SALSA2d: Separation of Additive Layer Support by Automation via 2-way Digital Twin
Name of demonstration
SALSA2d: Separation of Additive Layer Support by Automation via 2-way Digital Twin
Main objective
This project aims to automate the support material removal post-processing step of additive manufactured components (specifically metal AM) by leveraging computer vision, robotic proprioception and simulation software. We seek to demonstrate the use of custom teaching software to effortlessly plan complex trajectories.
Short description
The following demonstration shows robotic support removal on an additive manufactured part using force controlled percussive tools. Three-dimensional computer vision is used to compensate for part variability and the process is simulated and visualised on Rviz. This demonstration will be valuable to industries looking to advance towards fully digital post-processing of near-net-shape manufactured components.
This demonstration has received funding from the European Union’s Horizon 2020 research and innovation programme under grant agreement No 825196.
Owner of the demonstrator
Additive Automations
Responsible person
Chief Technology Officer, Dr David Alatorre, alatorre@additiveautomations.com
NACE
C28 - Manufacture of machinery and equipment n.e.c.
Keywords
Robotics, Machine Vision, automation, Additive manufacturing, near-net-shape manufacturing, machine perception.
Benefits for the users
Design flexibility: The ability to quickly and intuitively modify machine code from a user interface allows operators to iterate designs quickly or work efficiently with always-custom components such as medical devices. Ease of operation: The elimination of skilled work and the simplification of robot programming by use of a simulated environment greatly decreases the time required to train production line technicians to use the robotic post-processing system. Volume production: Manual post processing is currently a bottleneck during production. Eliminating this barrier would allow production of additive manufactured components to scale with demand. This value proposition applies to customers in the industrial, energy, aerospace and automotive sectors, and any business currently unable to leverage AM at scale. Repeatability: The guaranteed consistency that comes with digital manufacturing leads to a 90% reduction of defects. Such a reduction in defects and scrap rates is a clear benefit for all of the potential users listed above. Cost saving: The combination of improved efficiency, decreased training time, reduced defect rate and 24-hour uptime is estimated to result in a 77% cost reduction. This includes depreciation of the CapEx cost of a robotic post-processing cell.
Innovation
As with any new venture in automation, our target is to outperform a manual process and repeatability is the key dimension to differentiate our technology. Our approach relies on proprioception, computer vision and intelligent software to give an industrial robotic arm the necessary dexterity to perform delicate tasks.
A computer vision algorithm developed in partnership with NRC Canada is used to compensate for part variability – a common aspect of additive manufactured parts – by aligning depth measurement data to the expected component 3D geometry.
A proprietary force control algorithm designed specifically for machining with low-stiffness robots serves to protect the system from surface-level imperfections often found in additive manufactured components, and helps achieve high accuracy results with a low-cost and light-weight robot arm.
Cutting edge software tools powered by ROS (Robot Operating System) incorporate machine perception with an intuitive user interface to guide the robot arm along complex and dynamic trajectories.
Risks and limitations
Compatibility: Our demonstrator must be used with ROS-compatible robot controllers capable of receiving pose streaming commands for instantaneous trajectory corrections by the force controller. One such controller is the Yaskawa YRC100micro. Our demonstrator must be used with ROS-compatible peripheral and tool controllers. Capability: The force control algorithm requires a 6-axis force transducer capable of streaming wrench data at at least 1000Hz. The machine vision algorithm requires a measurement system (stereo and/or structured light) capable of producing point cloud captures with better than 50 micron accuracy, such as a LMI 3D Gocator 3210. Application: The proposed system is intended to be used on near-net-shape parts and is not intended to perform bulk material removal or broader subtractive manufacture.
Technology readiness level
7 - System model in operational environment
Sectors of application
AEROSPACE: Manufacturers of aeroengines, aircraft components or satellite/spacecraft components requiring complex and light weight parts may use this demonstrator to eliminate the bottleneck to volume production of AM components and to simplify the certification process for new AM parts., ENERGY: Manufacturers of energy generation turbomachinery may use this demonstrator to increase production of advanced fuel injectors, heat exchangers and other complex parts. Remote plants may use AM with post-production robot cells to eliminate the need for spare parts and reduce repair downtime., AUTOMOTIVE: Manufacturers of sport and luxury vehicles requiring lightweighting of components and volume production of customised interior components may use automated post-processing to cut costs., MEDICAL: Companies producing bio-compatible metal implants, high-temperature custom moulds for dentures and complex dental aligners may use these cells to guarantee part compliance and achieve fully digital manufacture., DEFENCE: Organisations or companies overseeing supply logistics and asset maintenance for military equipment may use in-situ additive manufacturing and robot post-processing to make components and tools, eliminating the need to stock spare parts or send equipment away for overhaul..
