Robotic lamination of composite parts (CANNIER)
Name of demonstration
Robotic lamination of composite parts (CANNIER)
Main objective
The main objective is to develop a flexible robotised moulding cell, capable of automatically laminating carbon fibre reinforcements that have been pre-impregnated (prepreg) with activated resin for variable product specifications.
The aim is to make the manufacturing process more agile, overcoming the bottlenecks of manual moulding (hand lay-up), to increase production performances and repeatability, with a reduced final cost of the composite parts. Develop a flexible robotic system, capable to adapt to different specific geometries, without the need for complex and time-consuming reprogramming of the robot.
Short description
CANNIER brings together two key technologies:
1- Lamination CAD designer – a software tool to generate the lamination trajectories, extracting all required parameters from the CAD of the parts to be manufactured and of the robotic tools.
2- Mechanical design of the end-effectors for the ply lamination and the tool changer. These tools dynamically adapt the pressure applied on the prepreg.
This demonstration has received funding from the European Union’s Horizon 2020 research and innovation programme under grant agreement No 825196.
Owner of the demonstrator
Roboticssa
Responsible person
Title: Roboticsaa CEO
Name: Mr. Ignacio Secades
Contact: ignacio.secades@roboticssa.es
NACE
C28.9.9 - Manufacture of other special-purpose machinery n.e.c.
Keywords
Collaborative Robotics, carbon fiber, prepreg, composites, CFRP, lamination of CFRP components.
Benefits for the users
Thanks to CANNIER, the lamination process of CFRP components will be more agile, leading to an automated environment that ensures improved quality and repeatability of the parts manufactured.
Moreover, CANNIER contributes to the achievement of significant economic and environmental benefits:
• Increase productivity: maximising the exploitation of moulds, which are very expensive assets;
• Time reduction for the moulding time of carbon fibre prepregs by 40%, compared to manual lamination;
• Reduction of manufacturing cost by 25%, considering robot cost-effectiveness and reduced defected parts;
• Reduction of waste material due to non-compliant products between 2-3%, caused by operator mistakes;
• CO2 emissions are saved thanks to the reduction of waste and faulty components in the production process. A reduction of about 0.9 tons of CO2 is estimated, referred to as a batch of 1000 parts;
Innovation
Small manufacturers of CFRP components widely use manual labour in their production process. Options for
automation are available only to manufacture large batches or very specific parts. CANNIER introduces technologies that are more suitable than the “hand lay-up” process.
The mechanical design of a custom robot end-effectors presents a set of blunt tools for lamination of different geometries and geometrical features, and a dedicated tool changer to enable reconfiguration based on the specific process needs. The end-effector designs have achieved a balance between the variability of tools, to overcome the constraints induced by multiple shapes, geometries, and sizes of the parts.
The lamination CAM software makes the process more agile, generating the trajectories performed by the robot on the base of the parts 3D CAD models and the selected tools; the CAM tool will allow expert operators to adjust the generated trajectories based on their experience and to select the best-suited tool for each step of the lamination with an intuitive user interface (HMI).
The HMI also allows a simple reprogramming of the robot for new parts, making the process more agile and significantly reducing the time needed to reconfigure the system.
Risks and limitations
CANNIER could present limitations in two aspects that nonetheless can be addressed for a particular customer: 1- Work with molds of big dimensions. The robotic cell could be scaled up and the collaborative robot changed for a larger one. 2- Work with special geometries. For this case, new tools will be designed.
Technology readiness level
9 - System/model proven and ready for full commercial deployment
Sectors of application
The sector of application is small manufacturers of prepreg carbon-fibre-reinforced polymers (CFRP) parts. These companies have the strong need to improve the agility of their manufacturing process, increasing productivity, quality and repeatability of products, and to reduce manufacturing costs. Small manufacturer of CFRP components widely use manual labour in their production process. Options for automation are available only to manufacture large batches or very specific parts. Furthermore, with the increase of components produced, other manufacturing technologies are more suitable than the “hand lay-up” process. The main industrial challenges related to the automation of the lamination process concern the achievement of the high degree of flexibility of the robotic cell (with reduced reprogramming time) and the quality improvement for the broad range of products that can be manufactured. .
