Automated Robotic Welding
Name of demonstration
Automated Robotic Welding
Main objective
The objective of the demonstrator is to showcase how an industrial robot can be used for robotic welding and wire arc additive manufacturing (WAAM).
Short description
The industrial robot has an important role in the automation of the manufacturing industry and has considerably contributed to the improvement of profitability and working environments. However, there are still many tasks in the manufacturing industry that requires heavy work, such as welding and additive manufacturing based on welding.
Owner of the demonstrator
The Arctic University of Norway
Responsible person
Scientific fellow. M.Sc
Halldor Arnarson
Department of Industrial Engineering
UiT the Arctic University of Norway
halldor.arnarson@uit.no
NACE
C25.1.1 - Manufacture of metal structures and parts of structures
Keywords
Wire Arc Additive Manufacturing, WAAM, Additive manufacturing with industrial robot, Robotic welding, IoT.
Potential users
Manufacturing Industry, Automotive and Aerospace Industry
Benefits for the users
– The demonstrator exploits an industrial robotic arm to automate repetitive welding jobs that result in more consistent welds and fewer mistakes.
– Remote programming of the system (offline programming). This allows for verification of the welding program before running it on the physical robot and you can program the system without interrupting the current production which can save costs.
– Using robotic welding releases humans from the labor-intensive and hazardous work environment.
– The system can be used for additive manufacturing, to repair broken parts or 3D print parts. This can be a fast and cost-effective method to create or fix damaged parts.
Innovation
Robots are usually programmed with a robot controller and the physical robot to teach positions. This demonstrator uses a simulation software as a programming tool and a digital twin copy of the physical robot for robot programming.
The system allows for remote programming and configuration without being physically in the production environment. This creates a flexible method for re-programming and the possibility to test the program in the simulation software before executing it on the physical system.
Risks and limitations
- Welding induces a lot of stress on the welded part. This has to be considered when using the system for additive manufacturing with a TIG welder.
- Since robots are connected through the internet, further consideration on cybersecurity should be done to avoid cyber attacks.
- Using TIG welding for additive manufacturing produces considerable heat, which requires a lot of cooling.
Technology readiness level
6 - Safety approved sensors and systems are commercially available
Sectors of application
Aerospace - the parts created from the demonstrator have strong features, Automotive - the demonstrator has significant use as a single car can require thousands of welds in assembly, Manufacturing - performing repetitive work which can easily be automated with a robotic welder, Petroleum industry - welding oil and gas pipelines..
Potential sectors of application
3D printer for Aerospace and Automotive industry
Patents / Licenses / Copyrights
The module is made for the purpose of providing a proof-of-concept. The designed structure, upsetting, and its associated files are free of charge for internal and external use during the project period.
The software and other related files are under the standard MIT license: Copyright 2021 The Arctic University of Norway (UiT) Permission is hereby granted, free of charge, to any person obtaining a copy of this software and associated documentation files (the "Software"), to deal in the Software without restriction, including without limitation the rights to use, copy, modify, merge, publish, distribute, sublicense, and/or sell copies of the Software, and to permit persons to whom the Software is furnished to do so, subject to the following conditions: The above copyright notice and this permission notice shall be included in all copies or substantial portions of the Software. THE SOFTWARE IS PROVIDED "AS IS", WITHOUT WARRANTY OF ANY KIND, EXPRESS OR IMPLIED, INCLUDING BUT NOT LIMITED TO THE WARRANTIES OF MERCHANTABILITY, FITNESS FOR A PARTICULAR PURPOSE AND NONINFRINGEMENT. IN NO EVENT SHALL THE AUTHORS OR COPYRIGHT HOLDERS BE LIABLE FOR ANY CLAIM, DAMAGES OR OTHER LIABILITY, WHETHER IN AN ACTION OF CONTRACT, TORT OR OTHERWISE, ARISING FROM, OUT OF OR IN CONNECTION WITH THE SOFTWARE OR THE USE OR OTHER DEALINGS IN THE SOFTWARE.
