Robot Workcell Reconfiguration
Name of demonstration
Robot Workcell Reconfiguration
Main objective
Robot workcell reconfiguration
The ability to reconfigure production cells is crucial for agile production processes where production frequently changes from one product to another. In this demonstrator, we developed a robotic workcell that includes hardware components with passive degrees of freedom to enable quick robot-supported reconfiguration from one product to another without any manual intervention.
Short description
The developed robot workcell is a reconfigurable manufacturing system suitable not only for large production lines but also for low-volume high-diversity production. The workcell consists of the following crucial components to achieve this goal:
– Modular and largely passive hardware components aimed towards cost-effective, autonomous workcell reconfiguration.
– New hardware design methods based on 3-D printing.
– A software backbone based on ROS, which provides modularity of all software components.
– Fast programming of production tasks through kinesthetic guidance and script-based state machine description methods.
– Support for quick workcell reconfiguration by manipulating and exchanging the available hardware components, facilitated by a digital twin.
Owner of the demonstrator
Jožef Stefan Institute
NACE
C - Manufacturing
C26.1 - Manufacture of electronic components and boards
C29.3 - Manufacture of parts and accessories for motor vehicles
C28.2 - Manufacture of other general-purpose machinery
C28.1.5 - Manufacture of bearings, gears, gearing and driving elements
Keywords
Reconfigurable robot systems, Fixtures with passive degrees of freedom, ROS-based workcell control, 3-D printing, Plug and produce.
Potential users
Manufacturing companies with low-volume, high-diversity production
Benefits for the users
The main benefits of the reconfigurable robot workcell for the user include quicker setup times for new production tasks and automated or partly automated reconfiguration from one production task to another. New production tasks can typically be set up in 2-4 days if no new hardware is required or 2-4 weeks if hardware development is necessary. On the other hand, many reconfiguration processes can be performed fully automatically in matters of minutes. If reconfiguration requires manual intervention to, for example, exchange hardware elements, the reconfiguration can be usually accomplished in tens of minutes due to the plug-and-produce connectivity included in the workcell and supported both in hardware and software.
If new hardware is necessary, the setup times usually increase. The system, however, also support such cases through the modular design of components that often need to be adapted. This includes exchangeable gripper fingers, exchangeable fixture clamps, and exchangeable screw bits, which can be quickly manufactured using 3-D printing technologies without the need to replace the rest of the required hardware.
Innovation
The main innovation of the workcell lies in the application of passive reconfigurable components. The main reasoning behind this idea is that a robot workcell already contains an active component, namely a robot(s), which can be used to (re)configure the rest of the robot’s workspace. Thus hardware components with passive degrees of freedom can be manipulated by a robot and moved to a configuration suitable for the desired task. They are a more affordable option compared to high-cost active solutions, which are often prohibitively expensive for manufacturing SMEs that want to keep the costs of automation low. Besides fully automated reconfiguration, the cell also supports manual reconfiguration when full automation is not feasible.
Passive reconfiguration is supplemented by modular hardware and software integrated via ROS https://www.ros.orgThe various tools and features that are available within ROS enabled us to achieve the pursued software reconfigurability of the cell. In our case, software reconfigurability means that it is possible to expand the cell’s functionalities without disrupting the existing software architecture. New software components can be developed without the need to reprogram any of the existing ROS nodes. Hardware modularity is supported by plug-and-produce connectors that enable the fast exchange of hardware components.
Risks and limitations
While the system offers many automated capabilities for workcell reconfiguration, some reconfiguration tasks still require manual intervention. Nevertheless, manual reconfiguration is supported by a simulation system and other software tools that can be used to accelerate the reconfiguration process. Another issue can be the integration with ROS for hardware components that do not have ROS interfaces. For this purpose, we developed a special module called “ROS periphery interface” that enables the integration of hardware without ROS capabilities.
The developed system provides many facilities to support the users when setting up and (re)configuring robotic workcells. While many setup tasks can be performed by users without in-depth knowledge, some of them can only be performed by users with in-depth engineering knowledge. To mitigate this issue, we prepared a classification of setup processes according to the level of required user expertise.
Technology readiness level
6 - Safety approved sensors and systems are commercially available
Sectors of application
Automotive industry: assembly of parts, e.g. assembly of automotive light housings., Electronic industry: Mounting of printed circuit boards (PCBs) on a backplate..
