Integrating digital context to the digital twin with AR/VR of the robotized production
Name of demonstration
Integrating digital context to the digital twin with AR/VR of the robotized production
Main objective
To showcase the use of digital context data in manufacturing. Integration of robot trajectory data into product design provides an agile way for automating manufacturing processes and speeds up the design-production timeline. Complete VR/AR environments can be built and used for flexible monitoring, support, training, safety and maintenance.
Short description
The use case demonstrates the possibilities for utilizing digital context data into production of manufacturing companies, which provides an agile way for automating manufacturing processes. The use case involves utilizing BIM, VR/AR technology and a digital twin of a robotic production cell. These methods can be used for flexible monitoring, operational support, training, safety and maintenance purposes of the production cell.
Owner of the demonstrator
Centria University of Applied Sciences
Responsible person
Senior Research Scientist Sakari Pieskä
sakari.pieska@centria.fi Tel.: +358 44 449 2564
NACE
C28.2 - Manufacture of other general-purpose machinery
Keywords
Virtual reality, Augmented reality, Digital twin, Automation, Digital design.
Potential users
Robot and automation integrators, Manufacturing companies, SMEs providing or utilizing augmented reality interaction
Benefits for the users
Design-to-production time reduction: shortening of product’s design-production time span in manufacturing by introducing advanced product design e.g. robot trajectories to digital models already at the design phase.
Operational information: digital twins provide information of the real world enabling advanced monitoring if the system is performed as designed. Additionally, digital twins allow information flow from the real world to the digital allowing to update digital models if necessary. In addition, AR allows flexible and agile maintenance.
Advanced training: operational and safety training can be performed safely in virtual environment with the presence of instructor. Challenging conditions such as fire, toxic gas, dust, smoke etc. can be safely simulated in virtual environment.
Advanced risk assessment: Using virtual models of fully functional robot cells, risk assessment can be performed safely including visual inspection of robot cells, precise distance measurement, and testing of safety equipment.
Innovation
The use case innovates the existing product design capabilities along with robot maintenance and operational training measures by utilizing digital twins and AVR models in the production and robot integration. The use of digital twin and virtual environment of robot cells provides a safe, easily adaptable environment for the precautionary risk assessment in the integration phase, or for the operational and safety training on the robot cell tending. For example, as a result of a virtual environment training, newly trained operators will:
– learn to operate machinery in a safe and efficient way,
– learn to react proactively and safely to tasks that require a human interaction, and
– receive concrete information on safety measures in the robot cell (safety devices, first aid kits etc.).
The use case also innovates the product design during the design phase of new workpieces. A product design engineer can include the robot trajectory data into the product data at an early product design, and this information can be used by production engineers for robot programming at the production starting phase. This reduces the design-production time and leads to less faulty workpieces at the starting phase, which both lead to more agile robotized production and increased productivity.
Risks and limitations
Lack of incompatible specific software needed in integration may be a limitation.
Technology readiness level
6 - Safety approved sensors and systems are commercially available
Sectors of application
AUTOMOTIVE INDUSTRY, CONSTRUCTION, ELECTRICAL AND ELECTRONIC ENGINEERING INDUSTRIES, FOOD AND DRINK INDUSTRY, HEALTHCARE INDUSTRIES, MARITIME INDUSTRIES, MECHANICAL ENGINEERING, SPACE INSUTRY.
Potential sectors of application
EDUCATION
Patents / Licenses / Copyrights
Digital Design Content Based Robot Trajectory Generation: Usage of module is free excluding SolidWorks, Unity, Vuforia and RoboDK which are commercial software and licensing has to be negotiated with them.
Blender is released under GPL.
Other software developed at Centria is released under MIT license.
Hardware / Software
Hardware:
Virtual reality headset: e.g. HTC Vive includes base stations to track user movements in a real environment and hand-held controllers for user interaction. These devices together with a VR platform enable a full VR experience.
Indoor positioning system: e.g. Quuppa Intelligent Locating System. This can be utilized to improve the safety of robotized environments by tracking either mobile robots or people in the environment.
Software:
Simulation and programming framework: e.g. RoboDK. A developmental platform for industrial robot offline programming and simulation. RoboDK includes support for an online connection of robot systems and connection to SteamVR platform.
VR software: e.g. SteamVR. publishing and distributing platform for VR software providing a connection between VR software and hardware.
SolidWorks: a solid modelling computer-aided design and computer-aided engineering utilized to include information needed for robotized production to digital design content.
Unity: game engine for building AVR-experiences on multiple platforms.
