Flexible Automation for Agile Production
Name of demonstration
Flexible Automation for Agile Production
Short description
Highly flexible solutions for handling and clamping parts during the assembly process are needed to realize small lot sizes with a high variety. Flexible grippers and jigs are a possible solution. Requirements of different product types must be considered while planning, designing and constructing such systems. The main idea is to develop methods for planning workstations for assembly and handling processes. The use case demonstrator’s task is the automated handling of electronic parts used for LED-lamp production and the assembly of printed circuit boards (PCB).
Owner of the demonstrator
LP-Montagetechnik
Fraunhofer Institute of Machine Tools and Forming Technology
Responsible person
Dr. Ing. Marcel Todtermuschke Marcel.Todtermuschke@iwu.fraunhofer.de
Tel.: +49 371 5397-1301
NACE
C26.1 - Manufacture of electronic components and boards
Keywords
Robotics, Mechanical Engineering, Automation, Assembly, Process Planning.
Potential users
Electronics industry, SMES/larger companies interested in automation
Benefits for the users
The higher degree of automation of the assembly process will result in various positive benefits. The rate of misplaced components will be reduced which results in a reduction of quality errors thus decreasing the amount of time spent on rework. Shifting manual process steps towards being handled by a robot allows the workers to focus on other assembly processes that are still too complex to automate for small batch sizes. This means that the increased automation can dispense with the monotonous work and, if necessary, night shifts at this workstation. Automating the assembly process supports to reduce the impact of a shortage of skilled production workers. The automated assembly process enables a better integration into the factory’s production control software, which improves the possibility to monitor and control the production processes and to react quickly to changes in orders, product variants and lot sizes.
Innovation
Whereas the assembly of surface-mounted devices (SMD) printed circuit boards is highly automated, through-hole-technology (THT) printed circuit boards are still being assembled manually for smaller and medium quantities due to its components having long and thin leads that have to be put through the PCB. The developed demonstrator, however, performs the automated assembly with THT components. The robot is able to remove components from different removal situations, e.g. precisely positioned parts from a blister pack, as well as completely unaligned parts in a box.
Risks and limitations
With the current design of the manipulation tool using a suction cup, it is not possible to automate the handling of all existing components due to their surface form. For other types of the gripper, such as parallel grippers, the available place on the PCB between components is not sufficient. Therefore, the components necessary for assembly have to be divided between the workers and the robot.
A possible risk is that the demonstrator’s performance will not keep up with the worker’s in the real production environment, thus increasing production times or the implementation effort of the demonstrator.
Technology readiness level
4 – Component and/or breadboard validation in laboratory environment
Sectors of application
Electronic Industry, .
Potential sectors of application
Mechanical Engineering Industry
Hardware / Software
Hardware:
Kawasaki RS007LFF60
Camera
Ring light
Controller
Software:
Keyence
KR-Term
Photos

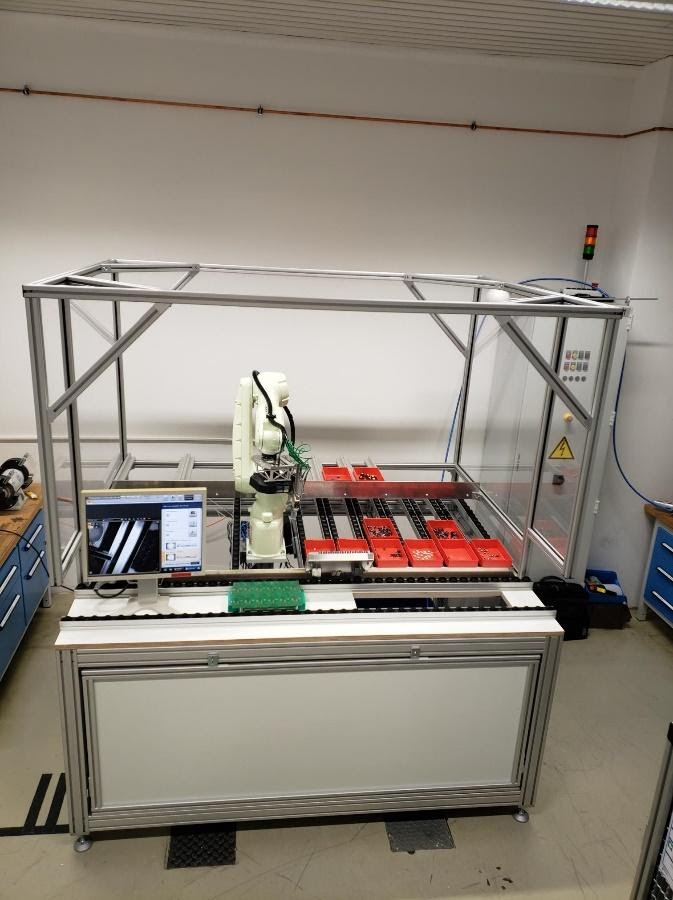
Handling and Assembly
This module provides a guideline on how to plan a workstation that has to perform handling and assembly act...
LEARN MORE
Vision System and Quality Assurance
A vision system serves as an aid for detecting optically detectable features and converting them into data ...
LEARN MORE
Trainings
To learn more about the solution, click on the link below to access the training on the Moodle platform
Flexible automation for agile production