Global Dynamic Robot Motion Planning for Agile Production
Name of demonstration
Global Dynamic Robot Motion Planning for Agile Production
Main objective
The objective of the project is to demonstrate the value of global dynamic motion planning in agile production by lowering the time it takes to make changes to the setup and making complex robot motions possible.
Short description
The developed system consists of a motion planner for efficient bin picking. This system can solve a complex application with multiple bins, where each bin and the environment in general is flexible and can change during the operation. This has the following advantages:
- No need to program any waypoints for the robot
- Motion planning handles changes in the cell on the fly
- More direct and efficient paths leading to reduced cycle time
- Seamless use of robot mounted 3D camera
Owner of the demonstrator
Adaptive Robotics
Responsible person
- CEO, Joachim Paasche, joachim@adaptiverobotics.com
NACE
C - Manufacturing
Keywords
Robotics.
Benefits for the users
The user will be able to:
- Program a new robot cell without specifying any waypoints for the robot
- Develop more robust cells which can handle changes in the cell on the fly. Less support due to
- fewer production stops.
- Lower development time per new robot cell
- Easier to reprogram a robot cell
- Lower the cycle time per cell
Innovation
- In traditional robot programming, the robot movement must be programmed with predefined waypoint which the robot has to move through. This is tedious, requires a lot thinking, creates movement which are not always optimal and makes the robot cell very inflexible and intolerant to changes. These problems increase even more when objects have variable positioning which is very often the case with vision enabled robot cells such as bin picking. Real time dynamic motion planning removes the above-mentioned challenges. The motion planner uses CAD and/or 3D point cloud as input to understand the environment. Based on this it will calculate the optimal movement for the robot on the fly. In the case of bin picking for instance, this means that the robot finds the optimal path per cycle. In the future with human-robot applications, the robot will continuously adapt the movement of the human and plan its path accordingly.
Risks and limitations
The motion planning software is dependent on accurate information of the environment. If CAD data or 3D point cloud is inaccurate or incorrectly positioned relative to the robot, it can result in a collision. The motion planner is dependent on a robot with an accurate absolute position. Often robots have very high repeatability, while the absolute position might be off. If the absolute position of the robot is inaccurate, it might result in unsuccessful picks, and in the worst-case scenario, collision with the environment. The motion planning software does not have any object detection capabilities. In case of bin picking applications for instance, it is necessary to have a 3rd party object recognition software which can detect objects based on 3D point cloud data.
Technology readiness level
6 - Safety approved sensors and systems are commercially available
Sectors of application
Manufacturing: Bin picking, Machine tending Warehouse logistics: Piece picking, Palletizing, Depalletizing.
Potential sectors of application
Manufacturing: Human robot applications Warehouse logistics: Human robot applications
Hardware / Software
Hardware:
Industrial robot: 5-7 DOF robot for performing the operation. 3D sensor: Sensor for providing point cloud to the system. This is used both for grasp detection and for updating the environment for safe motions. Robotic gripper: Gripper for manipulating the pieces.
Software:
Detection system: Software or dedicated hardware for detecting the grasps, which are sent to the motion planner.
Photos
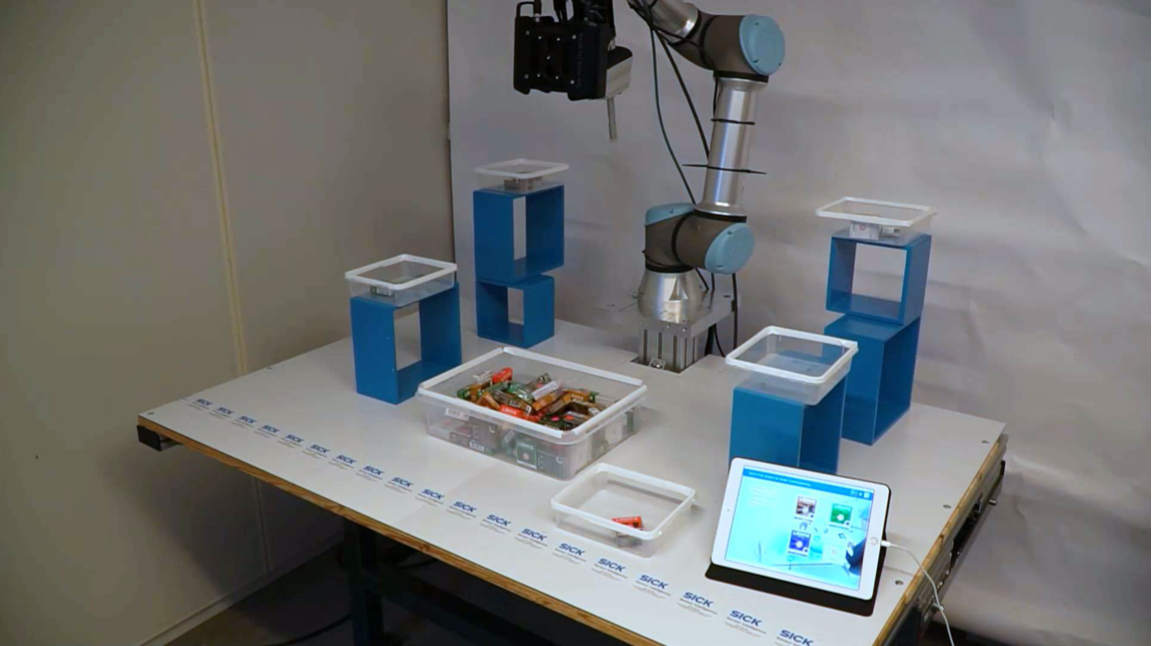
Video
The demonstration setup: - One 6-axis robotic arm - One on-arm 3D camera - A vacuum gripper with one suction cup - 6 separate bins with flexible positioning - Detection software with classification - Motion planner controlling the robot
https://www.adaptiverobotics.com/trinity/adaptive_bin_picking.mp4No modules assigned