Potential sectors of application
Large manufacturer of CFRP components can also potentially benefit from CANNIER. They add to the benefits that CANNIER brings to small manufacturers of prepreg carbon-fibre-reinforced polymers the potential for bigger margins due to economies of scale. The production of bigger batches could enhance the productivity of CANNIER and incentivize the development of more lamination tools for our solution.
Patents / Licenses / Copyrights
Hardware / Software
Hardware:
Collaborative 6 DOF arm
Lamination tools
Software:
Lamination CAD designer: software for generating the lamination trajectories. A program executing these trajectories with the selected laminaiton tools is sent to the robot arm.
Photos

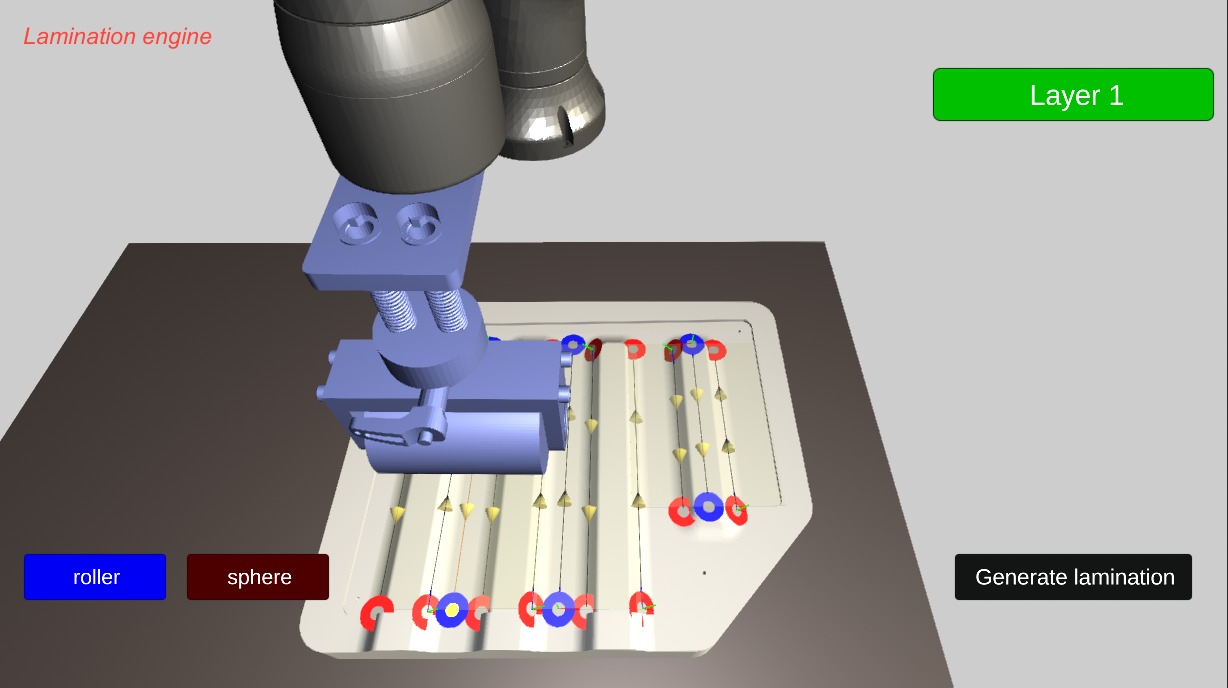
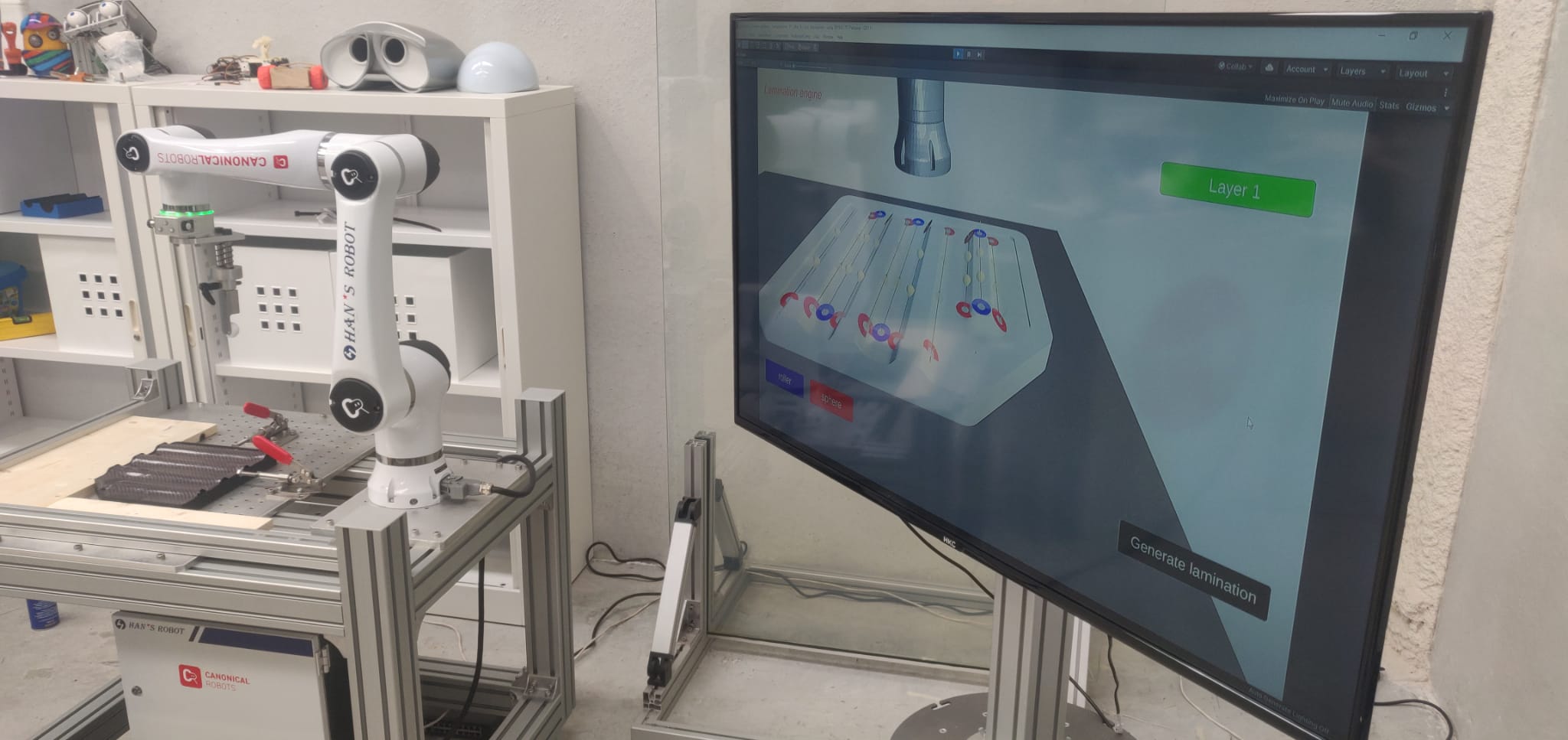
Video
Robotic lamination of composite parts.
https://Youtu.be/NJyB7gr302cRobotic lamination of composite parts. Executive video.
https://Youtu.be/jQ9pdkGc_rQNo modules assigned
Trainings
To learn more about the solution, click on the link below to access the training on the Moodle platform
Robotic lamination of composite parts