Potential sectors of application
Automotive industry, White goods industry, Aviation industry, Electronics industry, Furniture industry, Manufacturing of machinery
Patents / Licenses / Copyrights
The workcell includes many widely available parts like collaborative robots (Universal robot UR-10 are currently used), tool exchange systems, 3-D cameras, workstations for sensor data processing, simulation, and workcell control and ROS-based control software. It includes open-source software (three-clause BSD licence) as well as closed-source software that is available with the purchase of the corresponding hardware modules. The technology behind passive reconfigurable fixtures has been patented (European patent application Cardan joint, PCT/EP2018/060387). The developed system is not a stand-alone product that can be purchased but needs to be adapted for the respective applications. This is typically done on a project contract basis. The licenses for the workcell control software need to be negotiated within the contract.
Hardware / Software
Hardware:
2 Universal robots UR-10
2 ATI 6-D force-torque sensors
2 Basler cameras with PoE interface
Destaco QC-30 quick tool changer system
Several two-finger grippers
Up to 6 passive reconfigurable fixtures based on Stewart platforms
Passively reconfigurable rotary table
Passive linear guide for relocation of robot bases
Passive rotary table
Tool hanger module
Plug-and-produce connectors
Trolleys with integrated plug-and-produce connectors
Reconfigurable frame based on BoxJoint system
Two Linux workstations with GPUs for workcell control, simulation, and vision processing
Software:
ROS
Trainings
The training material in current being prepared and will be announced when it is ready.
