Artificial Intelligence Based Stereo Vision System
Name of demonstration
Artificial Intelligence Based Stereo Vision System
Main objective
Detect, recognize and classify randomly distributed objects that are overlapping each other in a pile and pick them up by a robotic arm.
Short description
A lot of industrial processes involve operation with a large number of different objects with an arbitrary location. It is hard to automate these kinds of processes because sometimes it is impossible to predetermine the positions for these objects. To overcome this issue, we integrate 3D and 2D computer vision solutions with AI and robotic systems for object detection, localization and classification.
Owner of the demonstrator
Institute of Electronics and Computer Science
Responsible person
Researcher Janis Arents janis.arents@edi.lv
NACE
C - Manufacturing
Keywords
Robotics, Manufacturing, Computer Vision, Artificial Intelligence, Bin-Picking.
Potential users
Tech integrators, SMEs
Benefits for the users
Implementing AI-based solutions can be effective in the manufacturing industry by improving process and product quality, reducing cycle time, decreasing costs and much more.
The use of AI-based stereo vision systems can reduce adjustment time, the complexity of the system and is more flexible to changes in manufacturing lines.
The AI-based stereo vision system of UC17 can be trained to detect and estimate the pose of different objects that are randomly distributed in a pile, therefore, enabling automation of industrial processes involving a different kind of objects with unpredictable positions.
Innovation
Traditionally working with randomly distributed objects requires human resources or dedicated sorting hardware that usually is spacious, expensive and hardly adjustable if product assortment changes. The problem becomes more complex if different kinds of objects are mixed in one pile and need to be sorted and structured into determined position and orientation. The proposed system deals with this kind of uncertainty of the environment by use of AI-based computer vision system that can detect and estimate the pose of such objects. In combination with an industrial robot detected objects can be picked up and placed in a determined position.
Risks and limitations
This use-case demonstration has been built upon the Robot Operating System (ROS). The compatibility with different hardware depends on the ROS driver availability of the intended hardware, such as Industrial Robots and 3D cameras. The system has been tested with ROS supported hardware: Universal Robots UR5 industrial robot and multiple RGBD cameras, such as Intel RealSense, Kinect and Zivid.
Technology readiness level
4 – Component and/or breadboard validation in laboratory environment
Sectors of application
Manufacturing.
Potential sectors of application
Any environment that can use AI based computer vision for their benefit
Hardware / Software
Hardware:
Industrial robot
RGBD camera
ROS PC
Software:
ROS
Trainings
Under development
Photos
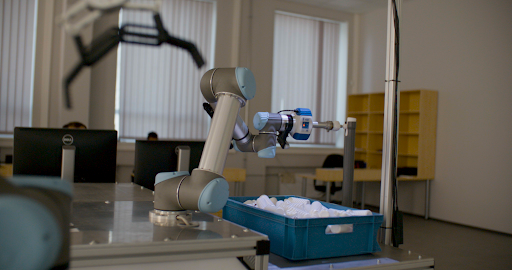
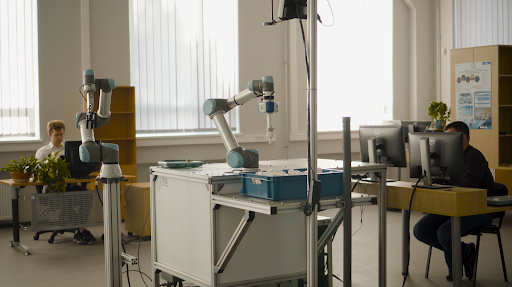
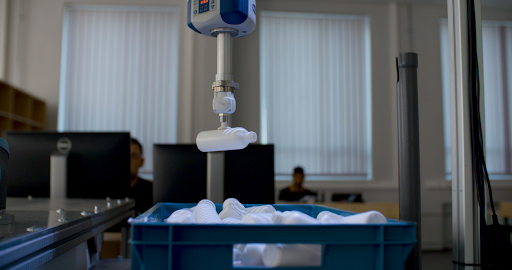
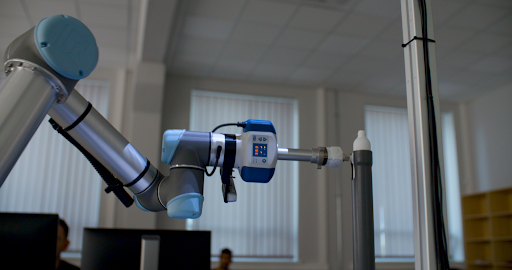

