Virtualization of a Robot Cell with a Real Controller
Name of demonstration
Virtualization of a Robot Cell with a Real Controller
Main objective
The main objective for the demonstrator is that a virtual model can substitute physical hardware in the context of training, testing and simulating the various functions of a flexible robotic cell.
Short description
This module enables the control of simulated manufacturing hardware using a real controller. The simulated hardware is represented in a real-time 3D-environment which can be used for demonstrating actual system functionality, training employees, virtual commissioning and testing production operations for new parts. These activities can be done before the system even exists or after commissioning when they can be done without disturbing the ongoing production. This way changes can be made and tested without losing valuable production time. It also means that the layout design can be iterated multiple times before committing to the final one.
Owner of the demonstrator
Fastems Oy Ab
Responsible person
Teemu-Pekka Ahonen, Product Manager, Fastems Oy Ab
NACE
M71.1.2 - Engineering activities and related technical consultancy
Keywords
Manufacturing, Simulation, Training, Virtual commissioning, Robotics.
Potential users
SMEs in the metal cutting industry, Educational establishments wanting to teach about agile manufacturing in metal cutting industry
Benefits for the users
For SMEs: faster and safer ramp-up, reduced risk when making changes to production, safer and more efficient training for employees, reduced uncertainty when planning for the future
For education: cheap, compact and safe alternative to a physical robot cell, allows teachers to create interactive learning exercises to teach the fundamental concepts of agile manufacturing and robotics.
Innovation
The innovation in this module comes from the interface and communication method between the virtual model and the production control software. Previously this type of communication between the Fastems MMS and Visual Components was not possible.
Risks and limitations
This use case requires Windows 10, Visual Components 4.2 and Fastems specific hardware and software. Without these, the use of the described use case is not possible.
Technology readiness level
6 - Safety approved sensors and systems are commercially available
Sectors of application
Manufacturing sector: training and simulating the production off-line, Educational sector: teaching agile manufacturing without real robot system hardware.
Hardware / Software
Hardware:
Fastems cell controller
Workstation PC
Software:
Fastems MMS
Visual Components
Windows 10
Photos
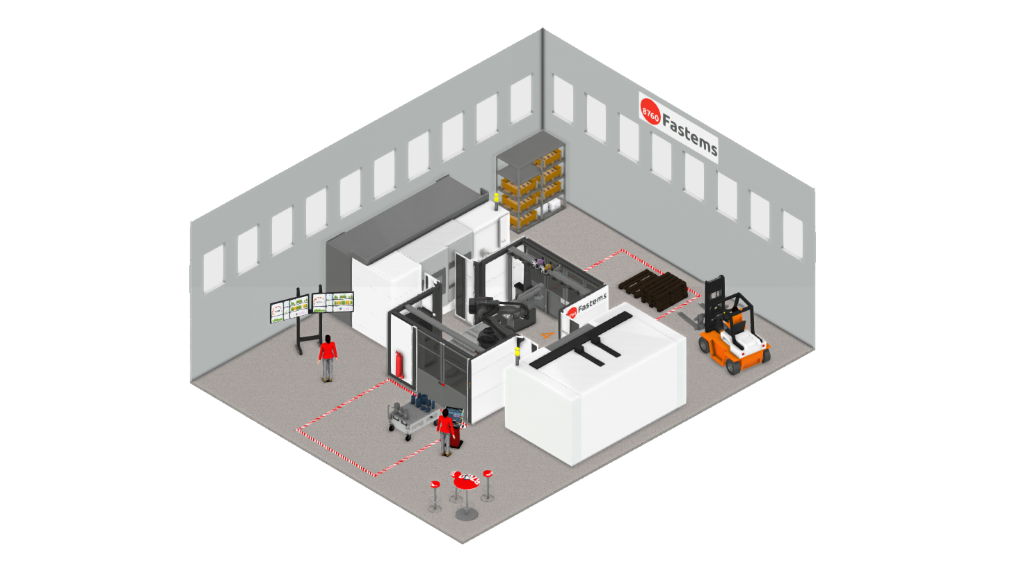
Trainings
To learn more about the solution, click on the link below to access the training on the Moodle platform
Virtualization of a robot cell with a real controller