SpinEye: AI & Cloud enabled vision system for agile teach-in of Assembly processes
Name of demonstration
SpinEye: AI & Cloud enabled vision system for agile teach-in of Assembly processes
Main objective
Every day, millions of screws and bolts are mounted in the European manufacturing industry by employees with handheld screwdrivers in everything from windows to cars & electronic products. The Trinity demonstrator shows how to automate high/Mix – low/volume productions involving screw assembly task, by introducing an easy-to use camera system – SpinEye which is fast to setup and program.
Short description
The data is being gathered through an integrated camera sensor – light source and being processed by a cloud-based scheme that enables remote monitoring, data annotation and data management. A robust specialized Artificial Intelligence (AI) scheme that has been extensively trained on the collected data and validated on various samples has been adopted. This module is responsible for detecting and accurately localizing screw holes on PCBs. Additionally, a teach-in user friendly interface, the so-called URcap, has been implemented for simplifying the hand-eye calibration process. Last but not least, a SpinEye low-cost box that controls the communication interfaces between all the components has been included.
This demonstration has received funding from the European Union’s Horizon 2020 research and innovation programme under grant agreement No 825196.
Owner of the demonstrator
Spin Robotics
Responsible person
Dr. Thomas Sølund, CTO Spin Robotics – email: ts@spin-Robotics.com
Lazaros Lazaridis, Machine Learning Engineer – email: lazaros.lazaridis@d-cube.eu
NACE
C26 - Manufacture of computer, electronic and optical products
Keywords
Robotics, Vision System, Machine Learning, human-robot collaboration, artificial intelligence, cobot assisted manufacturing, Collaborative Robotics, Industry 4.0, Machine Vision, robotic cell, automation, robotics and automation, AI.
Benefits for the users
Customers that will deploy SpinEye will benefit from faster changeover between tasks, while there is also no need for highly skilled workers to set up an assembly task. The quality rate will be increased, as the vision system will be able to detect slight mispositions of the fixture and adjust the cobot’s instructions.
Innovation
Manual screwdrivers are the norm is most assembly lines, as they are cheap and can handle the task of screwing. When using manual screwdrivers, employees are presented with strain to the body and the operation can be process to human errors due to fatigue. With robots, these factors are eliminated, and every screw will be inserted unison with precise torque. The SD35 innovates the market by making it possible for all enterprises to get access to a robotic assembly workforce, since it has a low implementation time/cost, and the fact that there is no need to change the setup of the production line.
Accidents can happen in a production line, but due to the safety features, such as the safety shield, of the SD35, those accidents will be eliminated.
The screw holes on PCBs have a diameter between 4-8 mm. The screws that will be mounted on those holes seem to have almost the same diameter as the holes. The cross on the middle of each screw is no more than 4mm. Therefore, from the AI/detection perspective, due to the screws and screw holes tiny nature, an extremely accurate machine learning object detection module has been developed.
Deep learning vision systems rely extensively on the quantity, quality and availability of input data for training. Thus, a specialized recording framework has been designed to capture and prepare the data. This framework has been implemented with respect to the assembly task, indenting to fit as closely as possible to scenarios that will be encountered during the assembly. The collected data from the recording framework is uploaded and stored in Trinity’s immersive framework cloud infrastructure enabling continuous analysis, data management and annotation procedures.
Risks and limitations
Risk/limitation: Before deploying and start using collaborative robots with the SD 35 screwdriving tool a risk assessment is always required. The risk assessment must be done in accordance with the ISO12100 standard that describes how to do a proper risk assessment. At Spin Robotics web page, you can find more information about how to do a risk assessment. Here you can download a risk assessment template in excel. Furthermore, you can download test reports from force impact tests the compute be applied during the risk assessment to prove that the tool is safe in according to the ISO/TS 15066. Always remember to update your risk assessment if you change the robot installation or the robot program. Remember also to take into consideration the physical installation or the environments that the robot I inserted into. For instance, are the robot installed close to a wall such that people can get trapped between the wall and the robot. Remember to always read the user manual before starting to implement a new screwdriving application with the SD 35 screwdriving tool.
Technology readiness level
6 - Safety approved sensors and systems are commercially available
Sectors of application
Small parts assembly.
Potential sectors of application
Automotive Industry, Electronic Industry, Wood Industry
Patents / Licenses / Copyrights
Hardware / Software
Hardware:
SD35 screwdriving tool
SPINBridge
Camera sensor and light source
Software:
Robot Apps for Universal Robots
Collaborative Robot
Screw presenter unit
Cloud infrastructure
AI – Deep learning screw detection module
Photos
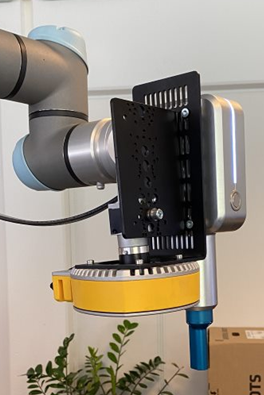
Video
Spin Eye promotional video
https://www.youtube.com/watch?v=9Gj5fgBX2BgExecutive video
https://dcubeeu-my.sharepoint.com/:v:/g/personal/dimitrios_katsikas_d-cube_eu/EcTRJ0HxChNNmd8-qSODD_0BClBxydAU-rzFyg1TmyYRqw?e=vLMiNgD3.2 - Demonstration of Hole detection model for the Screwdriver tool
https://dcubeeu-my.sharepoint.com/personal/dimitrios_katsikas_d-cube_eu/_layouts/15/stream.aspx?id=%2Fpersonal%2Fdimitrios%5Fkatsikas%5Fd%2Dcube%5Feu%2FDocuments%2FDcube%2FClients%2FTRINITY%2DSpinEye%2F9%2EOther%2FTrinity%5FAI%5FVision%5FSystem%5FVIDEO%2FTrinity%5FAI%5FVision%5FSystem%5F%5F%2Emp4&wdLOR=cD0A58994%2D6F2D%2D499D%2DBA8F%2D5725FCE27CA9&ct=1664482358273&or=Outlook-Body&cid=1138EADC-C51D-43B0-9523-2B9C31153639&ga=1No modules assigned
Trainings
To learn more about the solution, click on the link below to access the training on the Moodle platform
AI & Cloud enabled vision system for agile teach-in of assembly processes