Deployment of mobile robots in collaborative work cell for assembly of product variants
Name of demonstration
Deployment of mobile robots in collaborative work cell for assembly of product variants
Short description
The following use case introduces mobile robots equipped with manipulators in a shared workplace to assist assembly operations in a collaborative work cell for assembly of product variants. The potential application sector for such use case is foreseen to be in SMEs and large-scale companies that need flexible mobile robotic solutions.
Owner of the demonstrator
Flanders Make
Responsible person
dr. ir. Raheel Afzal, trinity@flandersmake.be
NACE
C28 - Manufacture of machinery and equipment n.e.c.
Keywords
Collaborative robots, Mobile Manipulation, ROS, Mobile Robots, Robot control.
Potential users
The potential users can be any company small or large that has the need to deploy mobile robots. It is especially useful for companies that are engaged in assembly operations and requires material transfer from warehouse to assembly stations.
Benefits for the users
Mobile manipulators collaborating in such use cases will allow the deployment of robotics in manufacturing operations with unlimited reach. The onboard and external sensing systems with the ability of mobile manipulation enable the realization of autonomous and agile manufacturing that can cope with variability in the manufacturing processes and provide extensive flexibility in assembly operations.
Innovation
This demonstration will showcase the capabilities of mobile manipulators in work places shared by humans. The mobile manipulator will be able to assist in logistics of different tasks being performed in the work cell by navigating to the pick points of different parts, picking and kitting, and dropping the parts to the designated drop points. Accurate localization of the robot in an indoor working environment is fundamental for precise navigation and manipulation. The platform which will be used for the demonstration is KUKA KMR mobile robot equipped with KUKA LBR iiwa collaborative manipulator. KMR robot localizes itself by fusing sensory information from the wheel encoders and laser scanners alongside sensor fusion of UWB tags and beacons. Mobile manipulator movements are planned with obstacle avoidance by solving a numeric optimization problem which takes into account of a continuously updated digital representation of the environment.
Risks and limitations
A thorough functional safety analysis is required before deployment. The demonstrator is made on KUKA KMR iiwa.
Technology readiness level
5
Sectors of application
Manufacturing, .
Potential sectors of application
medical sector, service sector and food sector can also deploy this technology with necessary constraints
Hardware / Software
Hardware:
KUKA iiwa KMP200 omnimove
Robotiq 3 Finger Gripper
External PC
Software:
KUKA sunrise
ROS/ROS2
Photos
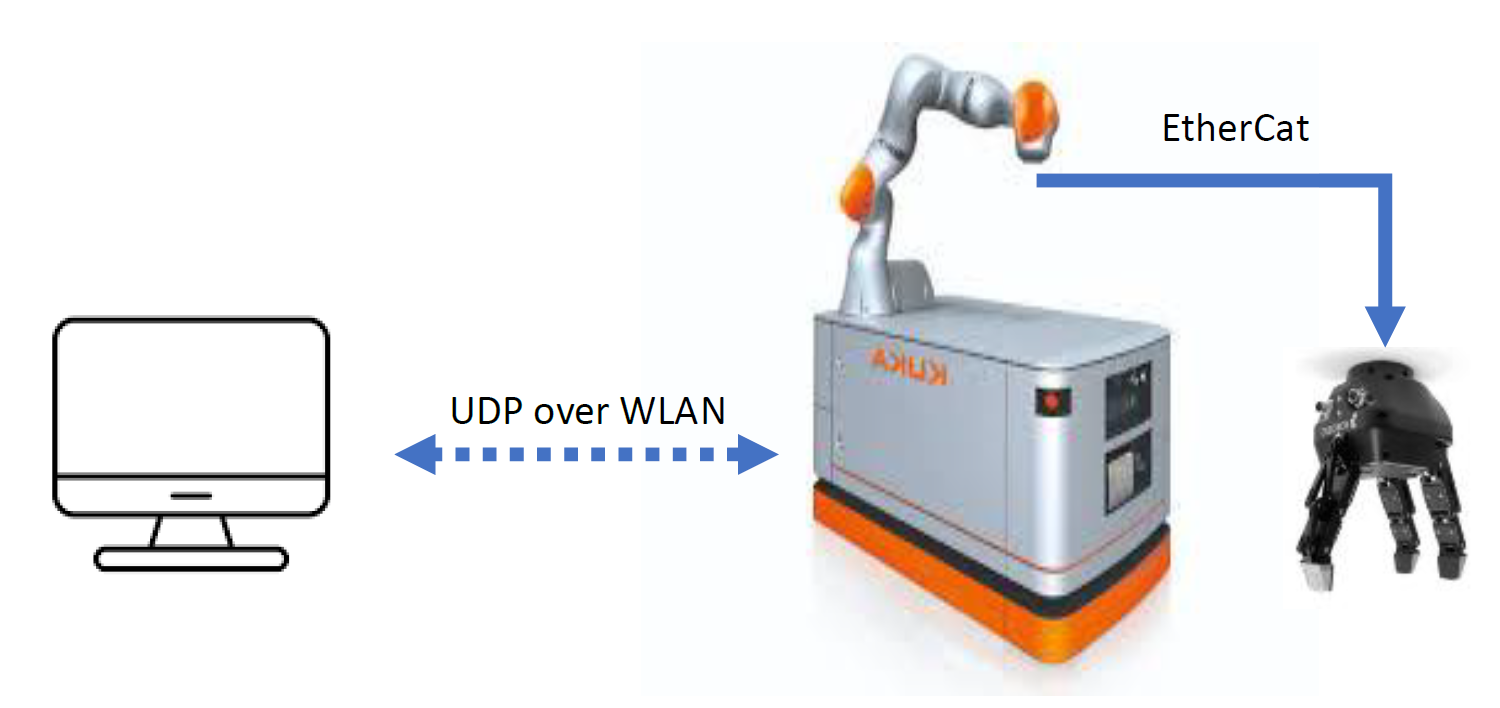
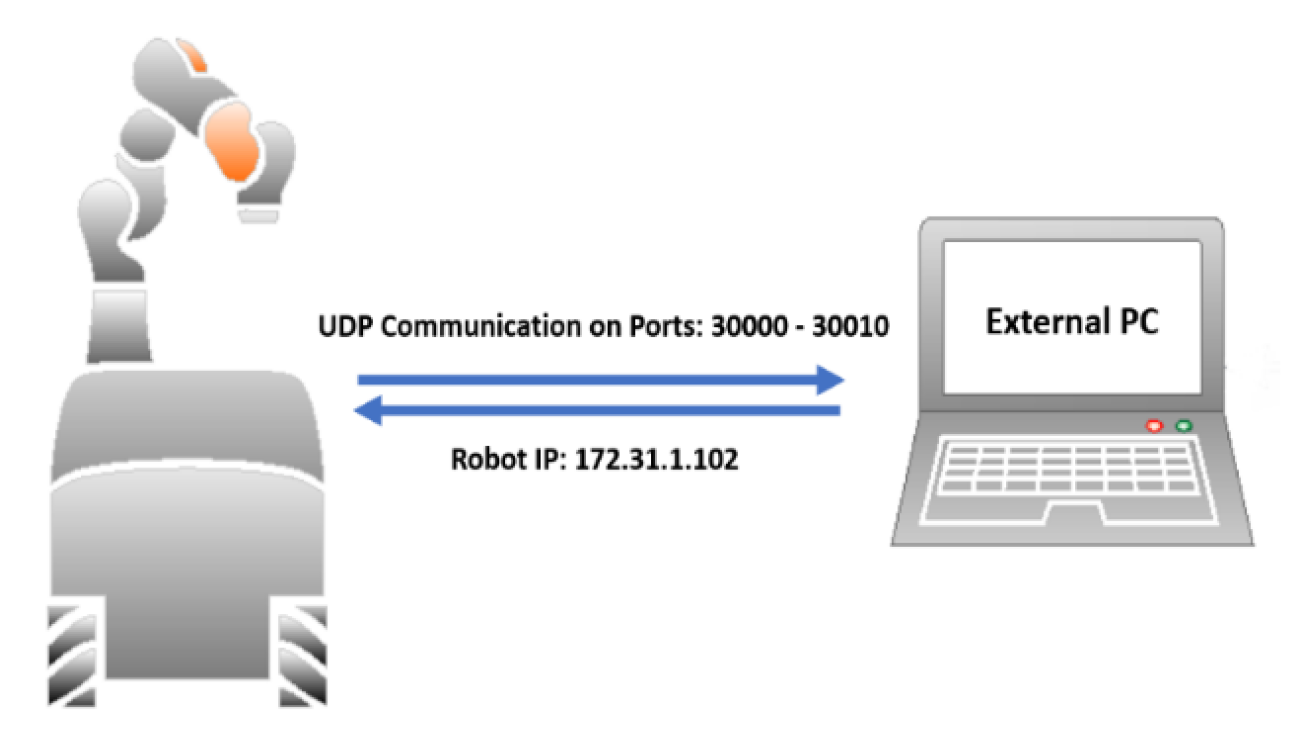
KMR External Control Module
This module allows to control a KUKA KMR from an external PC. With this module, programming a specific appl...
LEARN MORE
UWB based indoor localization Module
To introduce mobile manipulators in industrial settings localization capabilities need to be added. We use ...
LEARN MORE
Trainings
To learn more about the solution, click on the link below to access the training on the Moodle platform
Deployment of mobile robots in collaborative work cell for assembly of product variants