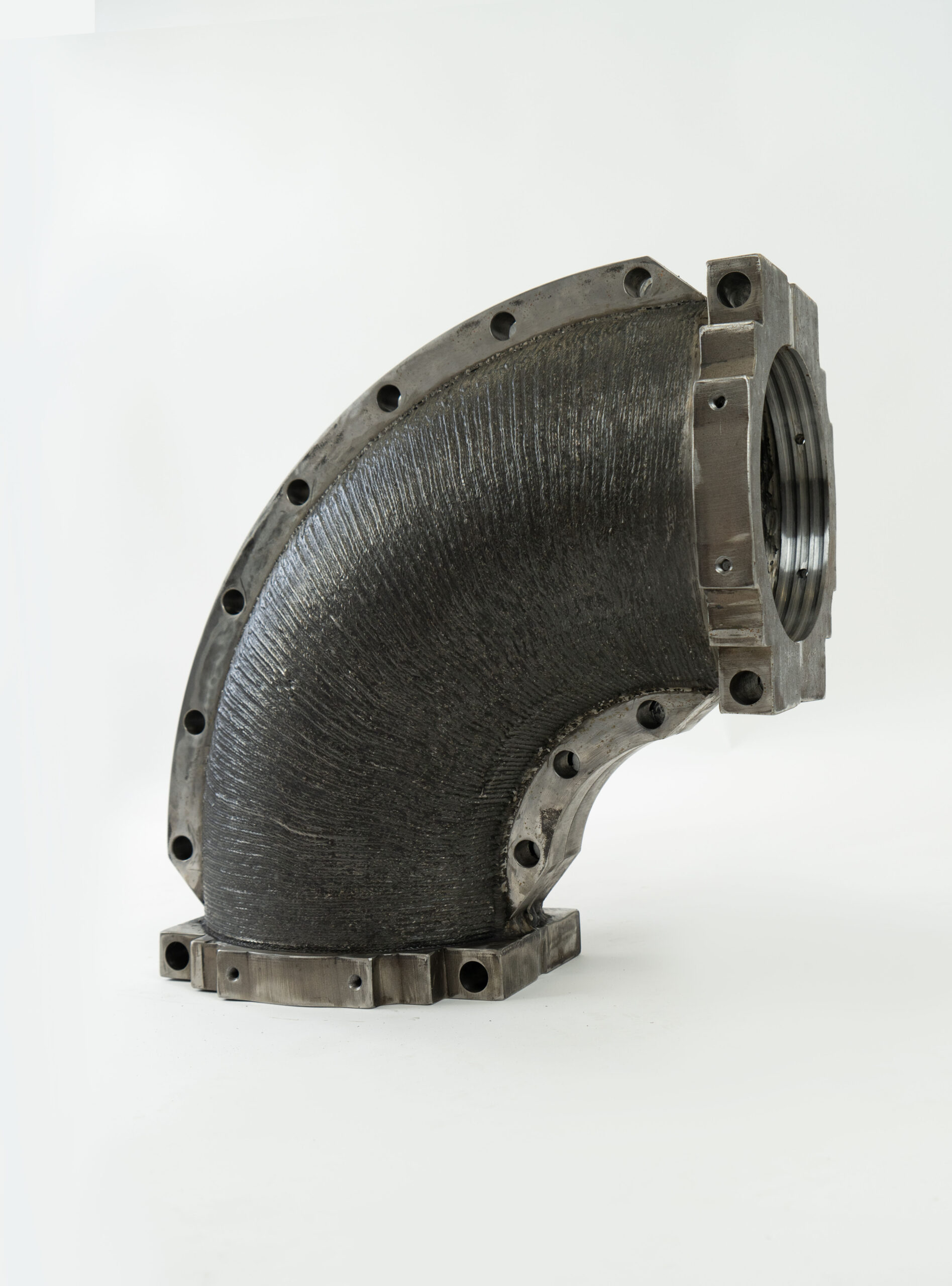
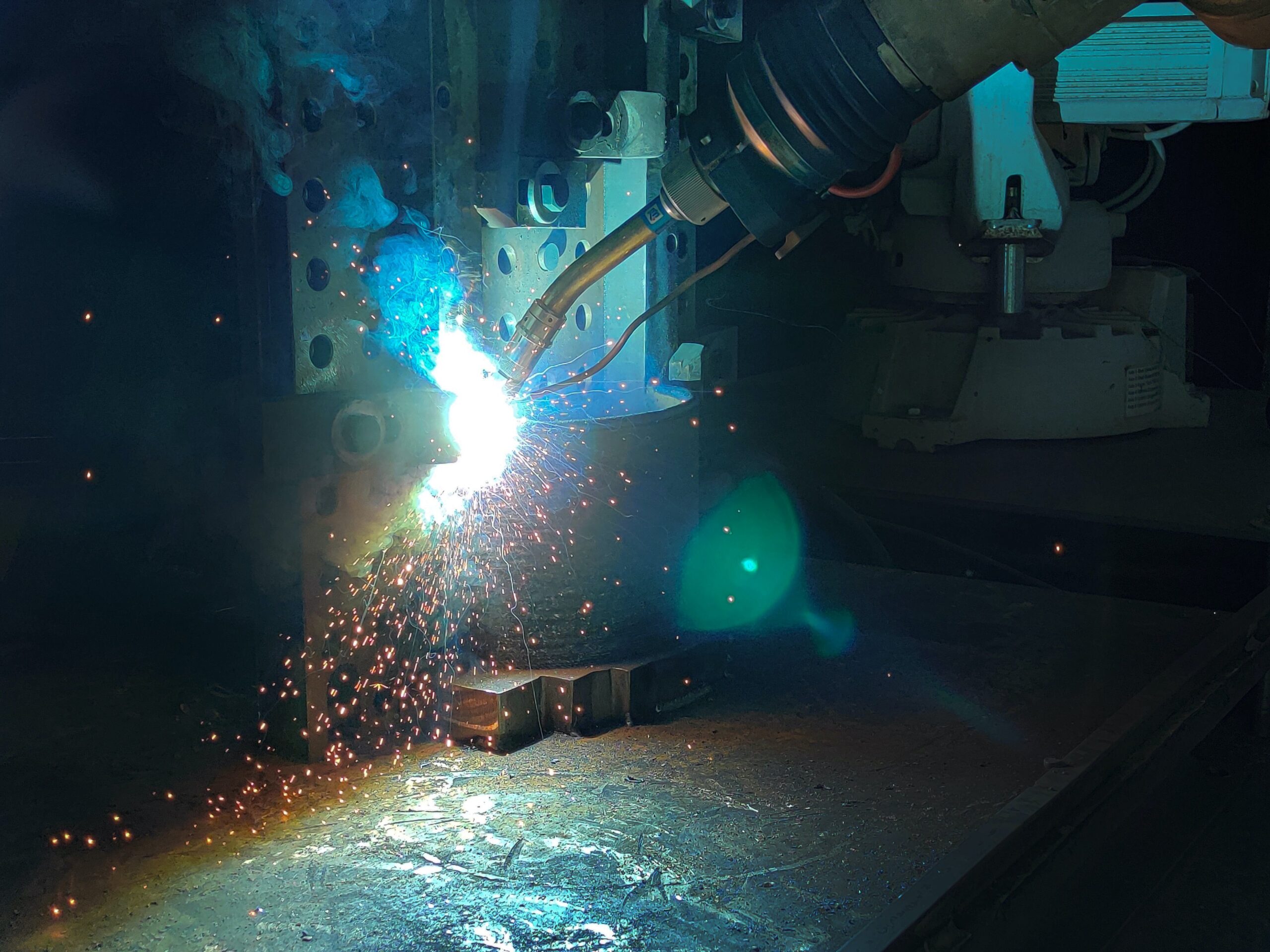
Video
WAAM Clamp, a Hybrid Wire Arc Additive Manufacturing to reduce production lead time for the oil and gas industry
https://youtu.be/J5zEzMvoqbENo modules assigned
Trainings
To learn more about the solution, click on the link below to access the training on the Moodle platform
Waam clamp-wire arc application of metal component linked to additive manufacturing for pipeline repair