Collaborative Robotics In Large Scale Assembly, Material Handling And Processing
Name of demonstration
Collaborative Robotics In Large Scale Assembly, Material Handling And Processing
Main objective
Main objective of this use case is to demonstrate the possibilities of large-scale industrial robotics in collaborative tasks. This use case demonstrates a novel combination of safety sensors and additional devices that make true human-robot collaboration possible, while still following safety regulations and standards. In addition, dynamic and flexible robot trajectory generations are demonstrated.
Short description
An agile industrial robotization of a large-scale material handling, processing or prefabrication where robots and people will process components collaboratively is demonstrated. The working zone is monitored dynamically and information is provided to both parties: the human worker and robot. Different multimodal human-computer interaction methods are evaluated. This ultimately leads to more agile robotized production, where humans and robots may work together in tasks such as large-scale assembly, material handling and processing
Owner of the demonstrator
Centria University of Applied Sciences
Responsible person
Senior Research Scientist, Sakari Pieskä
tel.: +358 44 449 2564
NACE
C33.2 - Installation of industrial machinery and equipment
Keywords
Industrial robot, Collaborative robot, Robot safety, Robot trajectories.
Potential users
Robot and automation integrators: companies that program and deploy industrial robots for automated manufacturing tasks can use the demonstrated systems in realised robot cells. Companies dealing with large-scale materials: companies carrying out large-scale material handling, processing or component pre-fabrication. Typically the robot integration is bought as a service from the aforementioned operators.
Benefits for the users
Enhanced and dynamic safety: more flexible production and operations related to robotics.
Human-robot-collaboration: HRC using industrial size robots.
Saved space: smaller factory footprint and therefore lowered costs due to fenceless robot cells.
Innovation
Conventionally, industrial robots have been isolated by fences to prevent accidents and as a result, tasks involving large-scale workpieces and human interaction have been challenging to implement into robotized production. While still following regulations and standards, it is possible to implement safe fenceless industrial robot cells that allow a true human-robot collaboration. This demonstration is a novel combination of multiple safety-related sensors of which some are safety-approved and others are additional sensors increasing agility, flexibility and safety of the manufacturing process.
Risks and limitations
Lack of incompatible specific software needed in integration may be a limitation, especially for aged industrial robots. Every robot needs a safety software (e.g. ABB SafeMove, KUKASafety) to assure safe and reliable operation. For aged industrial robots the modern software is not necessarily available.
Technology readiness level
6 - Safety approved sensors and systems are commercially available
Sectors of application
Construction, Mechanical engineering.
Potential sectors of application
Maritime industry and Automotive industry
Patents / Licenses / Copyrights
Individual HW components are commercial off-the-shelf products.
Usage of modules is free excluding AutoMAPPPS, which is property of Convergent IT.
CloudCompare is released under GPL.
Other software developed at Centria is released under MIT license.
Hardware / Software
Hardware:
Safety laser scanner: e.g. Pilz PSENscan or Sick S300 safety scanner for spatial robot cell safeguarding.
Microwave radar: e.g. Sick SafeRS microwave radar that operates in challenging industrial environment containing dust, smoke, darkness, steam etc. for person detection.
Indoor positioning system: additional safety system of RF tracking or other precise indoor positioning system such as Quuppa Intelligent Locating System.
360 camera: e.g. 360Fly as an additional safety system that together with artificial intelligence can be used for person detection.
3D point cloud creation hardware: 3Dcamera: e.g. 3D Kinect, Intel RealSense, Orbec or LIDAR or 3D Scanner e.g. PhotoXi or Artec Leo 3D Scanner. Used for robot trajectory generation
Software:
ROS and/or ROS-Industrial: dynamic trajectory programming
AUTOMAPPPS: reactive (online) robot trajectory programming
CloudCompare: 3D-point cloud processing
RoboDK: dynamic trajectory programming, robot programming in general, and simulation
CDS Config and diagnostic software: configuration and diagnostic software for SICK safety products
SICK safeRS Designer: configuring and diagnostics of safe radar sensor(s)
Quuppa Positioning Engine (QPE) or similar for indoor positioning: used to calculate tracking tag locations based on information tags are transmitting to the server
Custom software for other additional sensors: accessing and analysing data from 3D cameras, 360 cameras, LIDARS and 3D scanners. machine learning framework such as PyTorch
Trainings
Online training material will be available through the TRINITY training platform that contains separate training material for use cases and modules.