Potential sectors of application
Consumer electronics: As luxury products become more customised, the use of additive manufacturing with automated post-processing will play a part in achieving economies of scale in this and other similar sectors. Marine: Similar to the energy sector, marine manufacturers may use this demonstrator to increase production of complex power generation components using corrosion resistant materials. Construction: As additive manufactured building gains traction, a scaled up version of this demonstrator may be used to automate the finishing steps of printed structures.
Patents / Licenses / Copyrights
Patent pending: Finishing system for near net shape parts (GB2114701.2)
Hardware / Software
Hardware:
ROBOT ARM (hardware): A series manipulator with at least six axes of motion is required to orient and apply tools on additive manufactured parts.
ROBOT CONTROLLER (hardware): A ROS-compatible robot controller is required to receive instructions from and return feedback to the perception, planning and control nodes running on a control PC.
POSITIONER (hardware): A rotary stage capable of turning the additive manufactured parts through 360 degrees may be required to augment the workspace of the robot arm.
3D VISION SYSTEM (hardware): A 3D measurement system (stereoscopic or structured light) may be required to provide feedback for the motion control and quality control nodes running on a control PC.
WRIST FORCE SENSOR (hardware): A six-axis force/torque sensor is required to provide tactile feedback to the force control nodes running on a control PC.
