Robotized Serving of Automated Warehouse
Name of demonstration
Robotized Serving of Automated Warehouse
Main objective
The demonstration was created as a fully functional, scaled-down, table-top model of an automated warehouse served by an omnidirectional mobile robot to be used as an attraction in exhibitions. The goal is to demonstrate the feasibility of using omnidirectional mobile robots in intralogistics.
Short description
Agile manufacturing is one of the main trends in research and development nowadays. The TRINITY project aims to increase the agility of various manufacturing processes. This section describes the hardware and software infrastructure and requirements, furthermore, the available modules offered of the Use Case demonstration titled Robotized serving of automated warehouse of the TRINITY project. The demonstration incorporates existing automated ground vehicle (AGV) solutions and other emerging technologies widely used in intralogistics: for example, optical line following and visual serving of an omnidirectional mobile robot. The potential users are SMEs who are dealing with smart assembly involving mobile robots.
Owner of the demonstrator
Budapest University of Technology and Economics
NACE
H52.1 - Warehousing and storage
Keywords
Robotics, Vision System, Logistics, Collaborative Robotics, Machine Vision.
Potential users
Intralogistics, AGVs and AMRs
Benefits for the users
Possible benefits of the demonstration are applications with mobile robots, optical character recognition, target detection, and controlled maneuvering, as well as path tracking without compromising safety. Furthermore, increased digitalization, new functionalities of systems, and increased efficiency. Applications based on this demonstration can optimize the traceability, speed, and accuracy of routine operations in warehousing and manufacturing.
Innovation
Autonomous guided vehicles, also known as AGVs, are often used in applications where material must be moved between facilities, covering distances greater than 300 meters. Mobile robots can also bring value in long distance applications if multiple inputs and output locations are required, especially