Photos
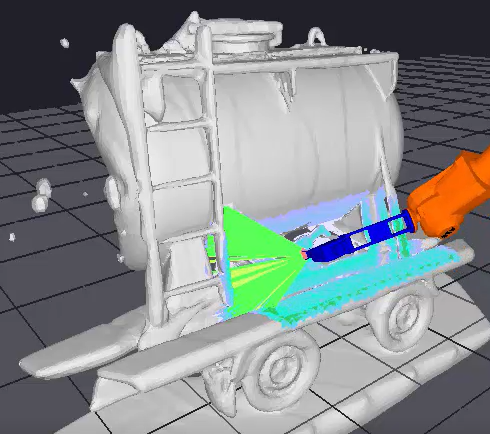

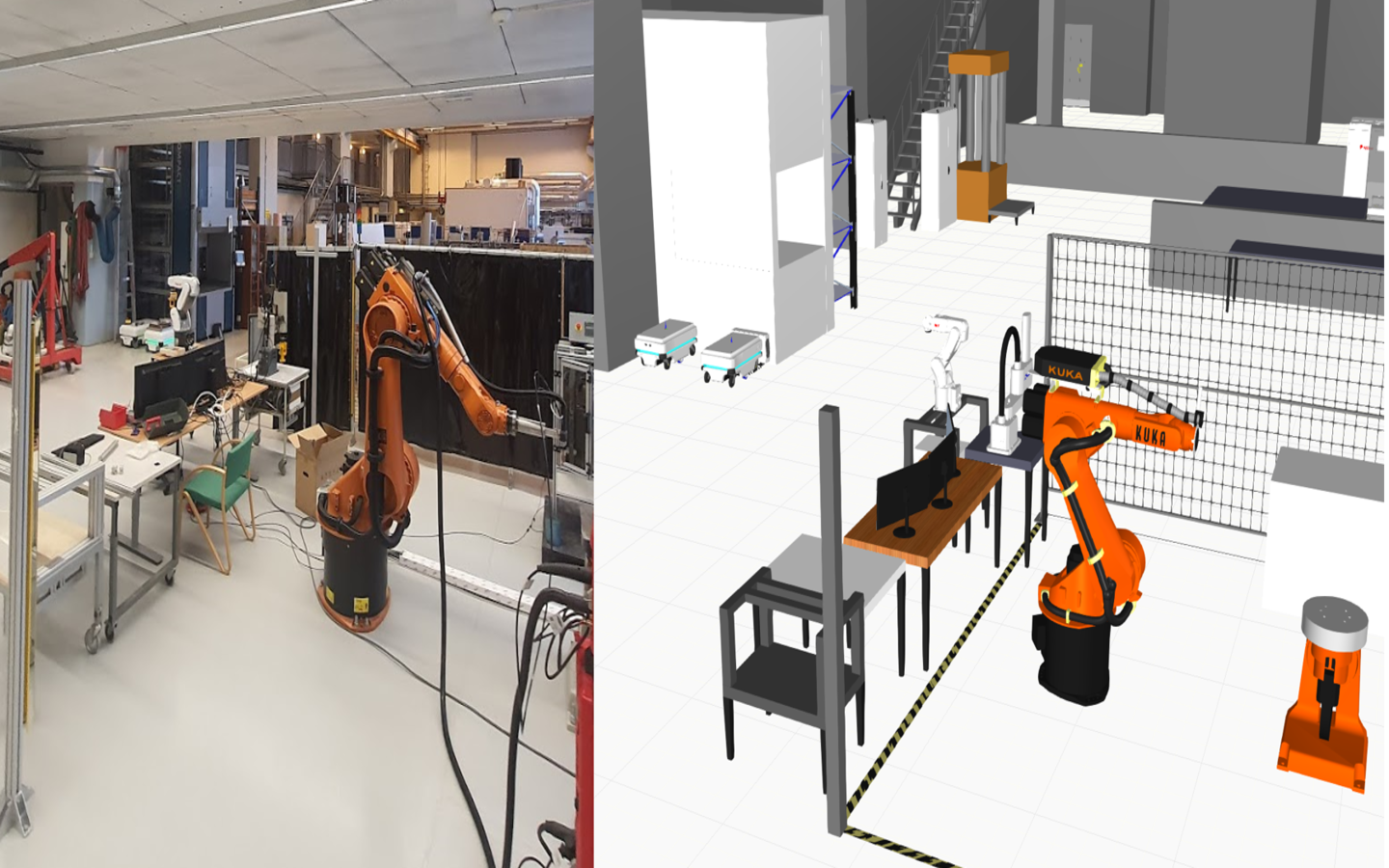
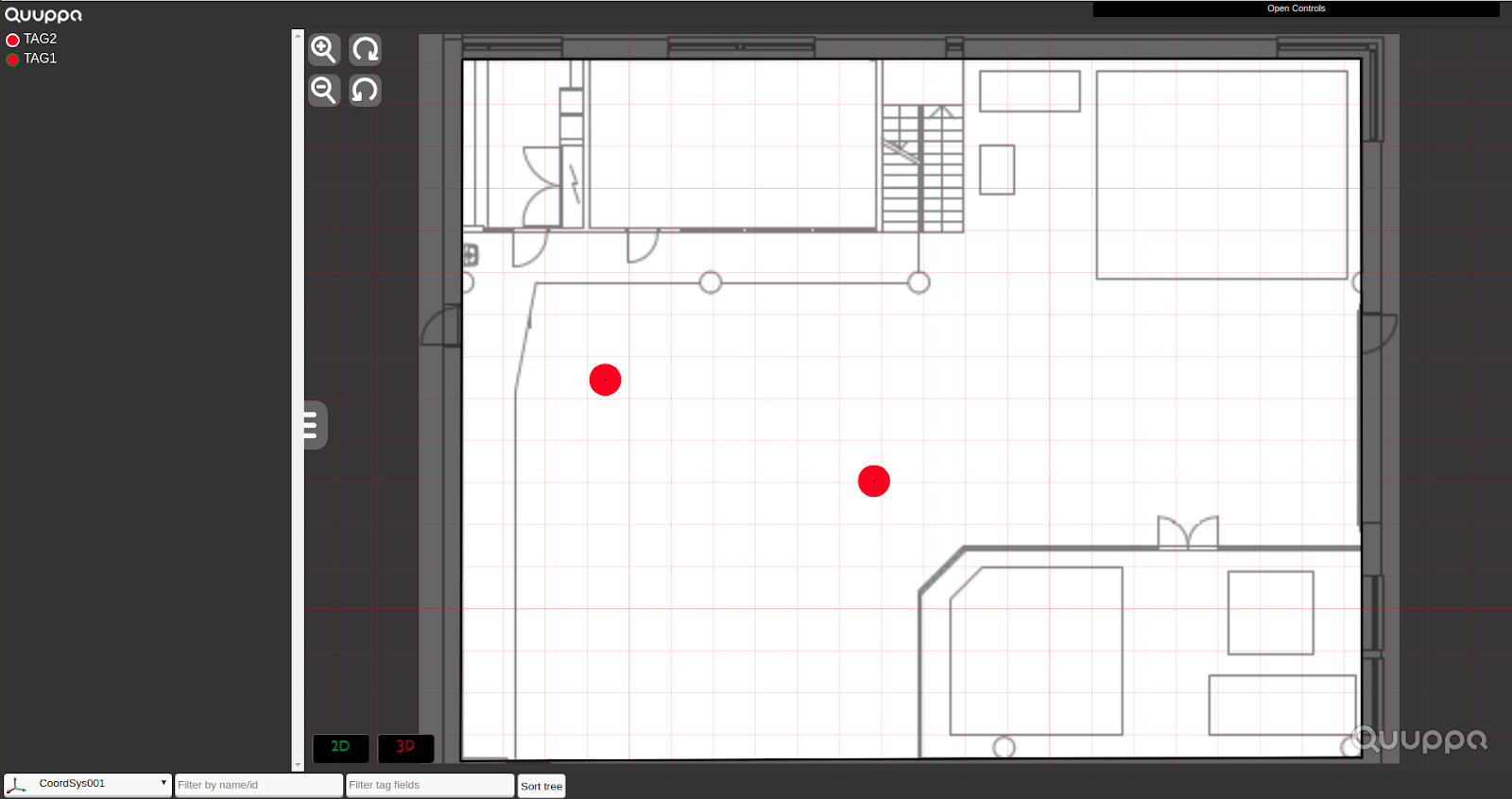
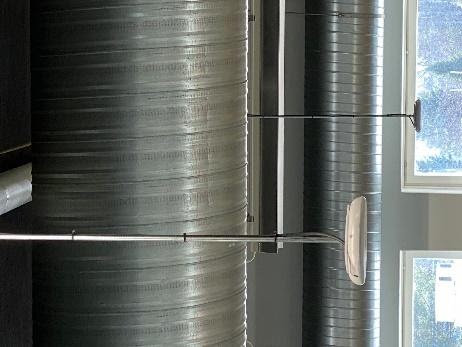
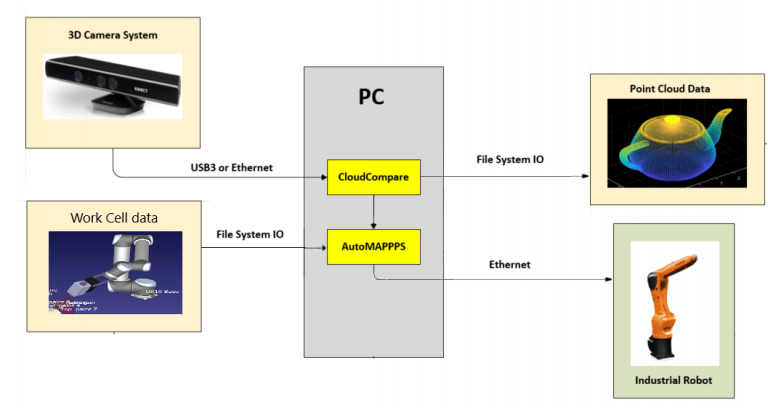
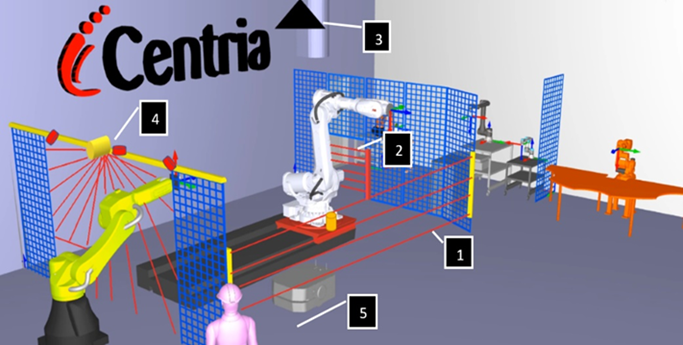
Dynamic Robot Trajectory Generation Based on Information from 3D camera
This module provides a flexible and adaptive way to create robot trajectories dynamically based on point cl...
LEARN MORE
Online Trajectory Generation with 3D camera for industrial robot
this module provides depth-based real-time information of workspace for generating dynamic trajectories for...
LEARN MORE
Safe Human Detection in a Collaborative Work Cell
Creating safety areas: flexible and adaptive creation of dynamic safety areas is based on information from ...
LEARN MORE
Trainings
To learn more about the solution, click on the link below to access the training on the Moodle platform
Collaborative robotics in large scale assembly, material handling and processing