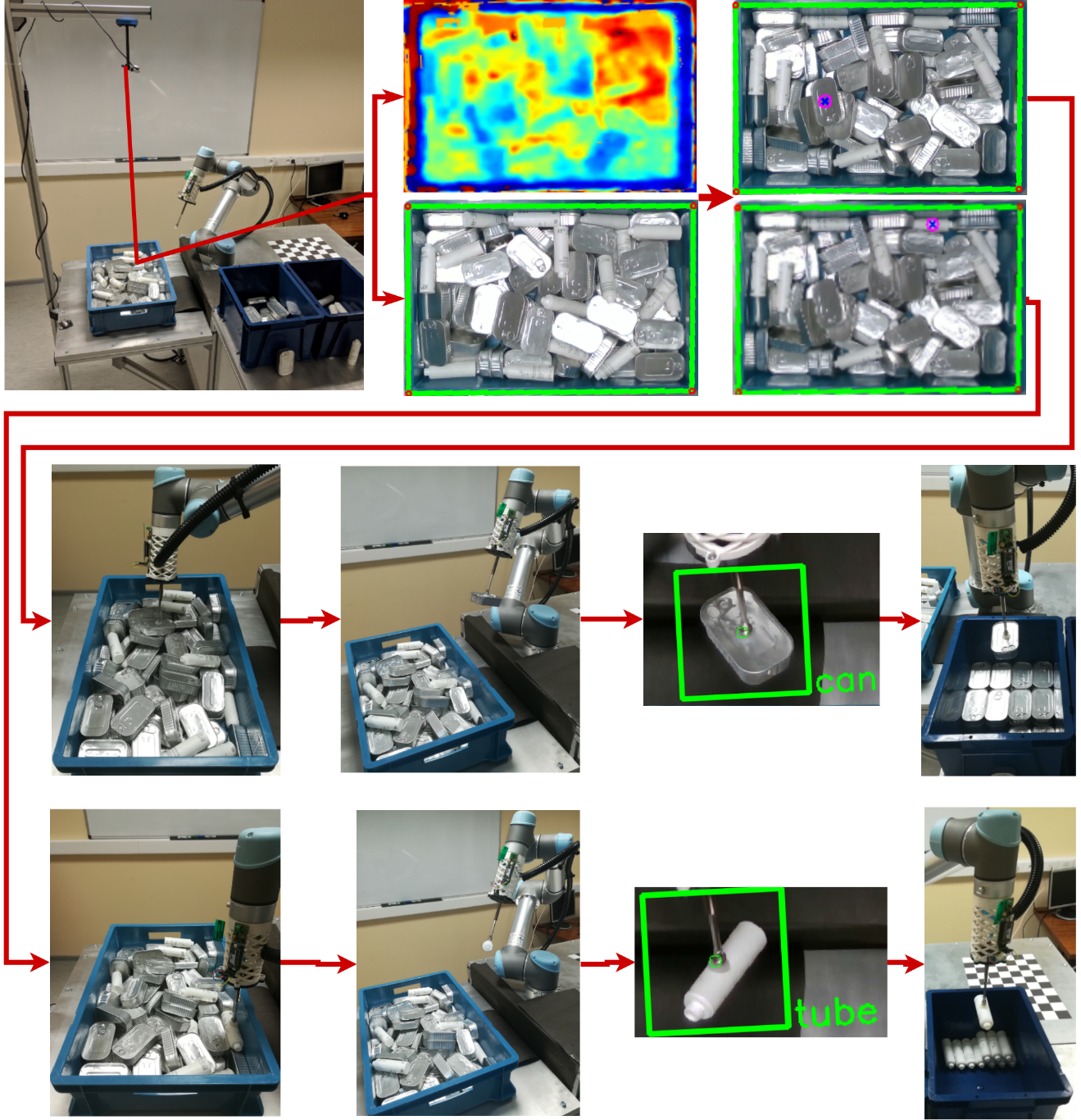

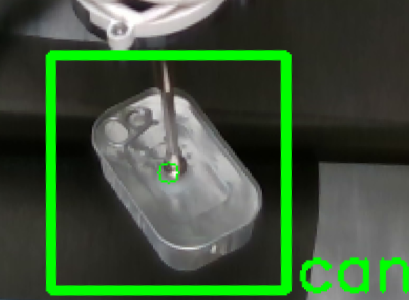
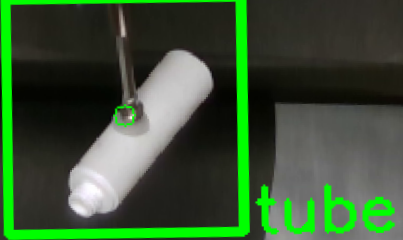

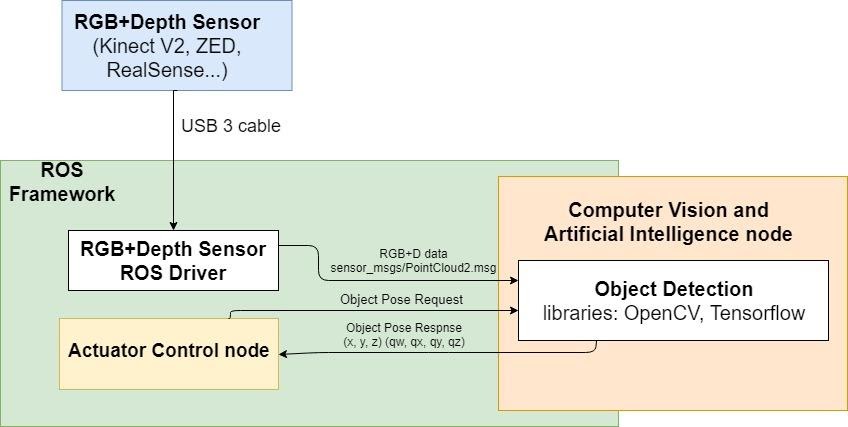
Object Classification
A deep convolutional neural network (CNN) is used to classify and sort objects. This is a robust and fast i...
LEARN MORE
Object Detection
The object detection module is used to perceive the changing environment and modify systems actions accordi...
LEARN MORE
Robot Control for bin-picking
Robot control for bin picking works as an integrator of object detection and classification modules or any ...
LEARN MORE