LINUX/WINDOWS PC (hardware and software): A computer running a Linux operating system such as Ubuntu or a Microsoft operating system such as Windows 10 is required to run the software nodes for perception, planning, control, user input, simulation, etc.
Software:
ADDITIVE AUTOMATIONS APPLICATION (software): A copy of Additive Automations’ support removal control application is required to establish communication, send commands and receive feedback from the hardware elements.
Photos
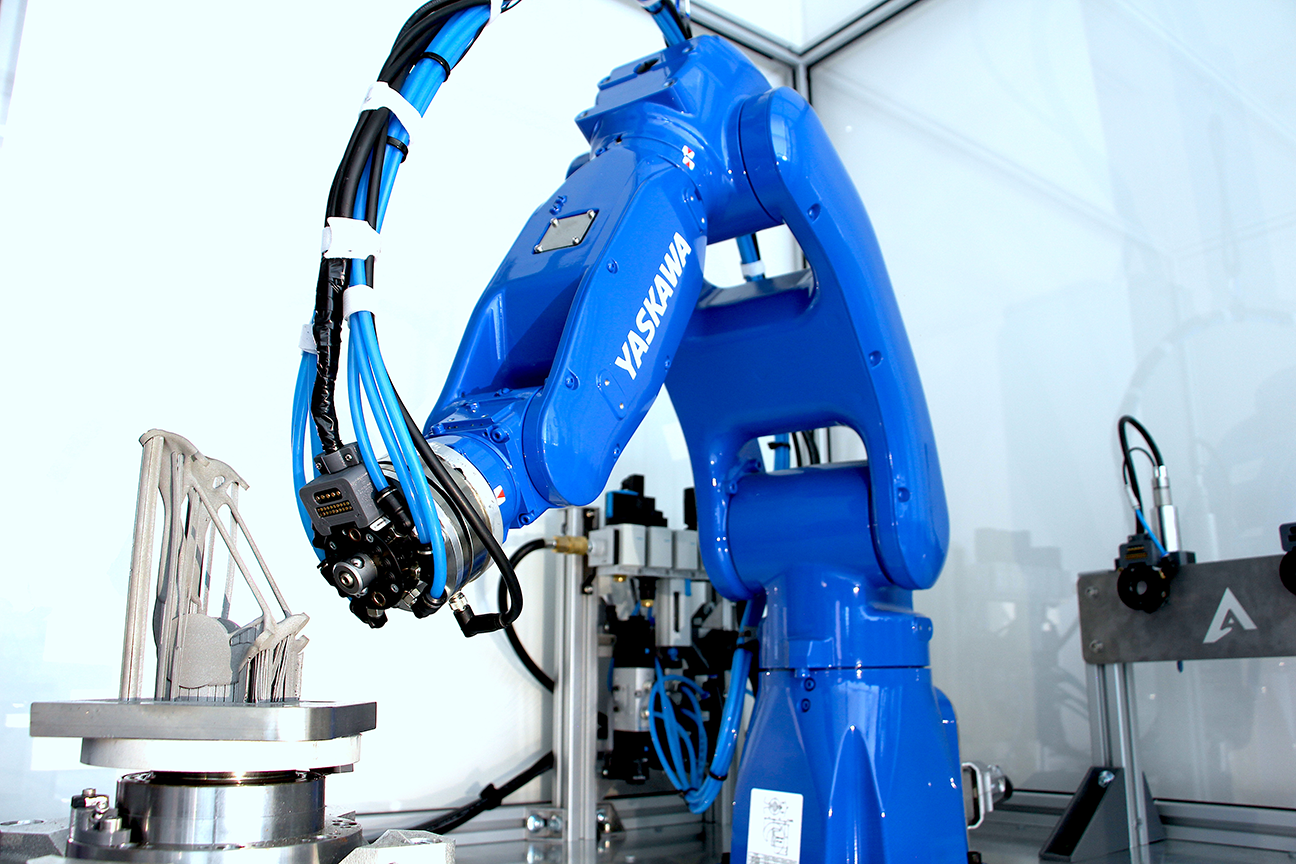
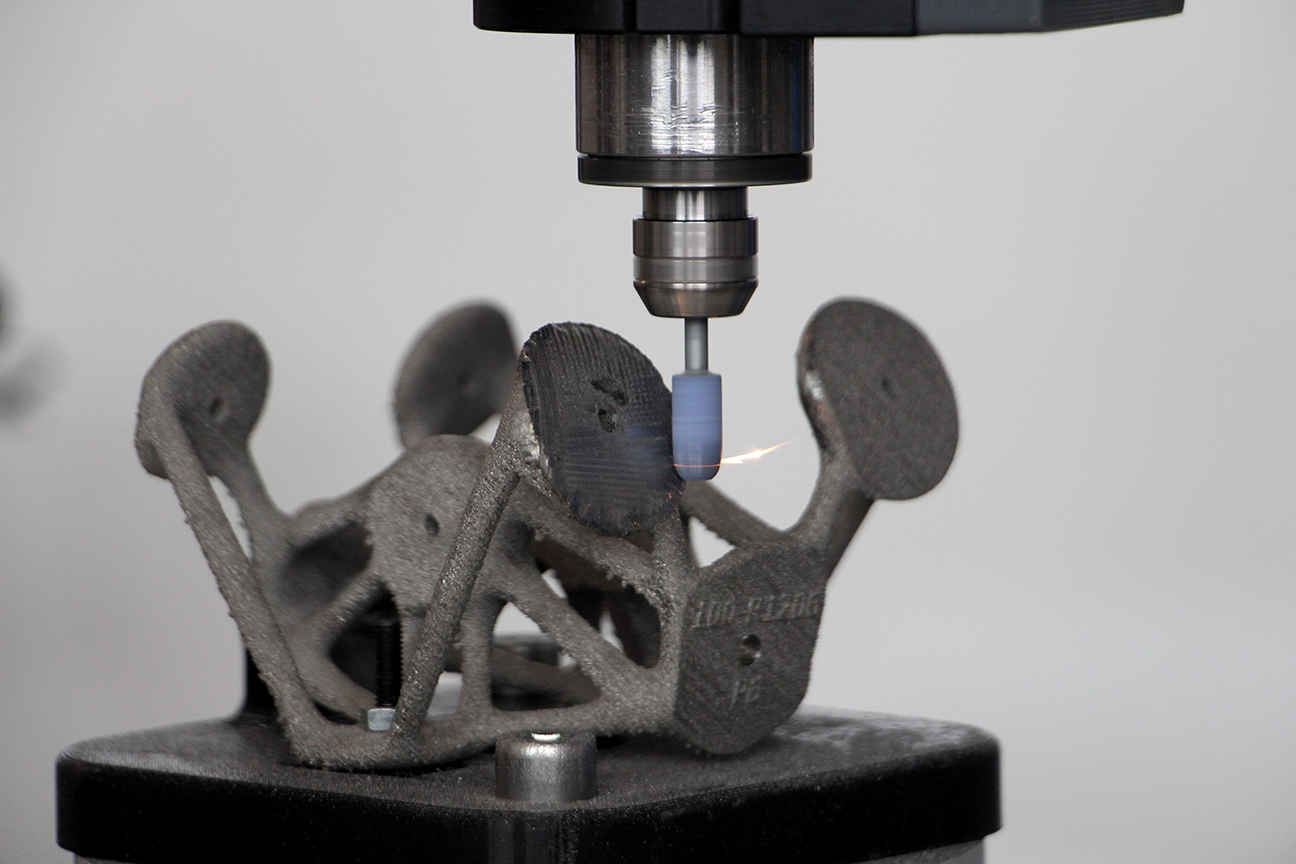
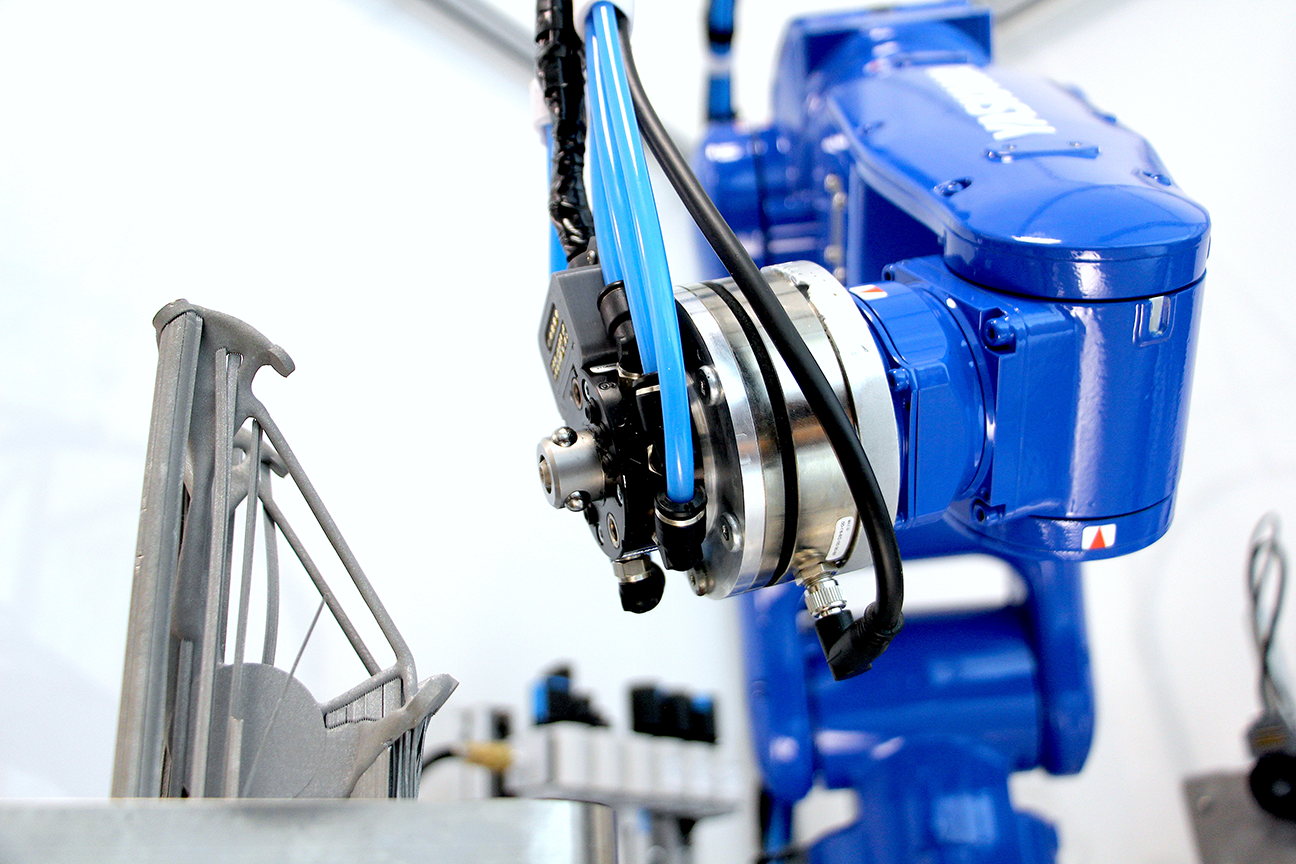
Trainings
To learn more about the solution, click on the link below to access the training on the Moodle platform
Separation of Additive-Layer Supports by Automation via 2-way Digital Twin