if it’s important to make changes during transportation. Autonomous mobile robots (AMRs) are a good solution for last-meter deliveries where flexibility is required.
Risks and limitations
The demonstration is a closed system with no need for access to the internet. Nevertheless, cybersecurity issues need to be taken into account to ensure the fluent and safe operation of the system in all conditions.
The setup consists of a laptop, a mobile robot (FESTO Robotino®), and an onboard Wi-Fi access point mounted on the robot. The mobile robot runs back and forth from the User to the Wending machine, serving the desired product. The elements of the setup are on top of a 2x2 m table. The User stands by the table and starts a delivery process by showing the desired product’s card to the robot’s camera.
Technology readiness level
5
Sectors of application
Automated storage and retrieval systems , Automotive industry, Manufacturing.
Potential sectors of application
Training material is under development.
Patents / Licenses / Copyrights
Hardware / Software
Hardware:
Omnidirectional Mobile Robot
Pen Wending Machine
Microcontroller
FESTO Robotino®
Software:
LabVIEW™
Optical Character Recognition
Trainings
Training material is under development.
Photos
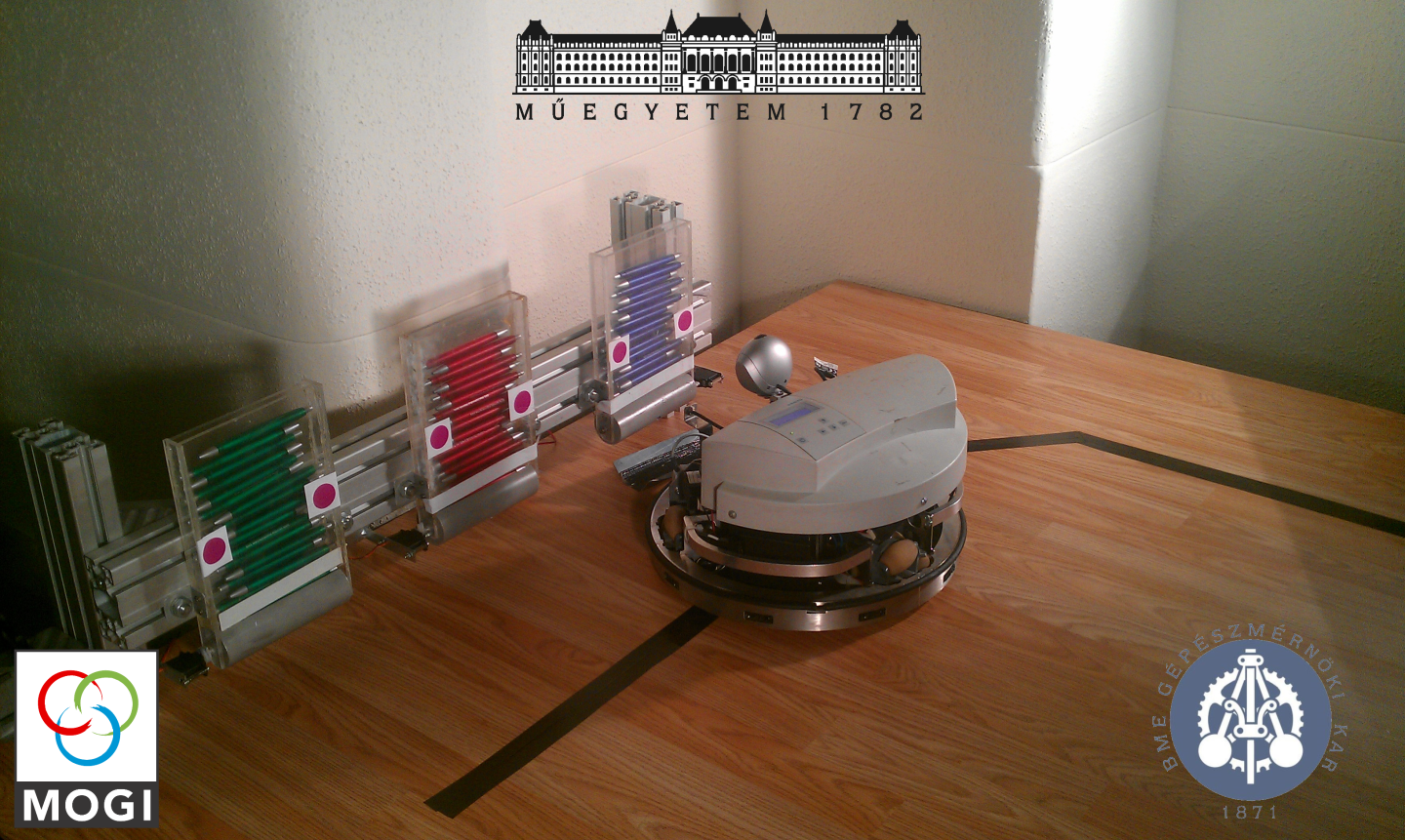
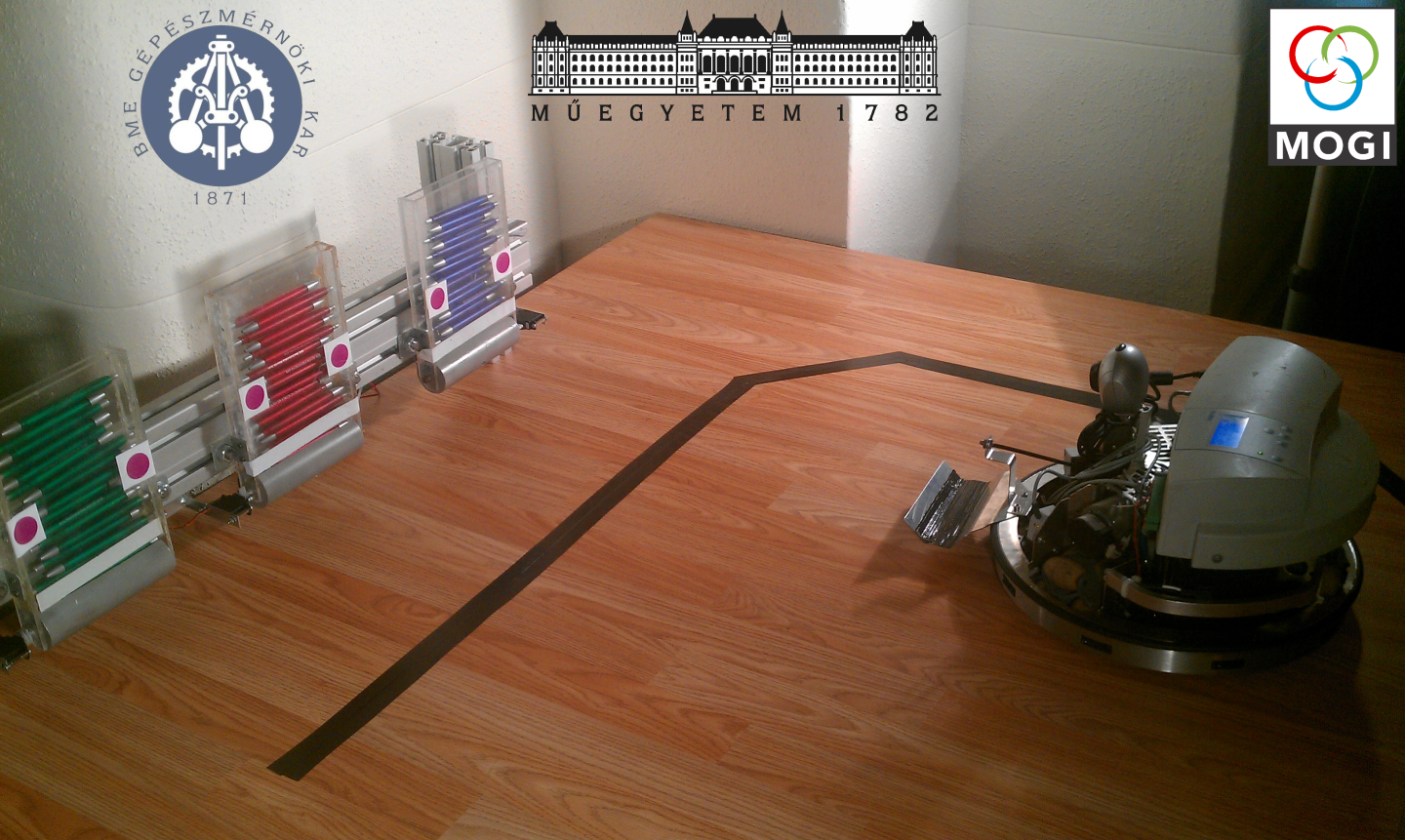
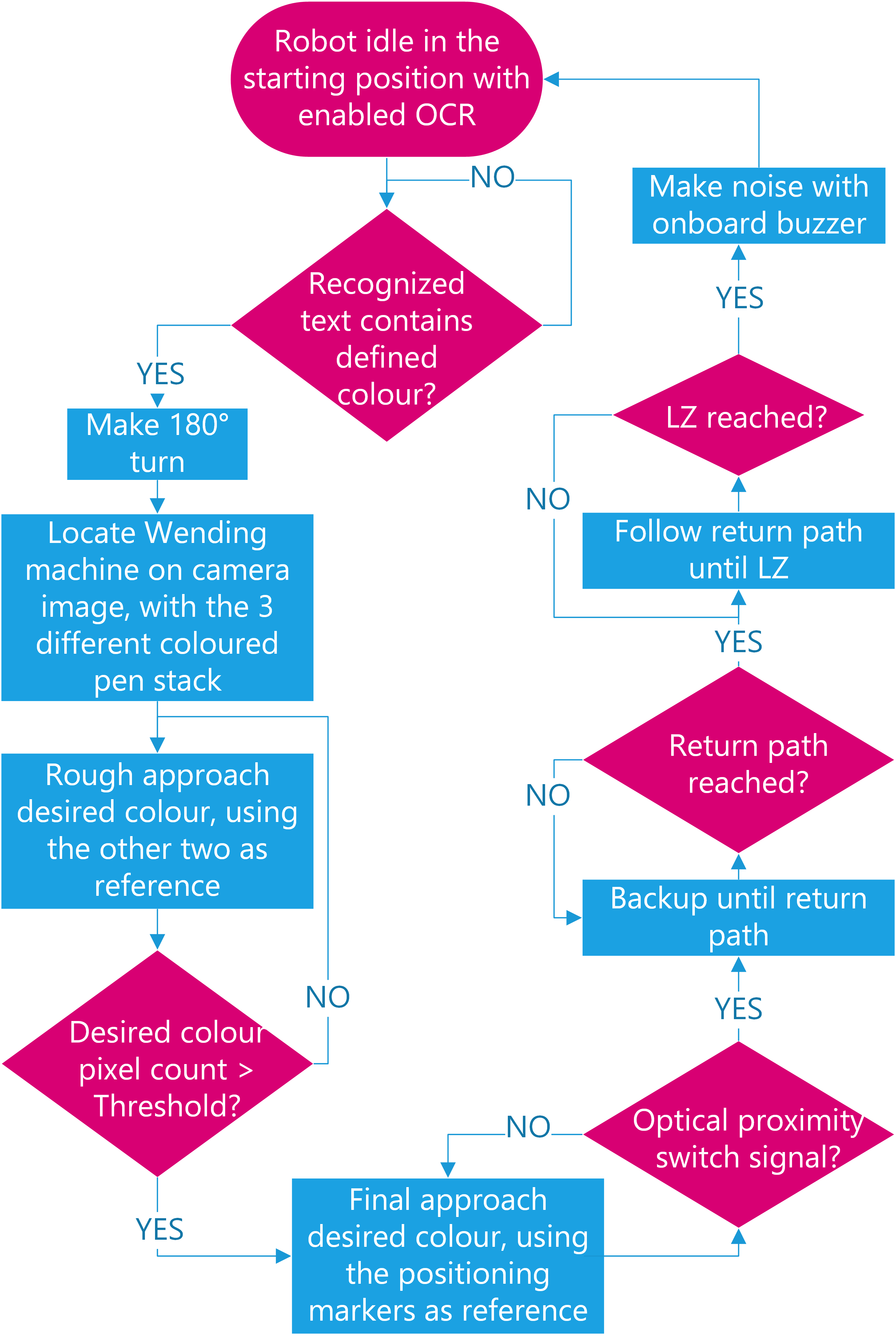
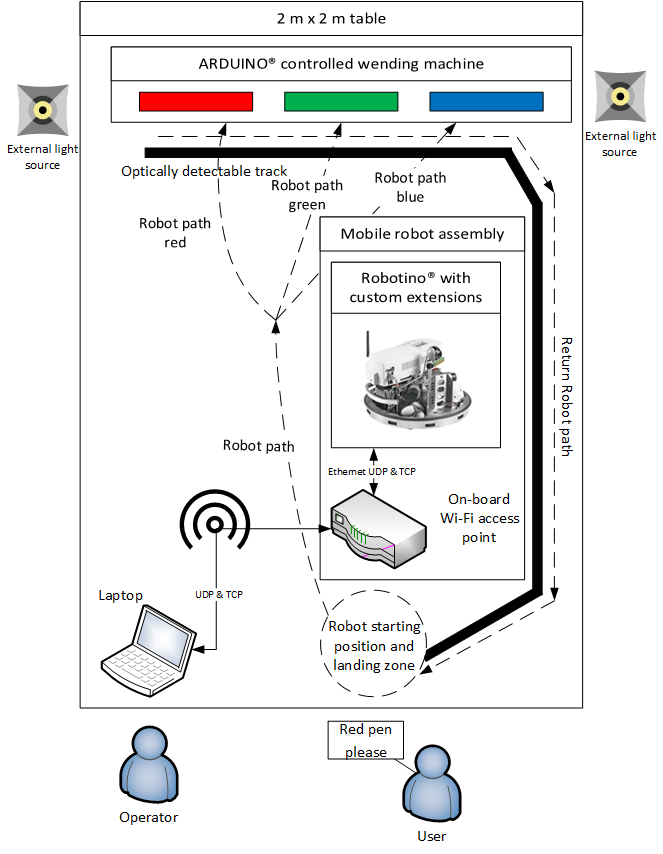
Environment Detection
This module consists of three sub-modules, each performing different sensory tasks.
Optical character...
LEARN MORE
Mobile Robot Motion Control
This module consists of two sub-modules, each performing different motion control tasks.
Open-loop mo...
LEARN MORE
Queued Message Handler Software Architecture
The main functionality of the module is to organize the whole software in separate tasks (modules) and exec...
LEARN MORE
Robotino® communication
The main functionality of the module is to communicate with the Robotino® . The Robotino® is a mobile rob...
LEARN MORE
Trainings
To learn more about the solution, click on the link below to access the training on the Moodle platform
Robotized serving of automated warehouse