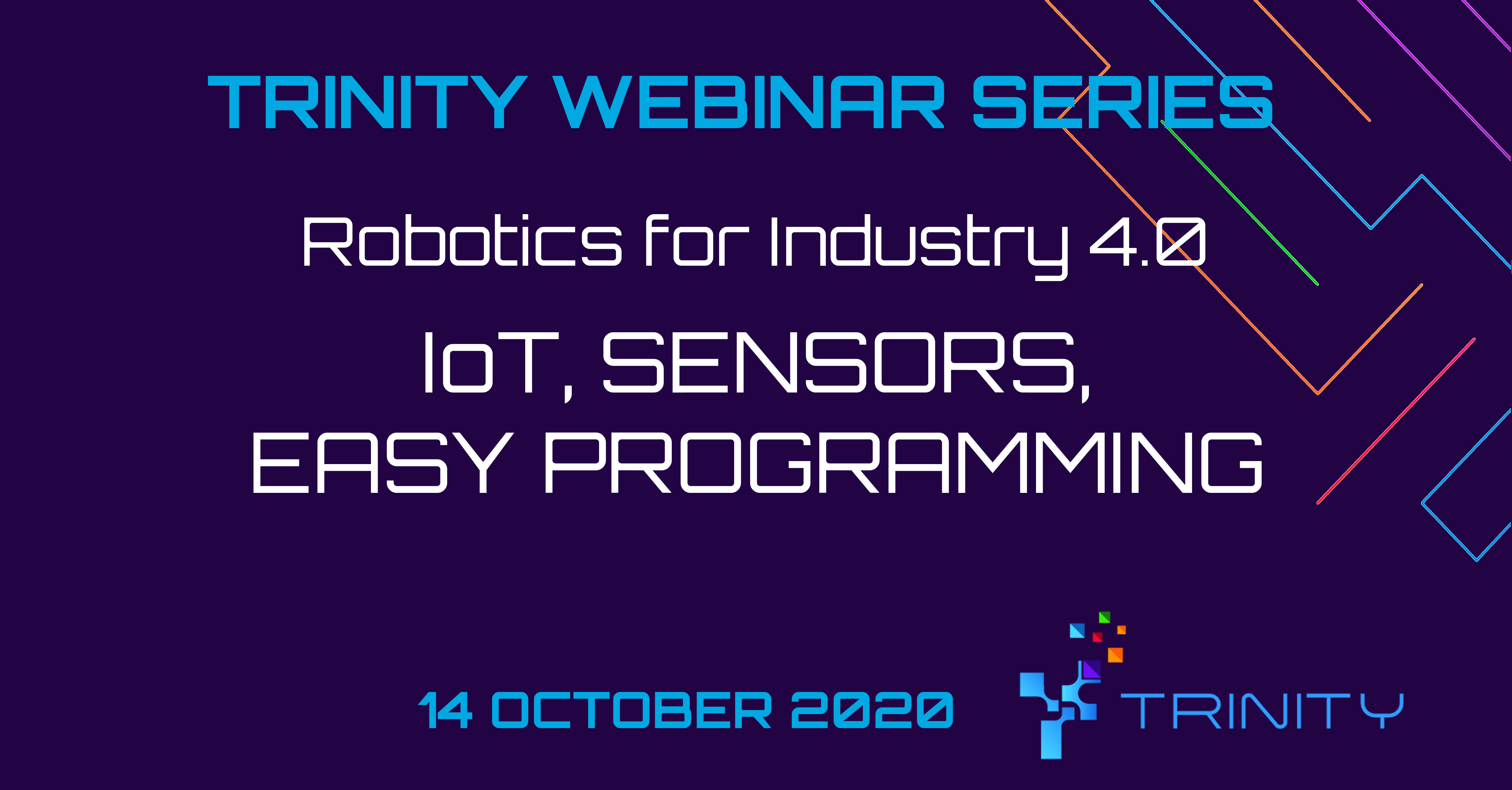
Robotics for Industry 4.0 – IoT, sensors, and easy programming
2020 10 20
On 14 October 2020, TRINITY project continued with another episode of its webinar series on Robotics for Industry 4.0. The aim of the series was to present to the broader audience the robotic demonstrators that SMEs are currently implementing thanks to TRINITY funding, obtained through the first round of open call closed in March 2020. Each project will run from 6 to 12 months, and the SMEs can benefit of TRINITY expertise to benefit the most from their innovative robotic solutions for the all duration of their implementation.The webinar series is made of 4 events, each one grouping the demonstrators according to their field of application. In this episode, the companies that are now implementing their robotic demonstrators have presented their innovative solutions tackling IoT, sensors, and easy programming issues.
After a brief introduction on the TRINITY project and the opportunities that SMEs can have through our open calls, the first demonstrator to be presented was ARGRIND – Advanced robotics for accurate grinding of complex metal parts by Mrs Sara Mata, Researcher at Ideko, Spain. As the name suggests, AGRIN wants to perform a successful accurate grinding of a complex metal part with a complete robotic solution, including a controller to guarantee homogeneous material removal, and a companion software to accurately simulate the ground surface.
Possible benefits gained with the implementation of ARGRIND are the minimization of robot programming time for each new part model to reduce lead time, prevention of part scrapping during the validation tests of new parts thus reducing set-up costs, and implementation of higher automation and efficiency for increased competitiveness.
▶ Watch the full presentation of ARGRIND here.
▶ Watch the full presentation of SNIPE here.
Robobend can be used at any of the existing press brakes replacing operators and increasing efficiency. The interfacing between the robot and the machine, the standard robot cell design (feeder + manipulator + collector as a standard setup) and the conversion of drawings to programs for the machine and movements of the robot make up a kit for process standardizing. Possible benefits that can be achieved include a reduced system set-up and programming time (up to 10-20 minutes from one batch to the next), reduction in BOM costs up to 20%, bending time cycle: approximately 10 seconds per bend and bending items: size up to 1.5m and 10 kg weight.
▶ Watch the full presentation of ROBOBEND here.
▶ Watch the full presentation of Digi-SAAP here.
▶ Watch the full presentation of MYWAI 4 ROBOTICS here.
Watch the complete recording
⏬⏬⏬