Photos
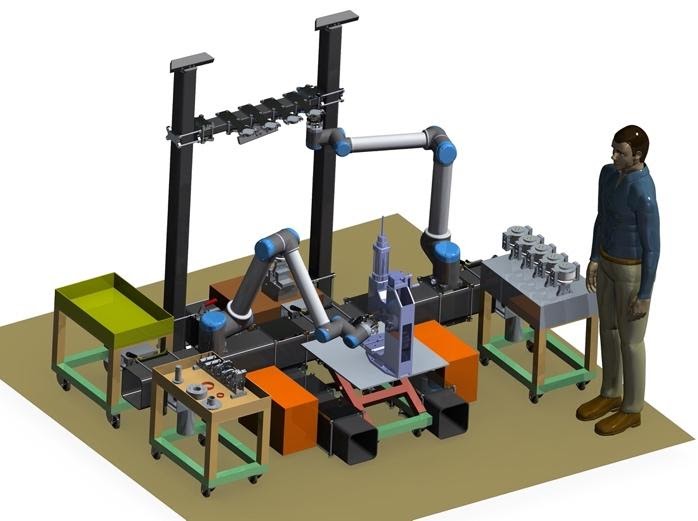
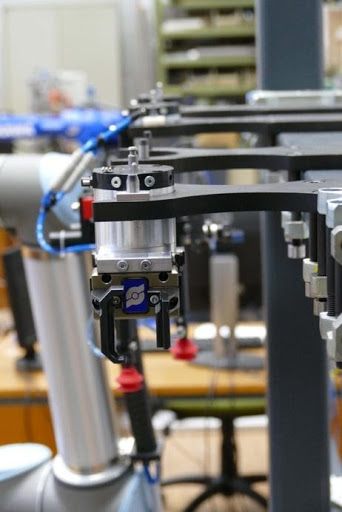
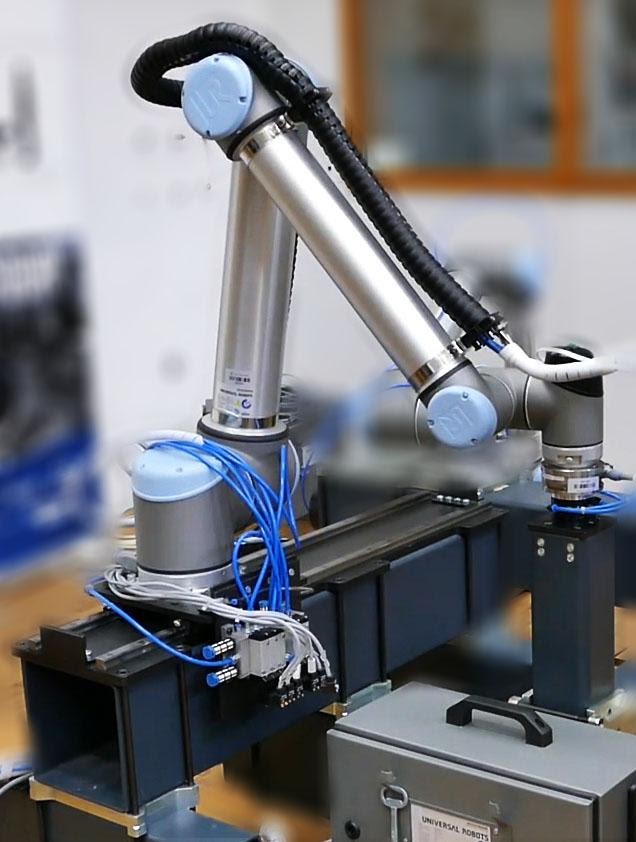
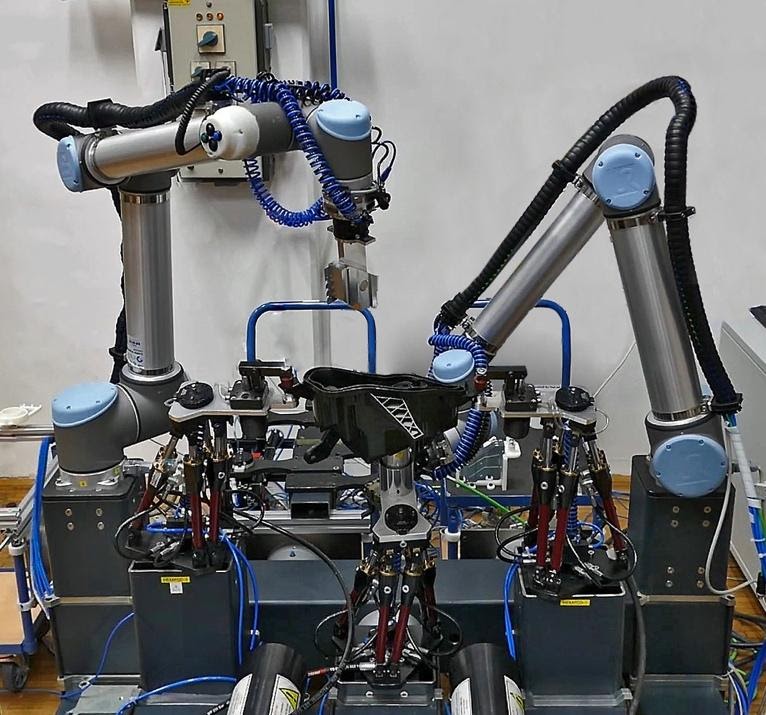
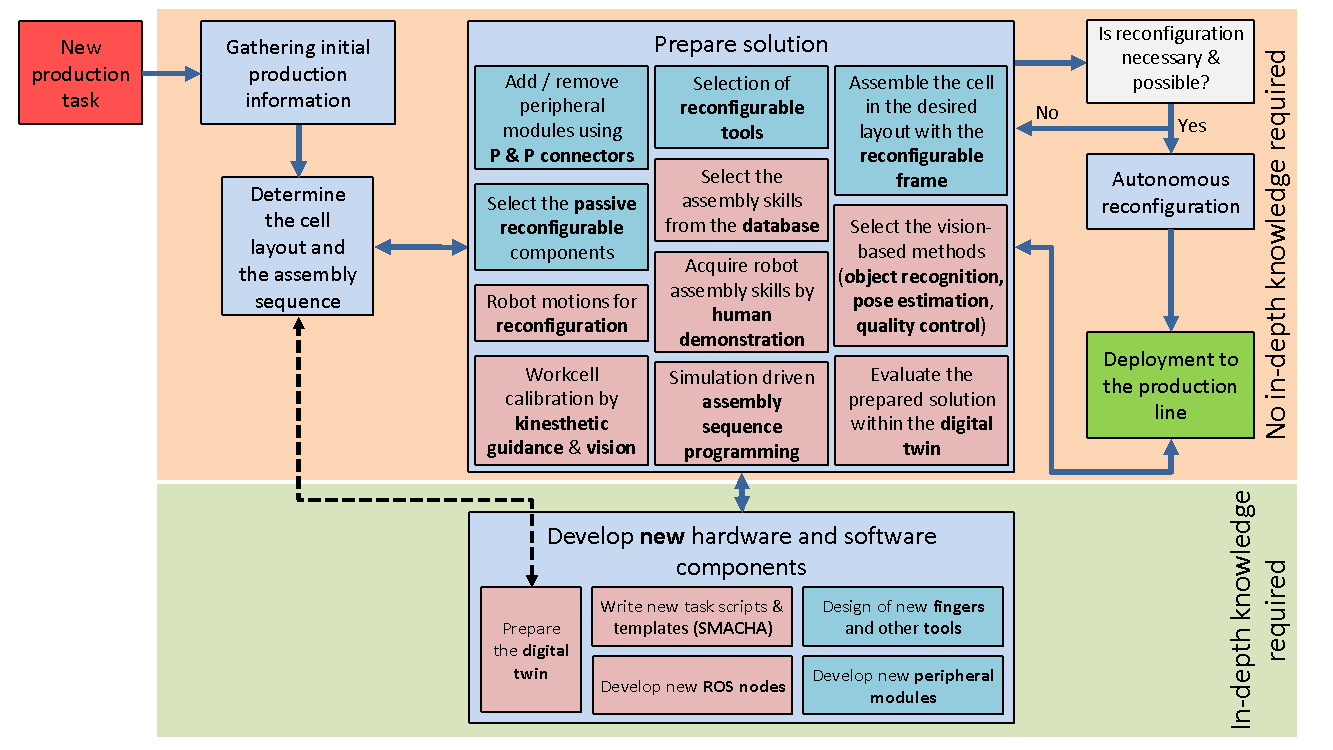
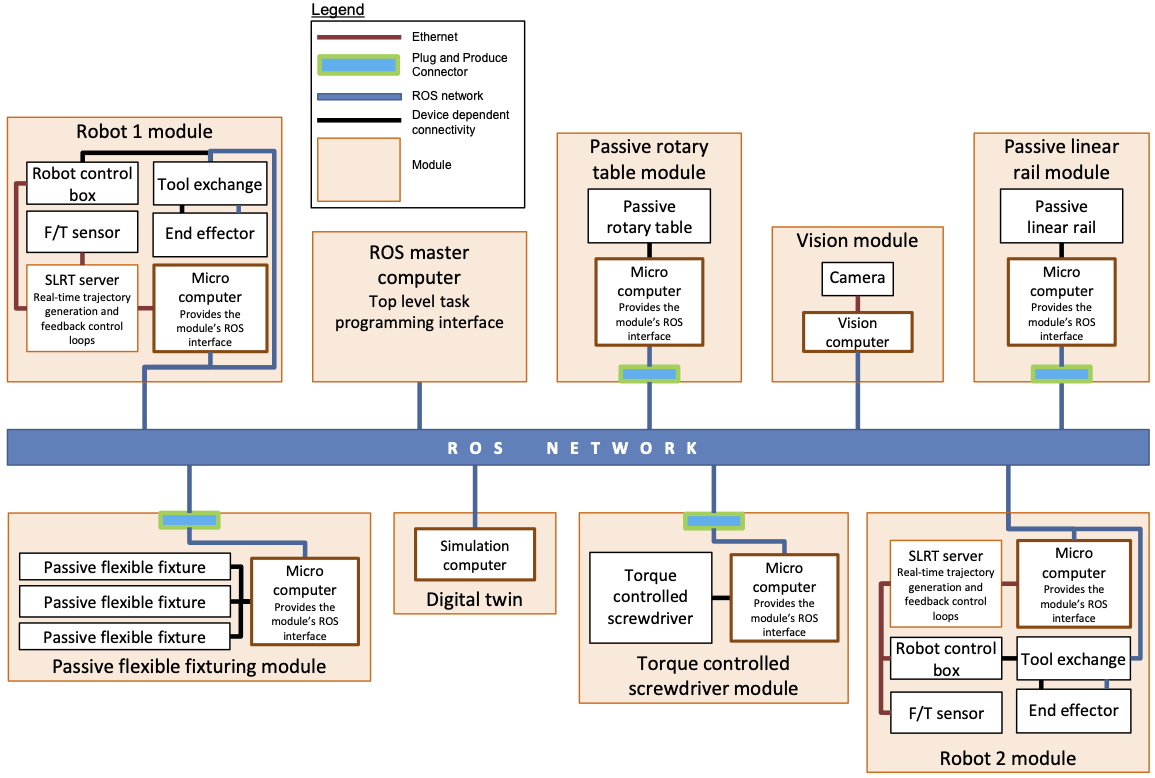
Video
The videos of example applications implemented in the reconfigurable robot workcell.
http://www.reconcell.eu/content/space/experiments.htmlOptimal locations and postures of reconfigurable fixtures
The module can be used to mount multiple workpieces onto a fixturing system constructed from two or more St...
LEARN MORE
ROS peripheral interface
The ROS periphery interface provided in this module is implemented on a micro-computer, e.g. Raspberry Pi. ...
LEARN MORE
Trainings
To learn more about the solution, click on the link below to access the training on the Moodle platform
Robot workcell reconfiguration