Hardware / Software
Hardware:
KUKA robot
Software:
Visual Components Premium
OPC UA
Python
Trainings
The training material is under development: http://heinlein.mech.upatras.gr/trinity/use-case-5/
Photos
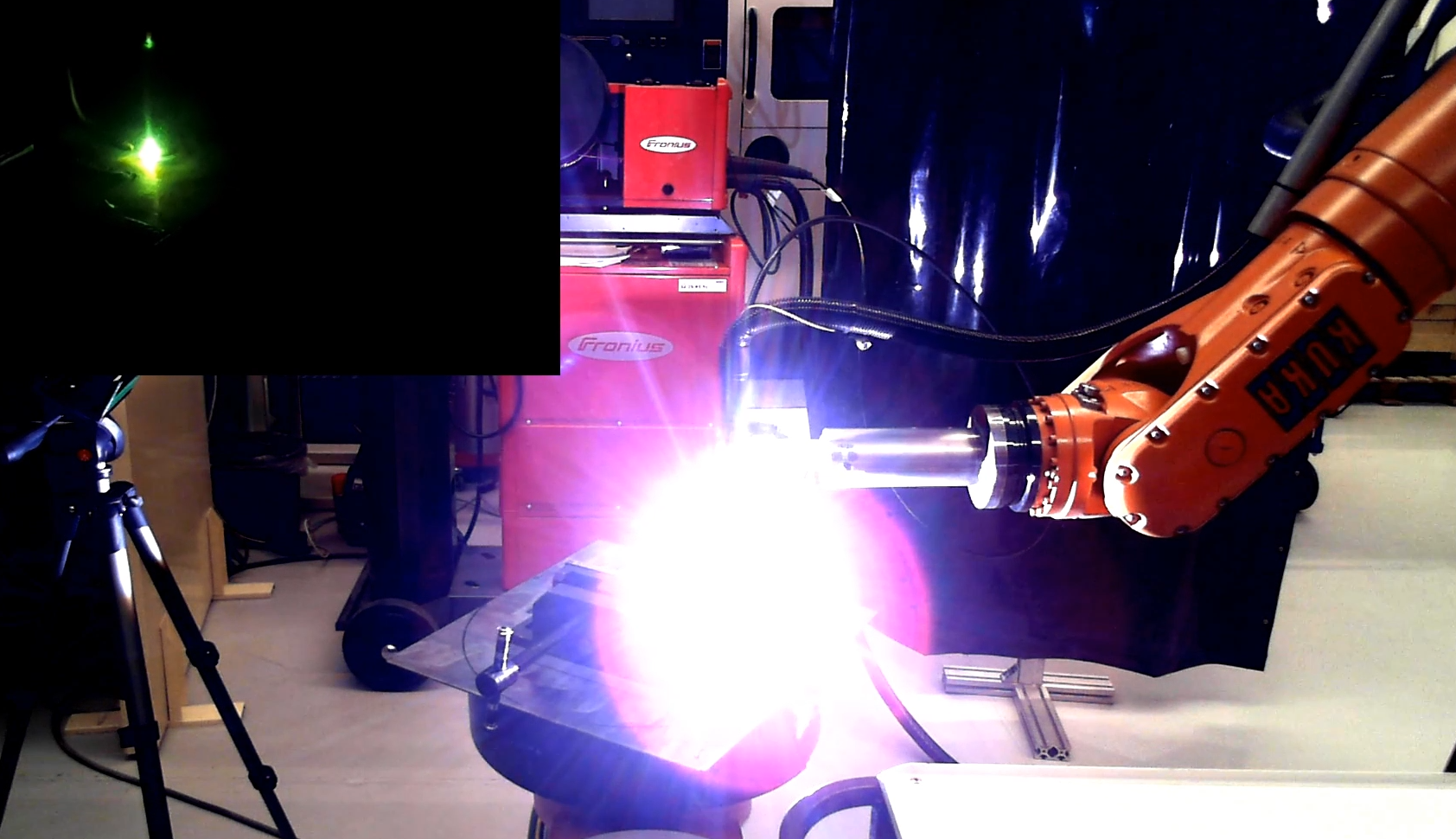
