ICON – agIle eleCtric mOtor maNufacturing
Name of demonstration
ICON - agIle eleCtric mOtor maNufacturing
Main objective
The main objective of the demonstrator is to make the manufacturing process of electric motors more agile, by deploying three TRINITY-originated modules in a production line. This leads to: increased HRC level and productivity in the coils winding step, waste material saving, economic and social benefits.
Short description
This demonstrator introduces three TRINITY-originated modules into an existing robotic cell for coils winding. Thanks to them, the cell is enhanced with new collaborative skills. The “Safe Human Detection in a Collaborative Work Cell” module allows the operator to work safely alongside the robot, creating dynamic and adaptive safety areas. Thanks to the “Projection-based Interaction Interface for HRC” module it is possible to control the robot using an innovative interface projected on the working-table. The “Object Classification” module allows to automatically recognize different stator designs and load the related parameter set to generate the robot trajectory to wind the coils.
This demonstration has received funding from the European Union’s Horizon 2020 research and innovation programme under grant agreement No 825196.
Owner of the demonstrator
Stam S.r.l.
Responsible person
STAM Business Area Manager – Robotics and Mechatronics, Stefano Ellero
ICPE Servomotors Department Manager, Paul Minciunescu
Keywords
Robotics, human-robot collaboration, industrial robotics, safety, object classification.
Benefits for the users
Thanks to this demonstrator, the manufacturing process of electric motors is:
– More agile: reduced time for cell reconfiguration.
– More productive: less time wasted in cell reprogramming and task parallelization.
– More automated and with an increased level of HRC.
In particular, it is possible to achieve:
– Time reduction: for the HRC-based process, which allows the operator performing preparatory and finishing tasks on a stator while the robot is winding another stator.
– Increased operators’ satisfaction and trust: following the deployment of HRC tasks.
– Material cost saving: thanks to the HRC-based winding process instead of semi-automatic process.
– CO2 emissions saving: thanks to material saving.
Innovation
The low flexibility of automated winding machines and conventional robotic systems, i.e. the time and costs required to switch from one design to another, coupled to their high cost, force small manufacturers to employ human operators in this task, who are obviously much more flexible, but more expensive (because of labour cost and equipment). Moreover, if the robotic cell responsible for coils winding is not able to guarantee the safety of the operator, no collaboration can be achieved between the human and the robot and therefore, while the robot is active, the operator has to stay behind a safety fence. Thanks to the three TRINITY-originated modules deployed in this use-case demonstrator, the implementation of collaborative tasks is possible, achieving multiple benefits. It is possible for the operator to work safely alongside the robot, significantly reducing idle times and speeding up the process.
Risks and limitations
ROS compatibility: this use-case demonstrator is based on ROS. The system has been tested with ROS supported hardware, such as Intel RealSense and Microsoft Kinect RGB-D cameras, the compatibility with different hardware depends on the ROS driver availability of the intended hardware. Knowledge of ROS: developers need to be familiar with ROS and its communication protocols. Cybersecurity aspects: since for the object classification task a dataset of stator pictures has to be acquired, further consideration on cybersecurity should be done to protect data from intellectual property theft, such as theft of proprietary design or pictures.
Technology readiness level
6 - Safety approved sensors and systems are commercially available
Sectors of application
Manufacturing.
Potential sectors of application
Manufacturing: various sizes companies dealing with manufacturing systems that aim to increase automation in their processes or companies that already have robotic cells in their production line and want to introduce collaboration between the operator and the robot. Thanks to this technology, companies would be able to improve the safety level of the robotic environment and make the robot perform the most repetitive and heavy tasks.
Patents / Licenses / Copyrights
Hardware / Software
Hardware:
KUKA KR6 sixx collaborative robotic arm.
KRC4 compact robot controller.
Rotary table combined with a self-centering chuck.
Industrial PLC: for handling the communication between the various components.
Control panel: to manage the basic signals for activation, start-up and emergency stop of the robotic cell.
End-effector: for winding the wire.
Linux industrial PC running ROS: for the software computations.
Lidar sensor: for detecting the proximity of the operator to the robot (such as KEYENCE SZ-01S).
Projector: for projecting the user interface components and the safety contour on the workspace (such as SHARP XR-32s).
RGB-D camera: for monitoring the depth values of the workspace and thus detecting the interaction of the operator with the interface (such as Microsoft Kinect v2).
RGB-D camera: for stator classification (such as INTEL RealSense D415).
