ShipWeld
Name of demonstration
ShipWeld
Main objective
Development of a robotic welding system to automate ship newbuilding and repair operations, providing technicians with the tools to work on pieces of unknown geometry, while increasing their safety and productivity.
Short description
ShipWeld is a pre-programmed free and CAD-independent welding solution, based on a UR10e collaborative 6-DoF robotic arm equipped with a welding kit. Integrated sensors handle the 3D workspace reconstruction, ensuring obstacle-free motion planning, and seam tracking. A deep learning algorithm paired with explainable AI or a handheld 3D tracking system can be used to identify seams. In total, ShipWeld reduces manufacturing costs for shipbuilders, while preventing technician exposure to harmful welding radiation and toxic fumes.
This demonstration has received funding from the European Union’s Horizon 2020 research and innovation programme under grant agreement No 825196
Owner of the demonstrator
iKnowHow
Responsible person
Efthymios Pachos, Technical Manager, mpachos@iknowhow.com
NACE
C28.9 - Manufacture of other special-purpose machinery
Keywords
Robotics, Welding, AI.
Benefits for the users
The adoption of ShipWeld solution is anticipated to upsurge the user’s welding capacity, leading to increase in revenues (3-fold increase in the profit margin assuming that ShipWeld efficiency will be approx. triple that of manual welding). Moreover, the impact of an automated welding solution will improve the quality of the resulting welding seam through more precise welding procedure of the steel plates. Consistency in the welding result can be achieved with the adoption of an automated solution as the robot lacks the “fatigue” factor of the manual labour. The project management will be a much easier task using a single platform for real-time result visualization and data storage for later use and analysis through specific dashboards. The robotic welding system lowers the hazard level by preventing exposure of technicians to harmful welding radiation and toxic fumes. To this end, this opportunity will lead to the modernization of jobs in the company like welding technicians – the welding industry is facing a workforce crisis expected to lead to higher costs, reduced competitiveness, increased turnaround times, lost revenue and declining margins-, while generating new and advanced professions embracing Industry 4.0 technologies.
Innovation
ASSET 1: One of the most important features of ShipWeld is the 3D workspace reconstruction. The 3D scanner takes multiple scans and the produced point clouds are stitched to create an accurate model of the welding piece and its surroundings, in a process that takes a fraction of the time of the previous photogrammetry method. This model is used to achieve collision free trajectory planning. The system is completely CAD-independent – no other such system is available – therefore reducing usage complexity and dependence on third-party software platforms.
ASSET 2: Trying to keep the solution as generic and versatile as possible while retaining the human expertise in the loop, we decided to provide the end-user of the system with a means of control, a way to pinpoint seams that must be welded. For that purpose, we integrated an HTC Vive tracking device, which broadcasts pose data. This pose data is used to define a desired trajectory for a particular welding target. Our solution includes communication with the UI so that the user can signal recording of the intended trajectory. However, the greatest advantage lies in the integrated laser seam tracker; users do not have to be too accurate while defining the trajectory. The seam tracker will scan along the defined path and produce the correct welding trajectory.
ASSET 3: The shipbuilding industry tends to include welding of large parts. In such cases, defining seams by hand could be tiring and counterproductive. Here comes a deep learning, in-house developed algorithm, that identifies seams along welding parts. In addition, Umnai provided technology capable of converting the black-box algorithm model into a fully-explainable and actionable white-box model. In this white-box model, or eXplainable Neural Net (XNN), the function and purpose of every node and connection within the model is known and understandable allowing for improved model interpretation, design and optimisation. Furthermore, XNNs provide explanations for predictions in real time which means that we are able to act on predictions meaningfully and with purpose, leading us to achieve the desired accuracy in results.
Risks and limitations
The welding interface is not yet integrated in the ShipWeld pipeline. The user needs to preselect the welding parameters before the system scans and welds the workpiece. Multiple paths and weaving are under development.
Technology readiness level
7 - System model in operational environment
Sectors of application
Shipbuilding, Welding .