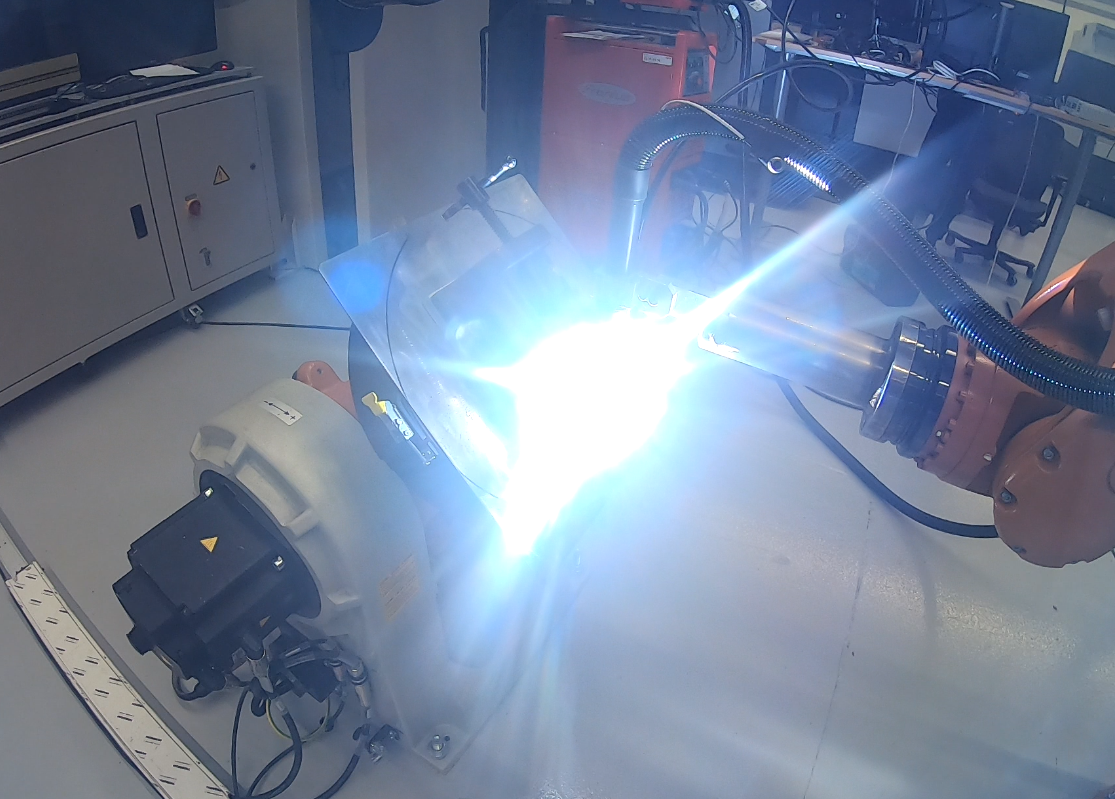


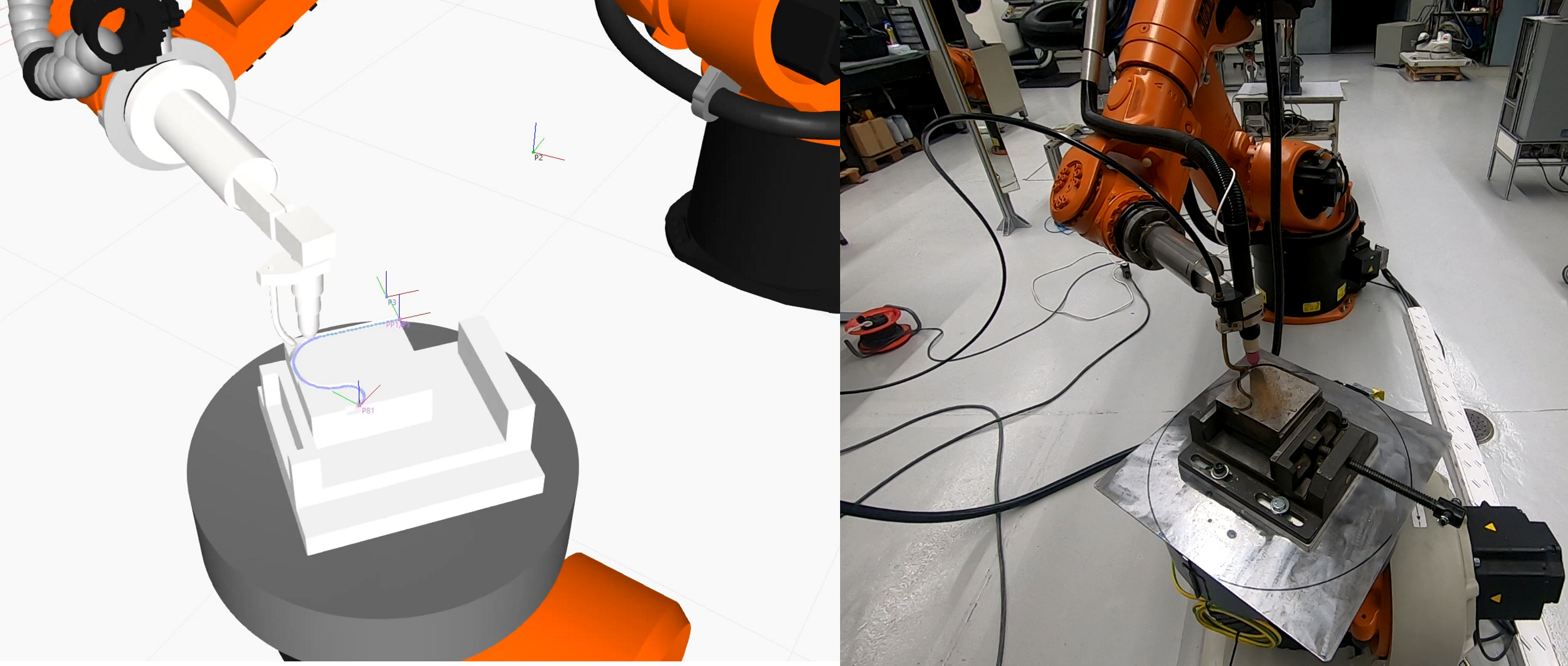
Trainings
To learn more about the solution, click on the link below to access the training on the Moodle platform
Wire arc additive manufacturing with industrial robots