Software:
TRINITY module: Safe Human Detection in a Collaborative Work Cell
TRINITY module: Projection-based Interaction Interface for HRC
TRINITY module: Object Classification
ROS
OpenCV
Photos
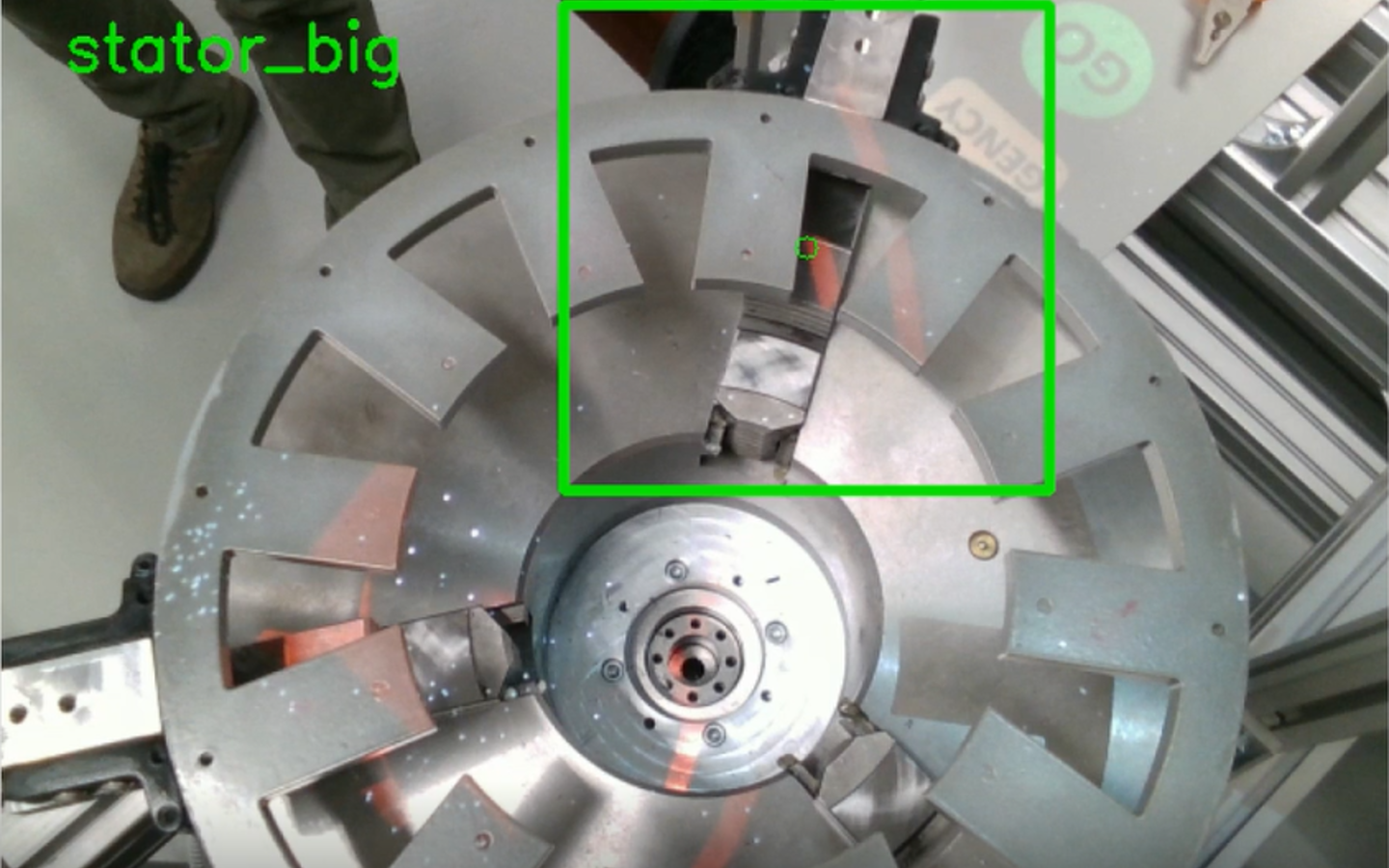
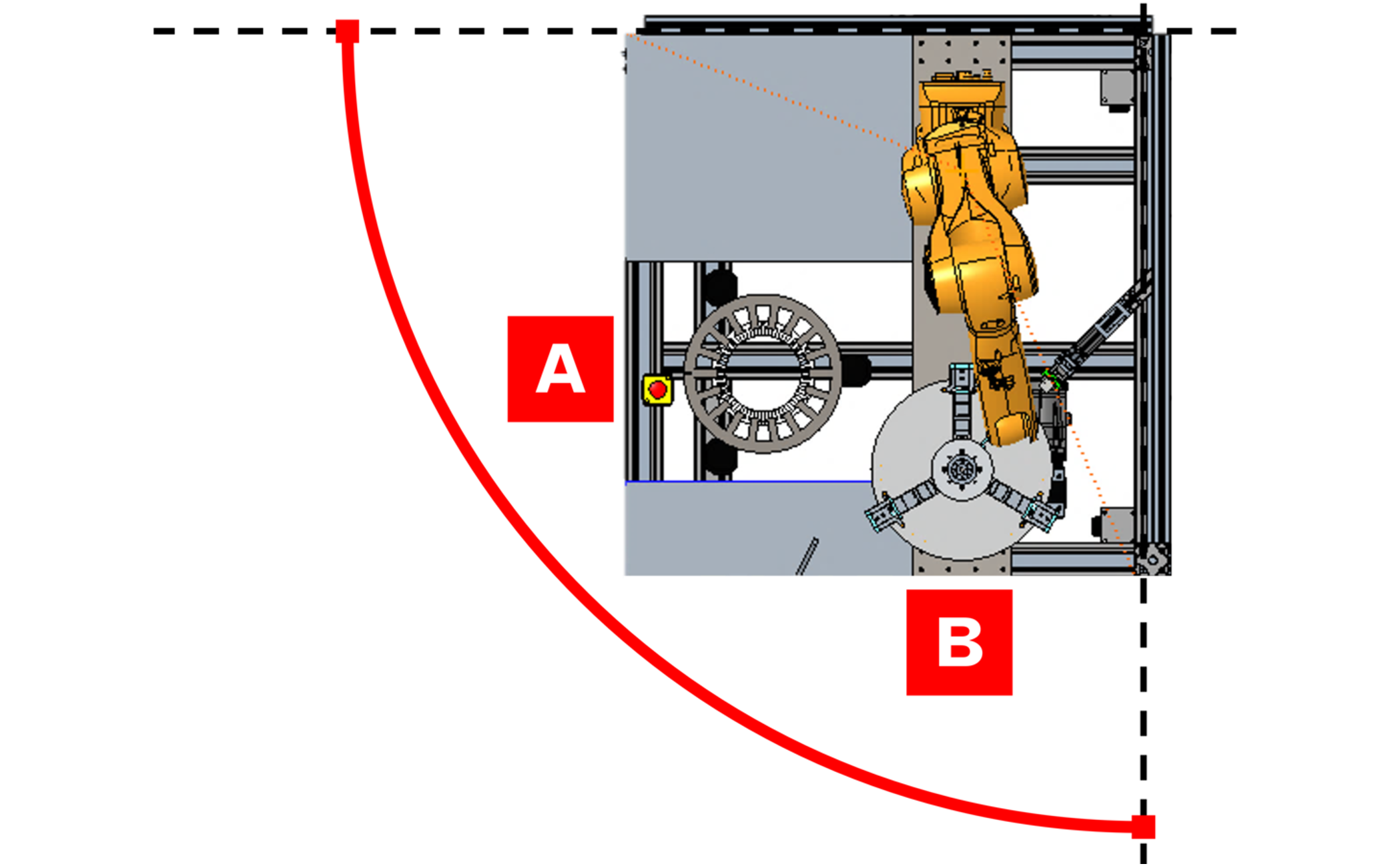
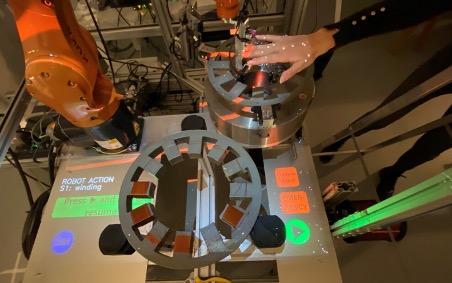
Object Classification
A deep convolutional neural network (CNN) is used to classify and sort objects. This is a robust and fast i...
LEARN MORE
Projection-based Interaction Interface for HRC
Interface Generation: The module projects interface that the user can interact with by placing a ha...
LEARN MORE
Safe Human Detection in a Collaborative Work Cell
Creating safety areas: flexible and adaptive creation of dynamic safety areas is based on information from ...
LEARN MORE
Trainings
To learn more about the solution, click on the link below to access the training on the Moodle platform
Agile Electric Motor Manufacturing