Vuforia: augmented reality software development kit. Key features of Vuforia include real-time 3D object detection and planar surface design tools, which in combination with AR equipment may be used in AR environment for design and manufacturing purposes.
Blender: free and open-source 3D computer graphics software utilized for building and modifying 3D-model files for Unity.
Trainings
Online training material is available through the TRINITY training platform that contains separate training material for use cases and modules.
Photos
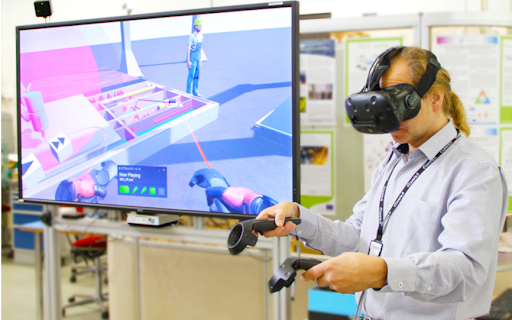
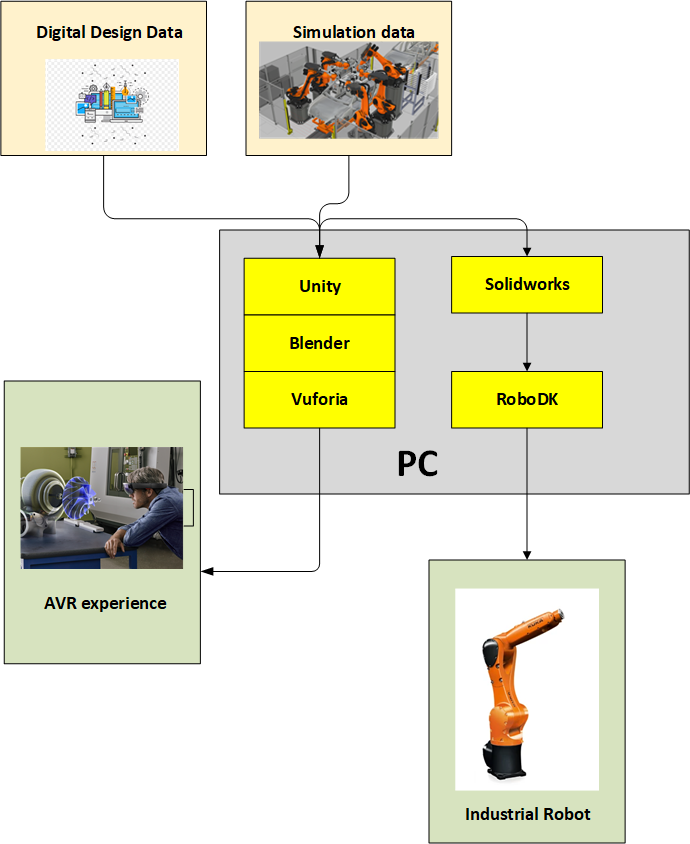
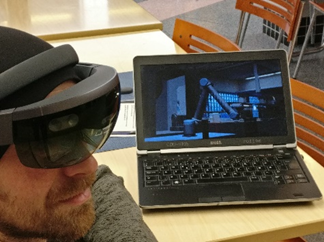

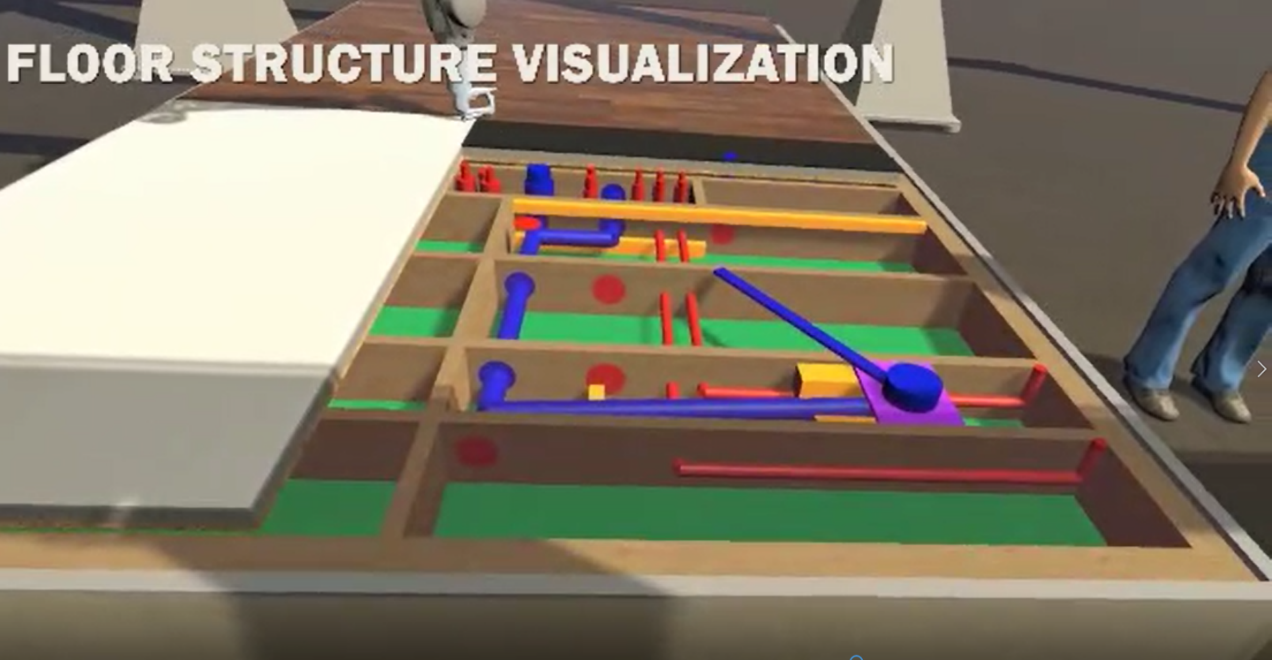
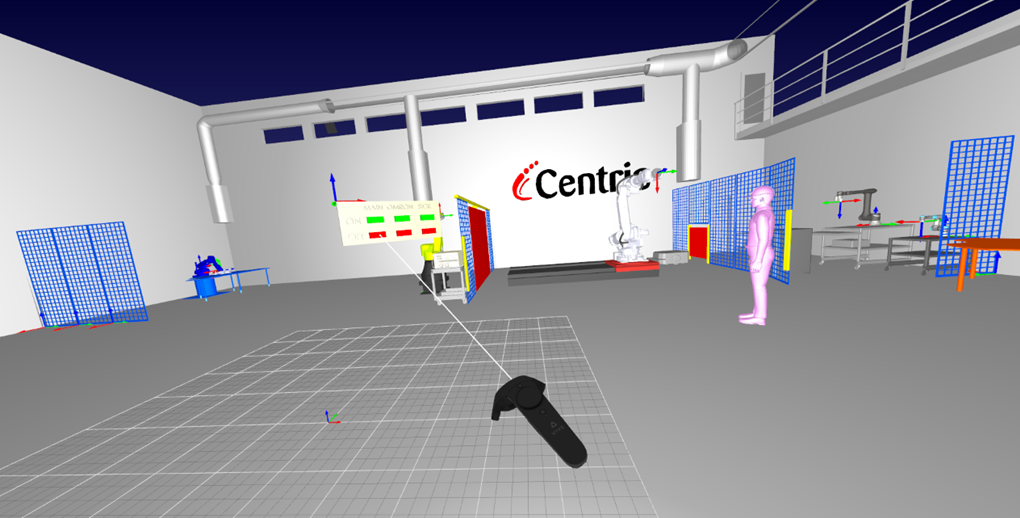
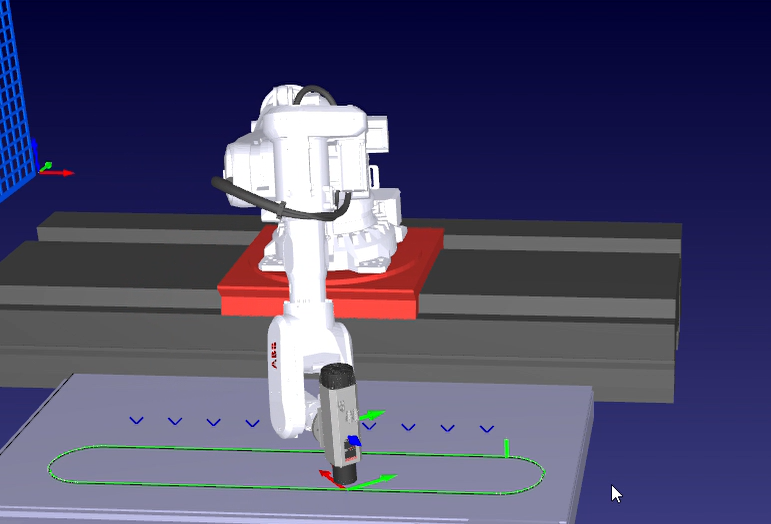
Trainings
To learn more about the solution, click on the link below to access the training on the Moodle platform
Integrating digital context (e.g. BIM) to the digital twin with AR/VR of the robotized production