Patents / Licenses / Copyrights
Hardware / Software
Hardware:
UR10e manipulator coupled with welding machine
HTC Vive
Photoneo PhoXi Scanner M
EVT Saturn laser Scanner
Software:
ROS
Bespoke ShipWeld software
Photos
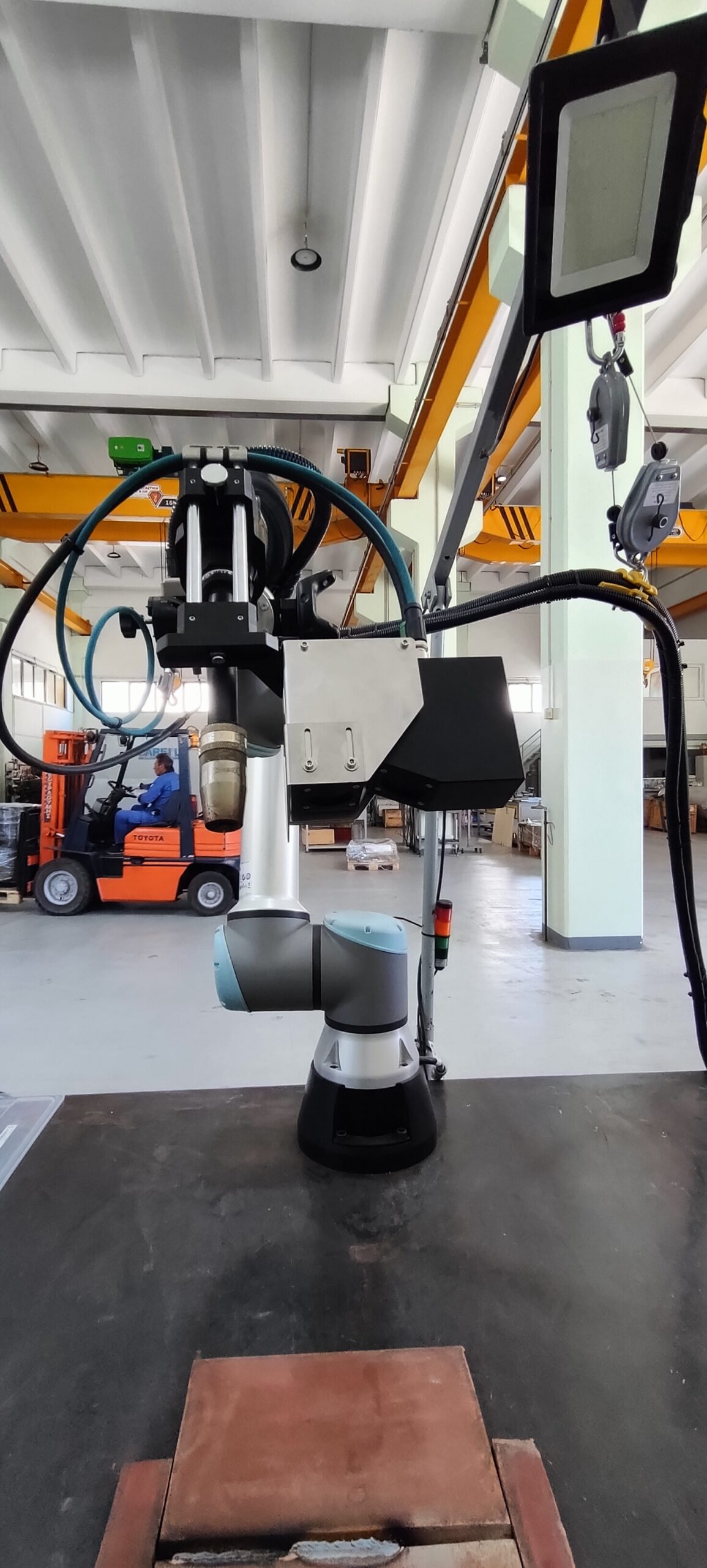
Video
ShipWeld video showcasing workpiece scanning, user interaction with workpiece using WeldWand, user interface, seam tracking, welding
https://youtu.be/BDhBIFcFCYUNo modules assigned
Trainings
To learn more about the solution, click on the link below to access the training on the Moodle platform
Mobile, flexible robotic welding system to reshape the European shipbuilding industry